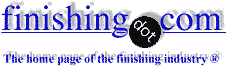
-----
Specifications & Standards for black oxide process
Q. I've been searching for black oxide specifications, particularly relating to coating of fasteners. I've found a general AMS black oxide spec but no others. My fastener supplier isn't much help either.
My company is moving away from Zinc plating due to repeated Hydrogen embrittlement problems and we need to specify the appropriate black oxide processes.
Do you have any suggestions?
Thank you
Mike
fluid management
1996
A. Hi, Mike. Here are some spec numbers: ASTM D769, AMS2485, MIL-DTL-13924
[⇦ this spec on DLA], MIL-HNDBK-205 -- there are others too.
Switching to black oxide should be a helpful step toward avoiding hydrogen embrittlement (acid causes hydrogen embrittlement,too), but note that the corrosion resistance of black oxide does not compare to zinc plating, and that there are reliable ways to address embrittlement except for extremely high strength fasteners.
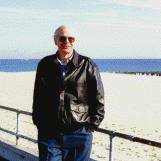
Ted Mooney, P.E.
Striving to live Aloha
finishing.com - Pine Beach, New Jersey
1996
1996
A. Mike - there is still the potential for hydrogen embrittlement. Some guidelines we have adopted:
- Use Mil-DTL-13924 (MIL-DTL-13924
[⇦ this spec on DLA]) specification instead of AMS2485, there are better controls in the Military specification and it provides details on correct processing for different materials.
- Do not use acid cleaning for high strength steels, vapor blast is effective for cleaning and surface preparation.
- Require a magnetic particle inspection (MPI) after the Black Oxide process.
- Oiling of the surface is required after Black Oxide, this oil must be removed to allow effective MPI and then the oil reapplied after inspection to assure corrosion protection.
- Acid stripping and re-coating cycles will compound a hydrogen absorption problem since the part is exposed to the acid longer.
- Use hooks and fixtures made of iron or steel, and mask parts of assemblies that are not ferrous material to prevent corrosion contamination of the bath.
- The Black Oxide processing time must be closely controlled to prevent intergranular attack (IGA) and alkaline embrittlement.
aircraft engines
A. Mike, would you be willing to look at a new PVD plating process for hydrogen-embrittlement-free zinc? No post bake is required. Perfect for high strength steels. Ted is correct, black oxide will not provide sacrificial properties.
Mandar Sunthankar- Fort Collins, Colorado
1998
A. Hi, Mike,
I believe that the zinc black oxide process is still a good choice for your applications because of its convenience and cost-efficiency.
Hydrogen embrittlement is caused by zinc plating and acid pickling not black treatment. Actually, zinc plating has the least risk of hydrogen embrittlement relative to other metal platings because the electrochemical resistance of hydrogen evolution is quite high on zinc. If zinc plating process is properly controlled with right pH range, current density, temperature, time, and additives, hydrogen embrittlement can be minimized. You may notice that zinc plating has almost 100% current efficiency, which means almost no hydrogen evolution on parts during plating.
Baking should be processed immediately after zinc plating at >200 °C for at least 4 hours. This is able to eliminate hydrogen in parts completely. Then the baked parts should be activated in either dilute sulfuric acid or nitric acid, depending on black formulations, and thoroughly rinsed in tape water and DI water respectively immediately before blackening treatment.
- Grand Rapids, Michigan
1998
Mr. Hao, Your comments are correct, except you didn't mention that the 100% efficiency only applies to Acid Zinc. I think this is important, since Cyanide zinc is quite different in respect of hydrogen embrittlement.
Carlos CielakMexico City, Mexico
1998
A. Zinc has a higher plate out voltage in alkaline solution which can decompose more water into hydrogen (but there is less of it so you get alkali cations which can't be baked out, could be your issue?). Hydrogen voltage also higher in alkaline solution. Cyanide just brings the Zinc voltage down closer to Hydrogen. Acid Zinc still higher voltage than Hydrogen but less of difference. (Cadmium and Nickel-Tin plate at lower voltages so less Hydrogen.) Best corrosion resistance and anti-seizing etc is the Zinc-Nickel and Zinc-Cobalt; commonly used for deck screws for treated wood. Electroless Nickel (high Phosphorus) is hard and reasonably corrosion resistant but brittle.
Best Black Oxide on Steel was hot Red Fuming Nitric Acid; not a nice thing to handle. At another shop the Copper plating line stripper (Nitric Acid, N2O4, copper nitrate
⇦ on
eBay
or
Amazon [affil links]
) would strip copper and passivate Titanium and turned Steel Black (not from Copper).
Re the acid/hydrogen connection: Nitric Acid oxidizes Hydrogen, esp. in higher concentrations. I've seen electrolytic anodization with nitric acid, but not small hardware.
You might check with your vendor re what steel they are supplying. Type 440 has less hydrogen embrittlement issues than Stainless. You wouldn't be the first shop to zinc plate stainless steel.
- Mount Vernon, Washington, USA
July 24, 2011
Q. What is the difference between Mil-C-13924 and MIL-DTL-13924 [⇦ this spec on DLA]?
Tom Fischerspring mfgr. - Maumee, Ohio
2002
A. The newer DTL version requires a bake for embrittlement relief. It's tough to bake black oxide which has little if any protection by itself without it rusting. Baking it with oil is a smoky and stinky proposition.
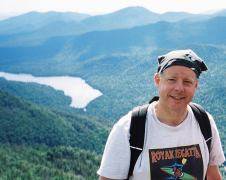
Milt Stevenson, Jr.
Syracuse, New York
2002
GM 4276-M specification for Black Oxide
Q. My name is Teppei Kojima with a bolt company. I would like to obtain GM 4276-M specification for Black Oxide. Currently we are trying to supply a fastener to Delphi. On the drawing, there is a note that Phosphate coat and oil per GM4276-M, 5% red rust permissible after "24" hour salt spray test. I would like to know about GM 4267-M so that I can find oil or wax to pass the test
Thank you
- Garden Grove, California USA
2003
A. GM standards, as well as many others, can be purchased from Global Engineering at www.global.ihs.com.
Cynthia L. Meade- Sylvania, Ohio, USA
2003
Q. I am in need of the correct specification to put on a drawing for a 0.156' dia. pin about 1" long. The pin will be case hardened 1018. I would like to have the "Lustrous Black Oxide" finish as you see on some commercially available hardened dowel pins.
The coating should not change the 8 RMS finish on the pin surface, build up on the pin surface or have a matte appearance. The coating should have about the corrosion resistance of blueing like you see on firearms.
A spec or even general notes I could use on the drawing would be most helpful.
Many thanks,
Chief Engineer - Bridgeport, New Jersey
2004
A. See "FAQ: Black Oxide and Cold Blackening" The basic spec is hot black oxide per MIL-DTL-13924 [⇦ this spec on DLA] (or AMS2485), but I suggest modifying the pre-and post-treatments. Pretreatment usually includes an HCl dip to remove rust, which may damage your surface finish (and perhaps add hydrogen to the part). Minimize this acid dip. The final treatment is usually a dip in water-displacing oil; you may prefer a dry-to-touch glossy wax. Run sample parts; a slightly finer initial finish may be needed to compensate for any deterioration.
Ken Vlach [deceased]- Goleta, California

Rest in peace, Ken. Thank you for your hard work which the finishing world, and we at finishing.com, continue to benefit from.
2004
Q. I am a mechanical design engineer, designing/specifying parts for my company to buy. On many parts (screws in particular) we ask for "black oxide." We'd like to get more exact with this specification. Is there an ASTM or similar specification we could reference? Is there a recommended thickness?
Jeff Mattlinelectronics - Saint Louis, Missouri, USA
2004
A. There is a very helpful article by Robert Farrel Jr. in the 2004 Metal Finishing Guide. This should help with your questions.
Paul Ellingsonplating - Wahpeton, North Dakota, USA
2004
Multiple threads merged: please forgive chronology errors and repetition 🙂
Q. Hi,
I am Khemandas Chute working as process engineer desire to start the blackodising process for our tools, jigs, fixtures. I don't have any information about blackodising process. I want to know the chemicals used & process details, so that I can be able to start this process.
Sr.Engineer - Aurangabad, Maharashtra, India.
2007
Q. Please give the detailed process of blackodising & chemicals used for this process. I need this information for my knowledge & study. Many of our components are blackodised but nobody is thoroughly knowledgeable about the process.
Ravindra JawalePart of the mechanical company - Pune, India
May 5, 2008
A. Hi, Khemandas. Hi, Ravindra. In addition to the specs, you can get an intro via our FAQ on Black Oxide & Cold Blackening; and there is a good chapter in the Metal Finishing Guidebook. Many people use proprietary chemistry rather than having to try to independently develop an optimum formulation, but expired patents may point the way to workable mixes although not the latest technology. Good luck.
Regards,
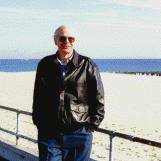
Ted Mooney, P.E.
Striving to live Aloha
finishing.com - Pine Beach, New Jersey
May 10, 2008
GEC- Marconi spec for black oxide, S114
September 17, 2012Q. We are trying to locate a GEC- Marconi spec for black oxide, S114. Their drawing calls for black oxide per Mil-C-13924 Class 1 & S114. Does anyone know what may be required by S114 over the Mil spec?
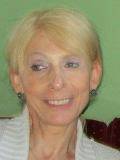
Victoria Kaye
- Hauppauge, New York, USA
Q. What all are blackodising standards?
Ajay Saxenacase new holland - indore, mp, India
April 1, 2013
A. Hi Ajay. As you see, we appended your question to a thread which already answers it, but get back to us if you have further questions. Good luck.
Regards,
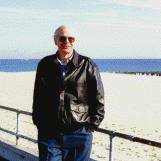
Ted Mooney, P.E.
Striving to live Aloha
finishing.com - Pine Beach, New Jersey
April , 2013
Q. Hi, can someone send me the AMS2485 specifications; am fed up of searching it on the net, could not download it -- please someone send it to me.
Prakash rajoil and gas equipment manufacturing - dubai, UAE
August 13, 2014
A. Hi Prakash. Please clarify ... We've linked to it multiple times just on this page alone, so no searching is needed at all, and it seems to download fine. Are you saying that you could not find any site that would accept your credit card for the download, or are you saying that you could not find it for free? It's a copyrighted specification, and it is not free because there are serious costs involved in maintaining it; it is contrary to international law for anyone to copy it and send it to you. Sorry, and good luck.
Regards,
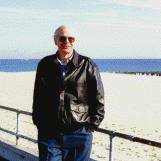
Ted Mooney, P.E.
Striving to live Aloha
finishing.com - Pine Beach, New Jersey
August 2014
Q. Hello,
Somebody who knows about process the Black oxide for class 2 please let me know. Thank you.
- Hermosillo, sonora, Mexico
September 18, 2014
A. Hi Hernando. You would need to know the spec number you want, not just a class. But assuming you are thinking of MIL-DTL-13924 [⇦ this spec on DLA], it's available for free from the referenced link. Good luck.
Regards,
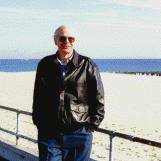
Ted Mooney, P.E.
Striving to live Aloha
finishing.com - Pine Beach, New Jersey
September 2014
Q. Hi,
I have been asked to comply with spec ESF-M6P3-A for a black oxide procedure. I already bought the spec, but it does not describe the method, it's very general. What can you tell me about this?
Do you think MIL-C-13924 C Class 1 will do?
Thanks!
- Monclova Coahuila Mexico
September 30, 2014
A. Hi Francisco. Ford and other automotive specs are usually pretty rigid -- I'm surprised this one isn't. If you've read it and it has no real requirements, then I think you're right that MIL-C-13924 Class 1 should be a good guide. Best of luck.
Regards,
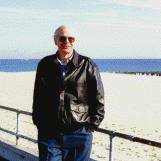
Ted Mooney, P.E.
Striving to live Aloha
finishing.com - Pine Beach, New Jersey
November 2014
Does MIL-DTL-1392D Class 4 (black oxide on stainless steel) require an added preservative?
MIL-DTL-13924D Class 4 for stainless steel. The specification calls for an added preservative after the black oxide process. Is the added preservative needed? Is there any advantages for using the preservative?
Cesar Duron- Albuquerque, New Mexico USA
November 11, 2014
A. Hi Cesar. That's an excellent question because there is a difficulty in that spec.: Section 3.4 says the section applies to Class 1 and 2; then subsidiary to that, section 3.4.1 says "all classes"" require rinsing, and section 3.4.2 says chromate dip is required after the rinsing. My read is that the reference to "all classes" in section 3.4.1 means "all classes within Class 1 and 2" and does not include Class 3 or 4 -- especially because, for Class 4, a salt spray test is required which it must pass before any post-treatments.
Luck and Regards,
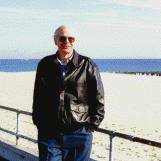
Ted Mooney, P.E.
Striving to live Aloha
finishing.com - Pine Beach, New Jersey
November 2014
Q. Thanks for info Ted. After going over section 3.11 (Supplementary preservative) the section does not state a class, meaning no preservative is needed for a class 4 finish -- is that correct?
Cesar Duron [returning]- Albuquerque, New Mexico USA
November 12, 2014
A. Hi again, Cesar. Section 3.11 basically says that you have to comply with your customer's specifications and requirements regarding supplementary treatments.
Now I've realized that I wasn't reading between the lines -- and I am guessing now that you are not a finisher trying to comply with a spec, but a designer trying to figure out what you should specify?
I don't think anyone -- certainly not me -- can help you write a spec for which I have no idea of the requirements :-)
If you believe the application is such, and the environment will be such, that passing the salt spray test will prove to be a sufficient requirement, then MIL-DTL-13924D Class 4 without a supplementary treatment should cover you, but I have no basis for presuming that MIL-DTL-13924D Class 4 is an appropriate finish for your application. Good luck.
Regards,
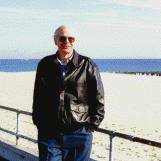
Ted Mooney, P.E.
Striving to live Aloha
finishing.com - Pine Beach, New Jersey
November 2014
Q. Hi Ted,
I am inspecting the product sent by the supplier and the added preservative that is being used is excessive. What I am trying to figure out is if the added preservative is needed to add protection to the black oxide or will it be okay with no preservative.
The black oxide is applied to a stainless steel bolt and used in normal weather conditions.
Thanks,
- Albuquerque New Mexico
November 12, 2014
A. Hi. If you're sure the coating is not also doing duty as a thread lubricant or anti-galling agent, and if the non-preserved parts did pass the required MIL-DTL-13924D Class 4 salt spray test, my guess is they'll probably be alright. I know it's not always possible to do elaborate field testing, but I'm not a big believer in proceeding from book knowledge to important production without testing, so test what you can to the extent you can :-)
Regards,
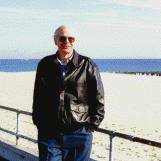
Ted Mooney, P.E.
Striving to live Aloha
finishing.com - Pine Beach, New Jersey
November 2014
Acceptance criteria of blackening parts
Q. I do inspection of many blackening parts , Many parts have often defect like red/ grey smut, pitting, burning etc. Is there any acceptance standard available?? If yes let me know.
- AHMEDABAD India
August 24, 2019
A. Hi Pintu. Although I would feel that the parts are unsatisfactory if they are red or smutty, or pitted or burned (how do parts get 'burned'?), they are hopefully being processed in accord with some specification. The starting point is always to determine what the requirements of the specification are. That specification may have acceptance criteria, but also required inspection procedures. Good luck.
Regards,
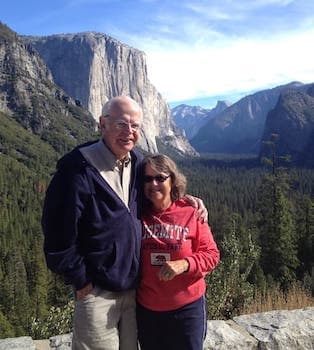
Ted Mooney, P.E. RET
Striving to live Aloha
finishing.com - Pine Beach, New Jersey
August 2019
A. Pintu, first let us know what type of black oxide process you are using. If it is a mid temp 129-132 °C bath comprised of NaOH and oxidizers like sodium Nitrate and Nitrite, I would suggest the bath is being overloaded and the temperature of the bath dips too low for too long when the parts that display that defect are introduced. Also check out MIL-DTL-13924 [⇦ this spec on DLA] for QC, should be able to find a free download online somewhere. Hope this helps.
Jordan EgnatoffPlating QC Chemist - Huntington, WV USA
September 10, 2019
Q, A, or Comment on THIS thread -or- Start a NEW Thread