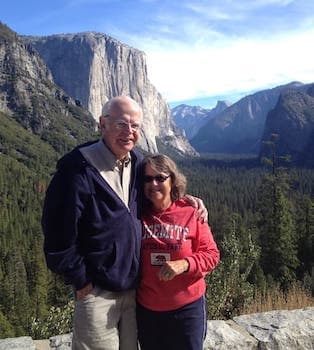
Curated with aloha by
Ted Mooney, P.E. RET
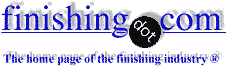
The authoritative public forum
for Metal Finishing 1989-2025
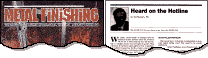
-----
Cannot achieve acceptable corrosion resistance with Electroless Nickel
Q. We have been Electroless nickel plating rolled steel blocks, 250 mm X 110 mm X 25 mm thick, with a high phosphorus bath to a thickness of 12 microns. We have found that they only do form 1 to 30 hours ASTM B117 standard salt spray corrosion tests. Some samples were plated to 25 microns, but performed no better. Electron scanning microscope tests show porosity. We have plated exactly according to supplier's parameters. Tests on rolled sheet metal show similar failed corrosion tests.
Pretreatment is:
1) Hot alkali soak clean
2) Water rinse X 2
3) Half minute in cold Hydrochloric acid 15% 4) Water rinse X 2
5) Hot alkali rinse
6) Hot alkali electroclean 2 minutes
7) Water rinse X 2
8) 12% propriety acid dip 1 minute
9) Water Rinse X 3
10) ELECTROLESS NICKEL PLATE
11) Water Rinse
12) Dry
Variations of pretreatment eliminating the HCl acid, and even only solvent cleaning in the lab also give failed results. Suppliers claim
1000+ hours for 1 mil and 500+ hours for 0.5 mil.
WHY CAN'T WE ACHIEVE NEAR THIS CORROSION PROTECTION?
Yours Faithfully
- Zaire
1996
A. Manny,
Sounds like the porosity may be due to entrapped gas (H2) as opposed to inadequate cleaning. You said you varied the cleaning cycle, in doing this did you try eliminating the electrocleaning? One suggestion would be to try slowing down the plating rate ( lower temp. or lower concentrations sodium hypophosphite and Ni.) Are you sure that the salt spray testing is being done properly -- are appropriate controls run when your material is tested, and do they pass? Good luck
- Putnam, Connecticut
Manny,
I would suggest that surface finish is the problem here. Past experience has shown us any porosity in the base metal or roughness, such as slivers of metal or rough machined areas will show corrosion with a deposit of 12 microns EN. We have used vibratory finishing, mechanical deburring on sharp edges and/or glass bead blasting in our operation to help solve this problem and have had some success.
One suggestion for pretreatment which has helped us: after your final rinse, before plating, go back to the electroclean for 1 minute anodic, rinse, then plate. In some cases we do not use any acid pretreatment steps.
Phil
- Louisiana.
A. If parts are heat treated for hardening it destroys deposits ability to withstand salt spray test and causes high phosphorous containing EN to act as 7-9% phosphorous.
25 microns is a minimum requirement, 35-40 will give better results.
The famous 1000 hours in salt spray is true only for simple sheets, parts with complicated shapes do not resist SST.


Sara Michaeli
Tel-Aviv-Yafo, Israel
A. What temperature is your Electroless Bath? The higher the temperature the quicker the reaction initiates. We have never been able to reproduce the manufacturers claims either. To such an extent that we now make our own electroless nickel chemistry. It is probably not any better but it is much cheaper.
PATRICK CROWLEY-U.K.
1996
Q, A, or Comment on THIS thread -or- Start a NEW Thread