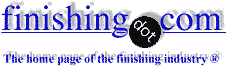
-----
Plating Electroless nickel directly onto aluminum

Q. Are there documented problems with application of electroless nickel directly onto 6061 alloy aluminum? The specification MIL-C-26074 [⇦ this spec on DLA] does not have any mention of concerns nor underplate recommendations. We have a customer that objects to our use of Ni over Al. They recommend a copper underplate and a Tin/Lead overplate (fused). What are the benefits to these additional layers and are they worth the additional costs?
Gordy Seppanenmaterials engineer - Minneapolis, Minnesota
1996
A. I have seen electroless nickel applied directly to aluminum--without a zincate treatment!--for connector housings. Reports were that it was satisfactory, but I never saw lab work verifying the adhesion, etc.
Zincate followed by electroless nickel seems to be the common & correct approach. I don't know what the advantage of an intermediary layer of copper is supposed to be. We have a few electronics plating gurus hanging around here, and hopefully one of them will chime in on that.
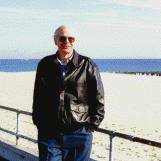
Ted Mooney, P.E.
Striving to live Aloha
finishing.com - Pine Beach, New Jersey
A. We always use zincate followed by electroless Ni with controlled P.
By the way, MIL-26074 has been canceled. We now use AMS2404.
aircraft
A. Gordy, does your customer object to the use of nickel in the product because of its magnetic properties, or is the customer just unaware of common plating practice? Sometimes you have to spend a bit of time to educate them. Although there are methods to apply copper directly to aluminum--see Durney,
Electroplating Engineering Handbook ⇦ this on
eBay,
AbeBooks, or
Amazon [affil links]
. They require uncommon chemistry and a bit of experience to be successful. If the problem is magnetics, you may be stuck trying to find a process supplier. If not, then take time to educate your customer on common aluminum finishing methods.
Good Luck,
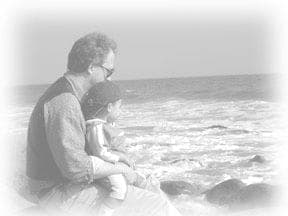
Dave Kinghorn
Chemical Engineer
SUNNYvale, California
Q. The customer objects because they believe that the Ni will crack during temp cycle (-55 to 85 C) exposing Al which will then lead to corrosion of the base material. The product is expected to survive 48 hours of salt spray.
I neglected to mention that we do Zincate the Al prior to Ni application, in fact we typically do a double Zincate.
I have found an internal program that tried Cu over Al and believe that the adhesion of plated Cu to Al is less than that of electroless Ni to Al. Unfortunately they did not document this testing. Any ideas as to where I might find such an adhesion comparison?
Thanks for all the comments!
materials engineer - Minneapolis, Minnesota
A. In addition to the traditional generic zincate,
Atotech offers their 'Alstan' tin-bearing pretreatment for aluminum, and Gumm offers their 'Bondal' process. Presumably these companies will be able to present quantitative data supporting their processes as being better than zincate.
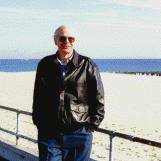
Ted Mooney, P.E.
Striving to live Aloha
finishing.com - Pine Beach, New Jersey
Ed. note: Fred Gumm Chemical Co. no longer exists, but the process perhaps can be found at MacDermid.
A. Gordy,
At this location we also double zincate aluminum prior to electroless nickel. I do remember that in one application we followed zincate with a copper strike which had a matching effect on the difference in coefficients of thermal expansion which sound like your customer's concern. I think we looked at it as a cushioning layer. I don't remember the specifics, but I remember doing it. We spoke last year about your zinc phosphate application question.
avionics Tampa, Florida
A. You may use a high pH electroless on double zincate, prior to ordinary electroless with PH about 4.8. This high pH EN plates a thin layer, protects zincate and gives very good adhesion. Sara


Sara Michaeli
Tel-Aviv-Yafo, Israel
A. As some people know, I sometimes find an answer looking for a question. I may have found one here.
I was just reading "pretreatment for plating on aluminum using the Stannate process by Jongkind and Seyb, aluminum finishing seminar, vol II, Proc. Conf., St Louis MO, 30 mar-1apr 1982, aluminum assoc. 818 Connecticut Ave, NW, Washington DC USA Met A, 8303-72-0144, 539-549.
It says that improved corrosion might be found by having tin next to the aluminum rather than zinc.
Maybe this would interest you.
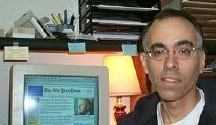

Tom Pullizzi
Falls Township, Pennsylvania
A. If your customer is really serious about this, do some comparative thermal cycling of both products. I doubt if you can beat the alkaline strike that Sara mentioned followed by an EN selected for its ductility and its ability to maintain it for the bath life. Most EN vendors probably will not want to spend a lot of time unless it is a lot of plating. I have seen papers from two vendors that address at least ductility and turnovers. I will put a cup of coffee on an alkaline EN followed by most any EN beating copper.
PS copper migration can cause real problems.
- Navarre, Florida
Q, A, or Comment on THIS thread -or- Start a NEW Thread