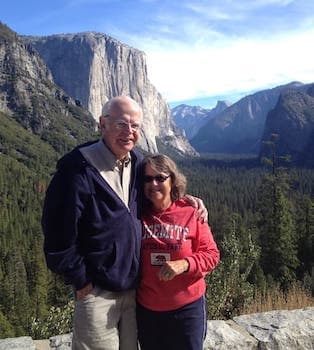
Curated with aloha by
Ted Mooney, P.E. RET
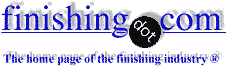
The authoritative public forum
for Metal Finishing 1989-2025
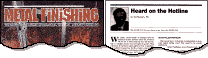
-----
Wear coating for S-7 Tool Steel or stainless? TiN, TiCN, Armoloy TDC, QPQ?
Q. I am looking for a wear resistance-low coefficient of friction coating to apply to 304 stainless which can be economically processed (many hundreds of parts at a time) . The final surface finish would be 6 micro.
It is used in a reciprocating pump and seal abrasion is the enemy.
I have tried: Hard Chrome, TiN, Armoloy, Melonite QPQ.
I would appreciate any help anyone can offer. I do not mind being solicited by suppliers.
James Cook- Ramsey, Minnesota
1998
A. James,
ID or OD? How thick a layer of chrome did you put on. What chemicals and abrasives is it up against. Tight tolerance and speed? Have you considered a ceramic sleeve or liner as appropriate. One of the high energy plasmas like tungsten carbide followed by grinding might work if that is "cost effective".
- Navarre, Florida
1998
A. Resin-bonded dry film lubricants may solve your problem. These products are applied like paint and cured. They are not inherently hard, but rather are designed to carry high loads while reducing sliding friction. Numerous products are offered by various material suppliers. You will probably need help from a qualified applicator to pick the right formulation for your pump shaft.
Chris Jurey, Past-President IHAALuke Engineering & Mfg. Co. Inc.

Wadsworth, Ohio
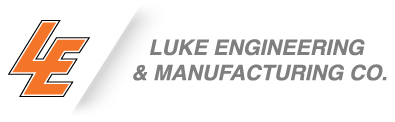
1998
A. You might consider using electroless nickel or an electroless nickel composite plating process that incorporates Teflon as occluded particles within the nickel plate.
Perhaps CrN would work better than TiN.
Blair Smithaerospace - Windsor Locks, Connecticut
1998
A. Had a similar problem on percussion drills , laser nitriding gave the best results, but that was cavitation corrosion . Perhaps combining hard chrome with laser nitriding might work , I remember the system being used on moulds in the early eighties .
Dave Brackenridgeaerospace plating - Germiston, South Africa
1998
A. Sputter deposited MoS2 coating is the low friction you coating you are looking for. This is a physical vapor deposited coating resulting in very high levels of adhesion, density and purity.
Regards,
Andy
- Dayton, Ohio
1998
A. You may find good results with Electroless Nickel containing particles CFX, a cousin of PTFE, but more tolerant of heat. The system fights corrosion and wear. The process will coat multiple parts at the same time with a uniform coat thickness. Hope this helps.
Robert L. Stone- coating specialist
1998
Q. I'm very interested in the experience you had with QPQ.
Regards,
Erik van der Staaij- Maasbommel, The Netherlands
1998
A. You can put in your production the technology to spray all metals including stellites by HVOF wire . Ra finish can be up to 3 as sprayed. No thickness limitation and no stress. Up to 7000 times more resistant than chrome deposition.
Other solution used for turbines for aircraft are Nickel-graphite abradable material which are essential for sealing turbines axes and resist hot corrosion and impact of particles (like sand on the turbines when the plane is flying in the desert)
Yves PlusquinBELGIUM
1999
1999
Q. Hello.
I'm a Mech. Engineer at Deluxe/Bostitch in Chicago, IL.
I'm looking to coat a piece of S-7 tool steel in order to reduce wear. It currently slides on a piece of C1018 and is wearing very quickly.
I'm currently looking at Armoloy, & TiN/TiCN. Armoloy is applied at a low temperature. It costs twice as much as TiN (which is not really an issue), but the cost for several prototype pieces is prohibitive. TiN/TiCN is applied at approximately 950 deg F, which will unfortunately reduce the hardness of the S-7 from 56-58 Rc to approximately 50-52 Rc. Prototype cost is negligent.
Can someone recommend a possible alternative to Armoloy or TiN/TiCN which has similar wear and lubricity properties, and which will not affect the base material properties during the application process.
Any help will be greatly appreciated.
Thanks,
John JablonskiChicago, Illinois
A. Without getting into in what ways Armoloy differs from conventional hard chrome (if any), I will say that conventional hard chrome exhibits a very low coefficient of friction, a very high hardness, and excellent lubricity. It is used for thousands of similar applications and I doubt that it costs as much as TiN/TiCN, let alone more. Because you will be able to get it done by a large number of shops, the prototyping costs should not be extravagant., but it does cost some time (and consequently money) to get the part fixtured right.
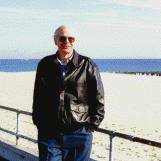
Ted Mooney, P.E.
Striving to live Aloha
finishing.com - Pine Beach, New Jersey
1999
A. I am somewhat surprised that hard S-7 is being worn by a 1018 steel. I would look at hardened Electroless nickel also. Its normal hardening temp is about 600 F, but it can be hardened at lower temperatures but takes a lot longer. Another alternative is low phosphorous EN. It comes out hard and can be further hardened. EN and chrome have fairly similar lubricity. EN goes on very uniformly and does not require grinding, which will save a buck. I would look at 1.5 mills thickness.
James Watts- Navarre, Florida
1999
A. PVD- TiN/C can be applied at lower temperatures. You might want to look at PVD-chromium nitride which has better lubricating properties than TiN.
Donald M. MattoxSociety of Vacuum Coaters
Albuquerque, New Mexico
"Handbook of Physical Vapor Deposition (PVD) Processing" (2010) [on AbeBooks or eBay or Amazon affil links]
and "The Foundations of Vacuum Coating Technology" (2018) on AbeBooks or eBay or Amazon affil links]
A. A very low temperature process that might be suitable is metal ion implantation. The processing temperature is very low -- under 200 °F -- and there is no change in dimensions -- it's not a coating process. We've found it greatly increases wear resistance if the problem is not adhesive wear. Our general implant combination is titanium and nickel, which we have used on many tens of thousands of metal cutting and forming tools. Typical life increase is 250%.
As noted by Don Mattox, PVD chromium nitride is also a possible choice, especially since it can be deposited at lower temperatures than TiN or TiCN. You may also want to look at Multi-Arc's MOST coating or Balzer's Hardlube, both of which are solid lubricant coatings deposited by PVD. I don't know the deposition temperature for Hardlube, but MOST is deposited at much lower temperatures than TiN or TiCN.
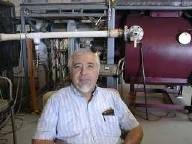
Jim Treglio - scwineryreview.com
PVD Consultant & Wine Lover
San Diego, California
2000
I must correct my previous response to your request. The Balzers Hardlube coating is a WC/C composite, not MoS2, and it is deposited at relatively high temperatures.
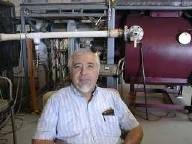
Jim Treglio - scwineryreview.com
PVD Consultant & Wine Lover
San Diego, California
2000
A. Try cryogenically treating the S7 to reduce the wear. It will maintain the hardness of the part.
F. J. Diekman- Streamwood, Illinois
2000
A. John,
have you looked at a composite nickel-PTFE (Teflon) coating? It is used extensively in the plastics molding industry for improved release/wear and lubricity properties.
Regards from PlaterB
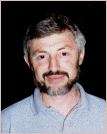

"PlaterB" Berl Stein
NiCoForm, Inc.

Rochester, New York
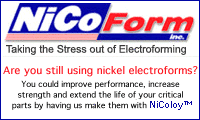
2000
A. Can you use a different tool steel with high wear properties and toughness like Crucibles CPM 3V. Look up the specs and you might find it suitable.
Dana Fike- Midland, Ontario, Canada
March 8, 2008
Q, A, or Comment on THIS thread -or- Start a NEW Thread