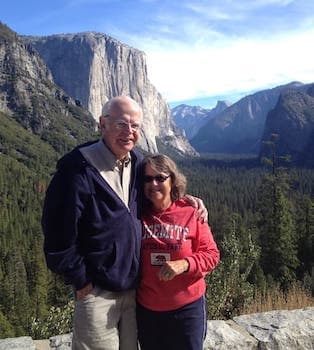
Curated with aloha by
Ted Mooney, P.E. RET
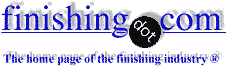
The authoritative public forum
for Metal Finishing 1989-2025
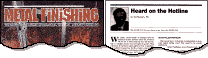
-----
Hard Anodising of high silicon content aluminum alloys
1996
I need to put a thick oxide layer ( more than 30 microns ) when hard anodising high silicon content ( over 10%) aluminum alloys .
These alloys are used by the foundries . Typically in the US it would be a 390 alloy .
Has anybody an idea of how to do that ?
All the tests we have done so far have resulted in an oxide layer thickness under 10 microns .
Thanks for your input .
The devil is in the details, Eric, but in general the way you get thick hard coatings, is to keep the temperature way down (25-32 °F. / -4 to 0 °F.), and apply high voltages (50 or more volts is not uncommon). But that is a great deal of silicon and certainly sounds like a problem :-(
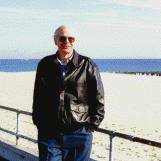
Ted Mooney, P.E.
Striving to live Aloha
finishing.com - Pine Beach, New Jersey
You need a specialty chemistry hardcoat system for high copper alloys
David A. Kraft- Long Island City, New York
1996
Q, A, or Comment on THIS thread -or- Start a NEW Thread