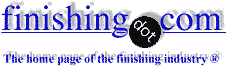
-----
Chromate conversion coating on screwed & glued aluminum

by Raj & Ali
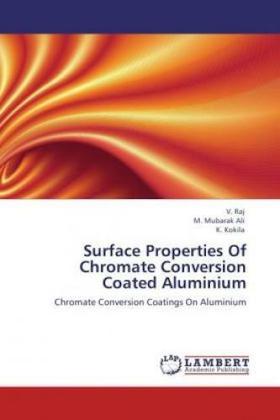
on eBay or Amazon
or AbeBooks
(affil link)
Q. I am looking for some guidelines or references regarding chromate conversion coating screwed and glued aluminum assemblies. Typically, chassis parts are fabricated from aluminum, cleaned, and then glued and screwed together. The stainless steel screws are countersunk and the screw heads are covered with an aluminum loaded structural epoxy. The entire assembly is then chromate conversion coated, primed, and painted.
While this approach has always been successful in the past, we recently has a chassis fail humidity testing. The epoxy over some of the screw heads is blistering/bubbling through the finish. We appear to have a corrosion or process control problem. It turns out that these particular chassis were also chromate conversion coated before the screw heads were sealed with epoxy. We are currently designing a test matrix to identify the problem and a corrective action - any suggestions?
Kevin Denning- avionics
1996
A. Kevin,
If I read correctly, these units were assembled, chem filmed, epoxied and then salt sprayed. If that is the case, I would expect at least one failure at a screw on nearly every box. Chemicals will wick around the screws, they are at most 85% thread and most likely helicoils. Customers that I have worked with, chem film the individual parts, let it dry for a day to set the film, then insert helicoils and then assemble. Touch up is sometimes required, but they work with care. PS, two hours in the Florida sun will set the film as much as 24 hours of setting. Low temp baking did not work,140 F is the max it can go to.
When you applied the epoxy and then chem filmed the assembly, you masked off the screws and holes. Your people were doing a good job if you had no failures before. Some leakage is almost a given with masking, and some operators are definitely better than others.
- Navarre, Florida
Q. The problem occurred during humidity testing - there was no salt spray test. As a general rule, our units are assembled, the screw heads are covered with epoxy, and the entire unit is chem filmed. The epoxy serves to mask the screws. The taps are usually blind.
The chassis which failed humidity testing was apparently chem filmed before and after the epoxy was added over the screw heads. The screws were probably not masked during the first chem film process. I strongly suspect that this is the source of our problem.
Kevin Denning [returning]- avionics
A. Kevin, I think you are correct. It very probably got some chemical in the threads from the first chem filming ,which did not rinse out, and became very active with the higher temperature of the humidity test.
James Watts- Navarre, Florida
A. My experience is that if you follow every wet process with a hot (140 °F min ) DI water rinse, life will be better. Spray or dunk with good flow ... about 3 - 5 Meg water min; hot air dry (no blotting papers) ... go to beach and relax!
Q. Now for a complicated problem ! I've some rather large aluminum parts at another contractor that have a wiped on clear chem film. Coating is not totally uniform in color but structures are covered -- does anyone have a simple test to demonstrate coverage?
Duane Barberaerospace - Sunnyvale, California
A. Dear Duane,
3 Meg water is no better than tap water if you have entrapped solution that bleeds out slowly.
If you say that the structure is covered by the chem film, then you don't need a test to demonstrate the fact, right? I know that the Bendix Corporation ignored the clear chem film portion of that MIL spec, and always asked for yellow to iridescent chromate, making inspection very easy.
I would like to know how the supplier demonstrates coverage to their own quality control system, whom I know they must serve. How do they determine that the aluminum is clean enough for the application of the film, and how do they know that all the surface was contacted by the solution? Do they have a spray or mopping pattern that the operator must follow?
Sincerely,
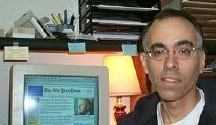

Tom Pullizzi
Falls Township, Pennsylvania
----
Ed. note: Other threads on similar topics include:
16006, "Chromate conversion coating aluminum parts having inserts"
56597,"Can Alodine/Iridite/Chromating be done with steel inserts already in place?"
Q, A, or Comment on THIS thread -or- Start a NEW Thread