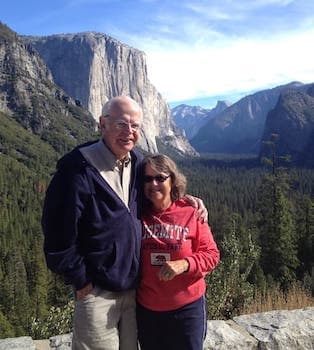
Curated with aloha by
Ted Mooney, P.E. RET
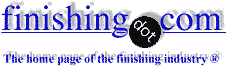
The authoritative public forum
for Metal Finishing 1989-2025
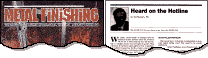
-----
Chemical roughening of aluminum surface
1996
I have a sample plate of aluminium which had been etched prior to painting.The surface is approximately a 63 micro finish and looks like a cast material but it isn't.I am looking for a process or a chemical to roughen the surface so that it can be painted. Painting bare aluminium without any preparation will be difficult-the adhesion of the paint to the aluminium will be poor.
If someone could give me some information about this I would appreciate it.
Greg Morrison1996
Hi, Greg. The general procedure usually recommended is MIL-C-5541 chromate conversion coating. This consists of caustic cleaning, etching in caustic, desmutting to remove non-aluminum constituents, then immersion in a dilute chromic acid based solution. This goes by such trade names as Alodine and Iridite. Companies like Atotech USA and Oakite Products [Chemetall] offer these conversion coating chemistries too.
This doesn't actually roughen the surface but it does impart corrosion resistance and paint adhesion. Good luck.
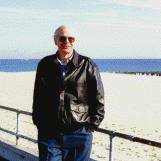
Ted Mooney, P.E.
Striving to live Aloha
finishing.com - Pine Beach, New Jersey
1996
Greg:
You might try the FPL (Forrest Products Laboratory) etch process which is commonly used in the aerospace industry. The following process has been successfully used at our facility:
- 1. Alkaline Clean (We use a non-etch product, TS-40A, available from Macdermid, at 150-180 °F, for 2-5 minutes.)
- 2. Immediately (before drying) water rinse. All alkaline cleaner residue must be rinsed off before proceeding to acid etch step.
- 3. FPL etch solution: 30 parts by weight (pbw) water, 10 pbw sulfuric acid, 2 pbw sodium dichromate, .20 oz/gal of 2024 aluminum alloy dissolved in sulfuric acid; 150-160 °F, 12-15 minutes.
- 4. Water rinse.
- 5. Force dry for 10 minutes at 120-140 °F.
- 6. Bond/paint within 4 hours.
You may also find similar information in ASTM D2651 "Standard Guide for Preparation of Metal Surfaces for Adhesive Bonding"
Blair Smithaerospace - Windsor Locks, Connecticut
1996
Greg,
It really depends on the type of application you have to determine the best pretreatment. the piece does not have to be visually "roughed up" to be receptive to painting. It needs to be clean or organics and inorganics, and relatively free of oxides.
Consider chromate conversion coating as being the "Cadillac" Also consider chromates being a heavy metal with disposal considerations weighing heavy.
Other types of precleaning includes 1) a phosphoric acid etch with some surfactants incorporated. This will clean, etch and provide some deoxidation. There are various proprietary products available.
Iron phosphates with fluorides incorporated with provide a light aluminum phosphate coating.
Very rough surfaces still have to be cleaned. They also require a lot of paint to provide a nice smooth coating. This can become an expensive proposition.
Hope this helps
Dan ZinmanFor ones and twos, grit blast it and immediately paint it with a primer for aluminum ⇦ this on eBay or Amazon [affil links] . Many paint stores sell one. It is a very poor substitute for chem film or anodize. You might be able to use naval jelly for aluminum, wash it in hot water, dry and prime immediately. Puts a poor mans phosphate coating on it. If it is in commercial quantities, you probably would be better off to ship it out. Consider a powder coater that does aluminum. It would be easier to comment on if there was more info.
James Watts- Navarre, Florida
1996
1999
You can try any of those products:
- Okemcoat 4500: 3 stages process: Alkaline cleaner 5% vol, Rinse and then OkemCoat 4500 5%vol : Products by Oakite
Or
- ROCC ( Reactive organic conversion coating ) More complicated then the Oakite process. 4 stages:
- Alkaline, Cleaner, ROCC and final rinse rinse
Both are offering a bonding between bare metal and coating. Powder coating can also be used or even an epoxy base paint and primer if UV radiation is not a concern.
Yvon Carrierlighting company - Boisbriand, Quebec, Canada
1999
All of the above are perfectly good suggestions. I have but one thing to add.
Selection of the pretreatment and coating material is usually based on the performance required of the finished product. You didn't say what the performance requirement was yet, so I can't help you select a pretreatment yet.


Craig Burkart
- Naperville, Illinois
Greg, I would like to suggest that you look into some of the new catalyzed polyurethanes for your top coat. There is a product that requires only a light etch (scrub) with a decontaminator, rinse and coat. ( apply 1 to 1.5 mil of topcoat) This product has been used extensively on anodized alum window mullions as well as other aluminum substrates. It is waterbourne and has a 10 year warrantee against uv fade. Conversion coating or acid etch is not required prior to coating.
Pete Bagley- Reno, Nevada
1999
Q, A, or Comment on THIS thread -or- Start a NEW Thread