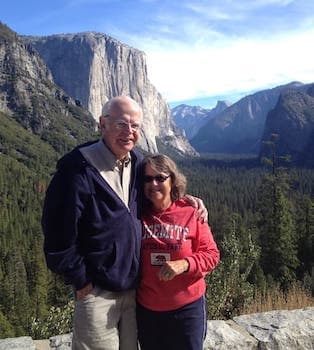
Curated with aloha by
Ted Mooney, P.E. RET
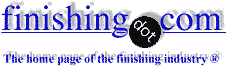
The authoritative public forum
for Metal Finishing 1989-2025
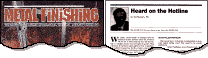
-----
Acid zinc plated screws have dark spots
Dear Sirs,
I am an assistant manager of a screw plating factory of Malaysia. I am confused about the brightness of the screws which is coated with acidic zinc plating. Sometime I found that was dark in the middle of the screws after put into the hot water, especially the long screws. And sometime it was dimmed. By the way, I am using the barrel to plate.
The main components of the chemical are Zn, KCl and Boric acid. I think I don't really catch the function of these chemical although I know about the analysis method of them.
Another problem is I have no idea about the brightener and carrier, neither the function nor the analysis method. May I ask you for the "Hull Cell" method ? I'll be very appreciative about this.
Your Sincerely,
- Malaysia
1996
Hi, FC. It is hard to determine exactly what is going on from here, however: I would be very concerned that the middle of the long screws may not even have any zinc plating! How do you test the thickness? Assuming I am wrong, and I certainly hope that I am, I'm not quite sure what is happening, but it seems that--even though you are barrel plating--you are getting higher current density, and thus brightness, on the ends. Sometimes excess iron in the bath deposits in the low current density areas and is much darker than the zinc.
The zinc provides the metal, the KCl is the conductive plating salt, and the boric acid is a pH buffer.
If you don't understand the function of the brightener and carrier and how to analyze it, you must get a supplier in to get you started. Usually you can't fully analyze for these proprietary components, but have the supplier periodically analyze and base your interim additions on Hull Cell results.
A Hull cell is a small open top plating tank (267 ml) which, viewed from the top, is trapezoidal in shape so that the cathode is quite close to the anode at one end and far from it at the other. This allows determining whether the problem is in low current density areas, high CD areas, or across the range. It allows you to test additions before scaling up to the actual tank.
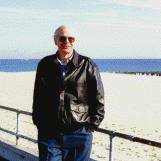
Ted Mooney, P.E.
Striving to live Aloha
finishing.com - Pine Beach, New Jersey
1996
Your problem may be temperature. Acid zinc baths work best at about 65 F-70 F. The Cl component is for both conductivity and anode corrosion. The Boric acid is to buffer the chemistry right on the surface of the workpiece(screws) while the plating reactions are going on, as a lot of hydroxide (OH) may be formed, especially in a barrel. The brightener is usually a sparingly soluble organic acid, therefore you usually need a second brightener component, the wetter, to fully solubilize the brightener. Most brighteners can be titrated as any acid but you must extract them from the plating chemistry first. Usually this is done by shaking 50 mls of plating solution in 250 mls diethlyl ether in a separatory flask, then let the organic and aqueous phases separate, and drain off the aqueous phase and titrate the organic phase. The wetter is determined by a stalagmometer(drip-counter). Dark in the middle of the screws is either caused by low Zn, Low Brightener, too much current, or high temperature which is causing the brightener to "oil-out." The brighteners , even with sufficient wetter, still tend to separate out at higher temperatures. I used it to plate 180 tons per day of screws, nuts, & bolts for Armco Steel in Kansas City. Also carbon treat often. But Temperature, Brightener Balance, and electrolytes are the important parameters. Good Luck,
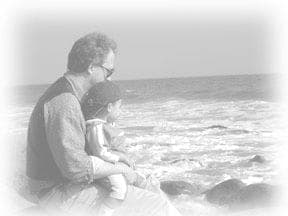
Dave Kinghorn
Chemical Engineer
SUNNYvale, California
1996
Hull Cell conditions are: 2 amp, 5 min, room temp, mechanical agitation. After plating in Hull Cell rinse, dip shortly in 5% nitric acid and rinse again. Deposit is allowed to be strip in nitric from the back of panel but if it strips from the front it means your covering power is bad and you probably have no deposit where you observe the problem. In this case add carrier. A lot of problems in acidic zinc are related to lack of carrier. do not hesitate to add carrier as extra carrier is not harmful.
You might have another problem - iron contamination. Do you add hydrogen peroxide at least once a week? It is essential to add it as iron always accumulates in this solutions. you can also add potassium permanganate
⇦ this on
eBay or
Amazon [affil links] instead of hydrogen peroxide.


Sara Michaeli
Tel-Aviv-Yafo, Israel
1996
We have a feature article on line here that you may find helpful: 'Improving your Chloride Zinc Plating Operation'
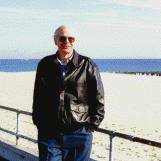
Ted Mooney, P.E.
Striving to live Aloha
finishing.com - Pine Beach, New Jersey
1996
In acid zinc Plating the brightener(R) gives the eye shine but the additive(M) plays a major role as an inhibitor to avoid corrosive effect of HCl acid in the Acid Zinc Plating, but if the additive(M) is excess means the plating becomes dull in the threaded portion.Hence make a dummy treatment using 0.5 volts for minimum of 3 hours so that the excess of additive(M) deposits on to the dummy and be careful while removing dummy don't switch off the rectifier, because if you switch off the current the organic impurities shall return to the bath. Always add M in alternative days calculating Amp hours worked or to be worked also make it a point that Degreasing in hot soak metal cleaner is very important before going for acid pickling. Periodically check for iron content and give a treatment using peroxide, caustic & Permanganate to purify the bath monthly.
C.PRAKASHAM- Chennai, Tamil Nadu, India
March 26, 2009
Q, A, or Comment on THIS thread -or- Start a NEW Thread