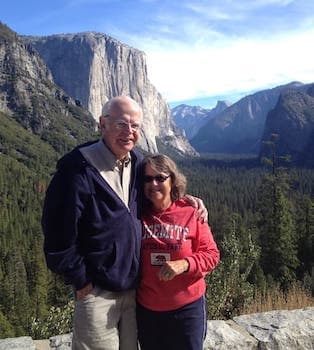
Curated with aloha by
Ted Mooney, P.E. RET
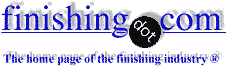
The authoritative public forum
for Metal Finishing 1989-2025
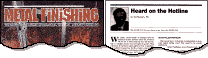
-----
Tell me about Mechanical Plating
Q. I would like to know about mechanical plating. What type of plating it is, what is the process and what are the equipment required for the same ?
Pankaj K. Shah- Mumbai, India
1996
A. Mechanical plating is the application of a metal surface coating by peening. In practice, the parts, the metal powder, and small glass beads are tumbled in a barrel. Because of the minuscule contact area between a spherical bead and the part, very large pressures develop--sufficient to pound the powder onto the substrate.
It is widely practiced and economical. The basic limitations are that it is not a decorative finish, and only reasonably soft metals (zinc, tin, and cadmium) are amenable.
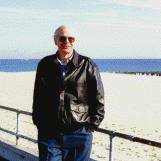
Ted Mooney, P.E.
Striving to live Aloha
finishing.com - Pine Beach, New Jersey
1996
1996
Q. I am familiar with mech. plating with Zinc as a substitute for hot dip galvanizing.
Can you use the process as you have suggested to plate Aluminum or Copper with Tin?
Is there a standard for the process, ASTM?
A. Tom Rochester [of Plating Systems & Technology, a finishing.com supporting advertiser], Jackson, Michigan is a premier supplier of mechanical plating & galvanizing systems; I'm sure he can answer your questions regarding ASTM specs and whether they can put tin onto copper and aluminum.
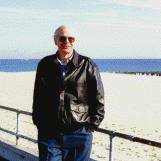
Ted Mooney, P.E.
Striving to live Aloha
finishing.com - Pine Beach, New Jersey
1996
1996
A. This is in response to Lee Heron's message.
Because we use glass plating media in our plating process, we must have a reasonably efficient way to separate our media from the parts that we run. In most cases we use a magnetic separator at the end of a surge hopper which extracts the finished product and the glass media goes below the separator into a holding tank. For this reason plating very large amounts of non-magnetic parts proves to be inefficient and quite time consuming. We are however doing production runs of copper parts (in small lots) that are getting silver plate. So yes we can plate on copper and aluminum.
Some of the metals we plate with are Zn, Al, Sn, Cu, Ag, brass, bronze, and we also can use combinations such as tin-zinc.
I work in a mechanical galvanizing/plating plant and would be more than happy to try to answer any questions anyone may have in regards to this process.
Q. We have a customer requesting that we plate our externally threaded fasteners with mechanical zinc vs. electroplated zinc.
The typical size of our products is 10-32 / M5 and approx. .550" in length.
Does anyone have experience with threads gauging or not gauging after mechanical plate? Is it as reliable for thickness as electroplate.
Thanks for your help,
- Danboro, Pennsylvania
1996
A. This message is in regards to Pat Kelly's question regarding the gauging of threaded fasteners after being Mechanically Plated.
I have worked in the Mechanical Plating industry for over twenty years and have seen millions of fasteners plated with no detrimental effect on the gauging properties of the threads. If anything Mechanical plating will reduce the "peaks and valleys" commonly associated with the an electro-deposited coating. We currently plate thousands of pounds of externally threaded fasteners every day. The absence of the hydrogen related failures has made Mechanical Plating a heavily specified coating in the Automotive field for decades.
As far as the coating thickness properties, there is a wider range of thickness variability on an individual fastener than in an electroplated coating, however the batch to batch variation is more precise than in electroplating. New technology has shown CpK values in excess of 1.3 in our experimental and production runs using this new technology.
My conclusion is that there are no detrimental effects on thread gauging caused by the use of Mechanical Plating. Its continued use in all Industries where "Hydrogen Embrittlement" is an overriding concern is evidence to its ability to providing an alternative to electroplating.
Q. I AM DOING MECHANICAL GALVANISING. A FEW OF THE WASHER PARTS GET ZINC FREE AT THE EDGE. LOWERING THE SPEED OF THE BARREL DID NOT AFFECT MUCH. HOW TO SOLVE THE PROBLEM? WILL THE COPPER UNDERCOAT PROTECT THE BASE METAL FROM RUSTING?
IN GENERAL, HOW MANY SALT SPRAY HOURS IS POSSIBLE FOR MECHANICALLY GALVANISED PARTS OF 60 MICRON THICK DEPOSIT COMPARED TO SAME THICKNESS OF HOT DIP GALVANISED COATING? IS MECHANICAL GALVANISING IS INFERIOR TO HOT DIP GALVANISING IN OUTDOOR EXPOSURE?
DR. D. SENFebruary 6, 2010
A. Hi Dr. Sen. I can only address your second paragraph...
Salt spray testing is a poor way to evaluate the real life of any finish, but is notoriously bad with regard to thick zinc coatings which slowly acquire a glassy, adherent, inert zinc carbonate coating after months or years of exposure ... whereas salt spray testing just quickly dissolves the zinc coating, which is deliberately anodically active, long before those carbonate reaction products can form. Mechanical galvanizing and hot-dip galvanizing are equivalent for equivalent thicknesses. 60 microns is 4-7 times as thick as the 8-13 micron electroplated coatings routinely specified for automotive hardware, and should deliver excellent corrosion resistance.
Regards,
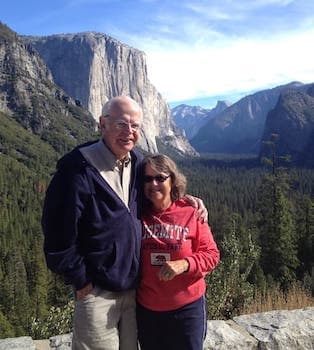
Ted Mooney, P.E. RET
Striving to live Aloha
finishing.com - Pine Beach, New Jersey

Q, A, or Comment on THIS thread -or- Start a NEW Thread