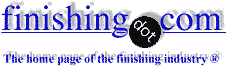
-----
Units of measurement of surface texture
Q. Can anyone help with the units of measurement of surface texture. These are often quoted in microinch or micrometer with the symbol Ra (subscript a), and at other times as RMS.
I would like to know what conversion factor is used to convert between Ra and RMS.
Thanks
- Malta
1996
A. RMS means "root mean square" and Ra "mean roughness".
You could search the definitions in ASTM Standards (for example). Unfortunately I don't know how send math formulae with this form.
- Argentina
1996
A. Sandro:
I have seen a 15 page brochure from Rank Taylor Hobson (surface texture equipment maker) that contains the definitions and formulas for a various "surface texture parameters" (this is the title as well).
Ford Motor Company
1996
Q. We recently had a lab test done on our mirror polished stainless. This time 0.774-0.997 microinch.
The lab was not able to give us the RMS and Ra value. If anyone can please reply. Thanks.
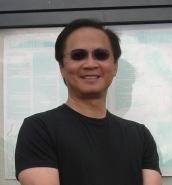
Michael Liu Taylor
specialty stainless steel distributor - Dallas, Texas
1996
1996
Q. The following formulas for RMS, AA were given to us
from the lab that perform the surface roughness tests.
The Ra estimation was from an electropolisher's brochure.
Where: h(n) = heights of surface
N = number of height readings
RMS (root mean square is derived as follows:
RMS average = the square root of:
h(1)**2+h(2)**2+h(3)**2+...h(n)**2
-----------------------------------------
N
AA Average = h(1) + h(2) + H(3) + … h(n)
------------------------------
N
Ra reading is approximately 87.5 percent of Rq or RMS reading.
The AA and RMS formulas are from an article on surface roughness by Lee Dillinger, Metallographic Manager.
LECO Corp. 3000 Lakeview Ave., St. Joseph, Michigan
49085.
This is the best I gotten so far, anyone else with different formula?
It could be soooo simple if only the ISO committee adapts a surface roughness standard.
Mike
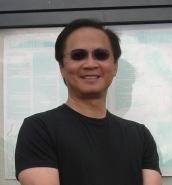
Michael Liu Taylor
specialty stainless steel distributor - Dallas, Texas
A. You can find all about roughness and its measurements in ASME B46.1 standard.
Miguel Flesia- Argentina
1996
Q. I got example regarding hydraulic cylinders, the roughness of cylinder tube I.D. was 12-30 RMS preferred, however,
If Ra reading is approximately 87.5 percent of Rq or RMS reading, it should be Ra 10.5 - 26.25, the value seems too high....
trading - Taiwan
2000
A. I have found a web page that may be of use: www.predev.com/smg/parameters.htm
David Lansdowne- Penryn, Cornwall, UK
2001
2002
1 RMS = 10/11 X 25.4 X 10-3=.023 RA
NOTE 10-3, MEANS 10 THE POWER OF MINUS THREE
1 RMS=MICRO INCH
--------
1 AA = 1 MICROINCH RA = 25.4 X 10-3 MICROMETER RA = .025 MICROMETER RA
NOTE 10-3, MEANS 10 THE POWER OF MINUS THREE
---------
1 S (RMAX = 1 Z )RZ) = 10 AA
- FREMONT, California
I found a technical paper posted at www.bandgmachine.com/technical/feb95.htm that says if there is no other means to to translate then an approximation can be made by multiplying Ra by 1.11 = Approximate RMS value. Nice and quick for on the shop floor conversions. (Ra is approx. 90% of RMS.)
Richard Zinger- Lansing, Michigan
2003
There are approximations 1.11, but they are not accurate. There is no direct way of doing a conversion. The problem is that the Ra (AA) * 1.11 = Rq (RaRMS) conversion only works on a test patch, or some other surface that is a true sign wave. The farther you are from a sign wave, the more distant the Ra/Rq values will be. On average machined surfaces Ra and Rq will be 20%-200% Different.
If you want a true Rq (RMS) value you have to have something that can measure it.
- Mequon, Wisconsin
2005
Q, A, or Comment on THIS thread -or- Start a NEW Thread