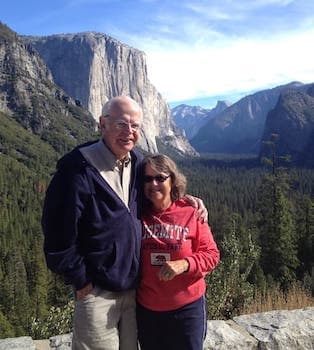
Curated with aloha by
Ted Mooney, P.E. RET
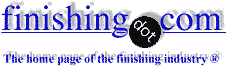
The authoritative public forum
for Metal Finishing 1989-2025
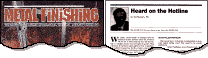
-----
Vacuum Impregnation and Plating
Would vacuum impregnation be useful/usable for rather larger openings such as the spot welded joints in chassis?
Is there some pore size / hole size that is too small for the sealant to enter or too large for it to span.
I understand that it is a vacuum process, but what actually draws the sealant into the pores--capillary action?
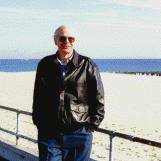
Ted Mooney, P.E.
Striving to live Aloha
finishing.com - Pine Beach, New Jersey
1996
1996
Generally vacuum impregnation is used to seal ferrous and non ferrous castings against pressure leakage. These can be pumps for oil, water etc. or cylinder heads and blocks for automotive applications. The major part of our business is with international automotive companies around the world. Others include electronic housings that require water tightness, etc.
There would not be any real benefit to seal spot welding unless they were in a pressurized environment and leakage was resulting from a pin hole in the weld. As a rule the porosity should be no more than 1/20th of the cross section that the defect is in.
Another application for porosity sealants is as a pretreatment for conversation coating - chromating etc. The benefit is to seal any voids that may otherwise trap the chemicals and spot out the surface finish. A regular component treated in this way is power metal parts.
Peter YoungThanks, Peter.
Regarding the spot welded chassis, what I was actually referring to is this: When such parts are placed in plating tanks, the aggressive cleaning, acid dipping, and plating solutions tend to wick into the joints. Later, of course, and over time, they wick back out and cause discoloration, staining and corrosion.
What is sometimes done is beads of sealants are run along all the edges to exclude the solutions. I was just wondering if vacuum impregnation might be a competitive technology for that application.
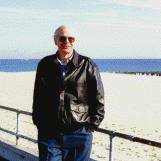
Ted Mooney, P.E.
Striving to live Aloha
finishing.com - Pine Beach, New Jersey
1996
From your description, vacuum impregnation may well be suitable for sealing for this application.
Peter Young1995
I will keep in mind a trial to see if vacuum impregnation is a viable alternative to the beads of sealant.
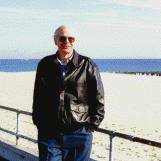
Ted Mooney, P.E.
Striving to live Aloha
finishing.com - Pine Beach, New Jersey
1996
Yes the porosity in the chassis should fill with sealant providing there is no relative structural movement in use and that the void is not so large that sealant will run out after impregnation. I believe a good guide is for the dia. of pore to be no more than 1/20th of its length.
Peter Young1996
Peter, you are probably right that the resin could fill the seams, but it may mean a redesign of the seam to make sure you don't have wide areas which won't be filled, thus still causing bleedout after an expensive operation such as impregnation. The idea is starting to appeal to me. I know we only did impregnation on investment castings for very expensive military equipment that required perfection. I can't see how the cost could be absorbed in a chassis costing a few dollars, but maybe there is a way.
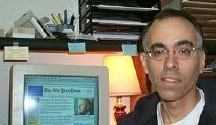

Tom Pullizzi
Falls Township, Pennsylvania
1996
1996
Tom Pullizzi
The cost of impregnation for military applications can be high due to certification etc. From a commercial point of view impregnation should not be expensive. Perhaps you could advise me of the size of the component and quantity and I will endeavor to give you a price guide.
1996
Dear Mr. Young,
Thank you for your offer. I would be very interested in the cost of impregnation of sheet metal boxes, just for the sake of argument. There might be many other applications.
The chassis, I suppose, are the ones that are used for electronic black boxes everywhere. say 6"x18"x16", some are open things with lots of nooks and crannys, some are more like a box.
As for the number of pieces, I'm sure there are millions, but not all of them will stand the cost of the added value of impregnation. Perhaps only a tiny percentage, used for critical applications, would ever be done this way. Who knows? Maybe one of your boxes will soon be on its way to Mars or somewhere.
I see many being plated in cyanide zinc, because of the better throwing power from the cyanide bath. I have no idea what it would cost to seal the seams of these boxes, relative to the total present cost of producing the box.
How would you do the estimate? I guess the cost is mostly a function of:
pickup and delivery of the boxes to the plant
labor to load the boxes in a carrier
dragout of the impregnate on the large surface area of the parts
amortization of the equipment
wastewater treatment
cost of heat for curing
regards,


Tom Pullizzi
Falls Township, Pennsylvania
1998
Tom
I've been thinking some more on the chassis. You may have seen earlier that I suggested to a reader that they may wish to think of vacuum washing of parts that get chemical entrapment. This is equipment we design and mfg. In essence the parts would be washed in a hot alkaline solution, vacuum dried in the same chamber, followed by chemical conversion and subsequent washes and further vacuuming as necessary. This all takes place in the same machine. The workload is first placed in suitable trays, bins, etc. Sub-division of the trays may be necessary for certain components that require protection.
The payload is rotated about a horizontal axis with the process solution cascading over it. It is shear volume of liquid that does the job - no nozzles to block! This equipment is sold to major automotive customers for chromating of aluminium castings, acid washing and alkaline washing. The cleaning is so great it beats ultrasonics!
Regards Peter.
Huh? You lost me, Peter. Are you suggesting that as long as parts are cleaned and rinsed efficiently, with ultrasonics or whatever, that people don't need vacuum impregnation or seam sealants after all?
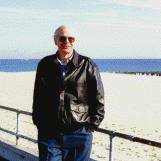
Ted Mooney, P.E.
Striving to live Aloha
finishing.com - Pine Beach, New Jersey
1998
I suppose the point that I was laboring is the need to ensure that the components are always as clean as possible.
There are two schools of thought in the impregnation world - whether to impregnate before or after chemical treatment. If in doubt it is worthy to sample test both ways. The limitation is what is available by way of impregnation processing. Most jobshop facilities offer traditional batch type processes with the major part of their experience with the sealing of porosity for pressure tightness - where surface cleanliness is perhaps less important. For surface finishing applications it is quite a different story - any sealant film left on the component, will of course mask against chemical reaction and cause unacceptable blotchyness of the finish.
To get around this problem, it is often recommended to chemical treat components first and then impregnate. The problem here of course is that corrosion could start in the entrapment if there is undue delay between chemical processing and impregnation.
Where chemical processing and impregnation are available side by side, the preference would be to first chemically treat. This is especially so where there is a risk of metal removal, exposing otherwise hidden voids that were not available for sealing at the time of impregnation.
Traditional batch processing impregnation can be made to work as a pretreatment, but it requires care and attention to effect the removal of surface sealant. It follows also that whether the impregnation process is used as a pretreatment or post treatment, itself has to be correctly applied - good positive vacuums using a good well maintained sealant are just as important.
Peter Young1998
Q, A, or Comment on THIS thread -or- Start a NEW Thread