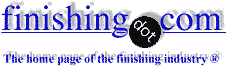
-----
Avoiding leaching of acid from anodized castings
A small portion of one of our pollution prevention projects involves the switch from organic coating of A356T6 aluminum to black sulfuric acid anodizing of the same alloy. The parts to be anodized will be used in sensitive (electronic and optical) aircraft systems, and there is concern that sulfuric acid may outgas or leach out at reduced atmospheric pressure. The limited information we have obtained indicates this is not a problem, but I need to be able to cite past work or other references to prove this is not a problem and why. What is the standard treatment of H2SO4 anodized parts to remove traces of the acid? Are there standards for residual H2SO4 in anodized parts?
Are certain black dyes better than others in sealing the surface? Is a certain coating thickness required to seal the surface for a given atmospheric pressure cycle? Can anyone provide references to past work in this area?
Troy Shaver- Johnstown, Pennsylvania
1996
Troy, three things I can think of that people do to get rid of the sulfuric acid to prevent bleedout include: hot and cold ('shock') rinsing, substitution by immersion in dilute nitric acid, and neutralization with sodium bicarbonate. I don't know offhand where to find articles on your specific problem, but I think a general literature search will not come up empty.
I know that Goddard Space Flight Center does some black sulfuric acid anodizing. Maybe you can find their webpage and leave e-mail to see if anybody there will help you.
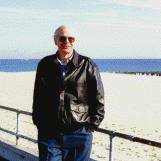
Ted Mooney, P.E.
Striving to live Aloha
finishing.com - Pine Beach, New Jersey
We have been successful with 356T6 casting for many years, and are currently Anodizing and Black Dyeing this alloy for a defense contractor.
It has been our experience that the quality of the casting makes all the difference toward the success of a good anodized and black dyed casting.
A good precleaning with a caustic and subsequent nitric/hydrofluoric desmutting is critical to the success of this process. A quality casting negates the necessity of special rinsing techniques. Anodizing and Black Dyeing of castings has been our speciality for many years.
Joe Hillockanodizing shop - Philadelphia, Pennsylvania
1996
I'm sure you will learn something useful in your research. Our finishing shop just anodized in the regular sulfuric anodize bath, drained the parts, rinsed in counterflow rinses, into the dye tank, rinse, into the seal tank, rinse, rinse, into a hot rinse, and blow dry. The parts looked nice; how much residual was left on the part, I don't know. The parts then went to the machine shop for more cutting, so they were probably cleaned a dozen times after that. Maybe after all the other operations, there was no acid left anywhere. There were all kinds of washes in the machine shop, degreasers, spray cleaners, etc.
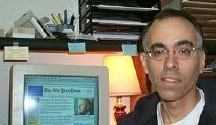

Tom Pullizzi
Falls Township, Pennsylvania
1996
Q, A, or Comment on THIS thread -or- Start a NEW Thread