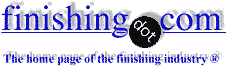
-----
Rusting of stainless steel at weld
Q. We recently had a U.S. manufacturer fabricate bicycle parking modules from 304 stainless steel for a prestigious client in Canada. They immediately experienced spot rusting after the first light rain. The modules were then carefully cleaned of rust and waxed, but rusted again after the next rain. Most of the rusting occurred in areas of weld or areas which were subjected to sanding during fabrication. We have since learned that abrasives should never be used on stainless steel let alone abrasives which have been previously used on ferrous metals.
What is the best way to remove the rust, leave a bright finish and prevent future tarnishing? The largest component is a base plate 8.2 feet long by 1 foot wide. Are electropolishing or passivating options? Are there better finishing options? Who might provide the needed finishing service in the vicinity of Ottawa, Ontario?
Sincerely,
A. Abrasives are commonly used on stainless steel, even for mirror polishing. But I believe that you are correct that abrasives which have been used on steel should never be used on stainless later, for the reason implied in your letter.
Electropolishing is more effective as a passivating mechanism than is nitric acid passivation. However, it is expensive, would probably be overkill, and would also introduce some new variables that would have to be tamed--probably not what you're looking for right now!
Although I've never personally been involved in trying to salvage parts of this nature by passivating them, my feeling is that nitric acid passivation will prove reasonably economical, very practical, and that it will probably work.
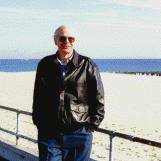
Ted Mooney, P.E.
Striving to live Aloha
finishing.com - Pine Beach, New Jersey
1996
1997
A. I just read your account, in Metal Finishing, of corrosion that occurred on the 304 stainless steel bicycle modules. I am not surprised. What you are experiencing is a phenomena called decarburization. This occurs in stainless steels when they are welded. As the steel cools from the welding process the carbon within the steel combines with the chromium to form chromium carbides within the heat effected zone of the welds. What this does is to effectively remove the chromium from the stainless steel and its resultant corrosion protection abilities. In effect the heat effected zones of the welds are no longer stainless steel and no amount of passivation or electropolish will restore it. To avoid this, we use the more expensive varieties of stainless steel such as 316, 347, or 304L (the L is for low carbon) if welding is to be done.
To save the parts you have already manufactured you will have to modify your joints to protect them, for instance, a selective nickel plate, or perhaps painting the joints. I would do this out to about an inch beyond the weld. As for the abraded areas that are corroding, that is a different situation and passivation will probably work. I would do a local passivation followed by a thorough cleaning. I might also attempt to smooth out the surface, if the abrasion process left any sharp ridges, my experience has been that sharp edges corrode much easier than smooth metal.
materials & processes engineering - aerospace
1996
A. Gerry,
If you cannot find a local plater to nickel the affected areas, you might want to look at brush plating. Mr Collins answer is right on. Also, do not try to make some areas look better by using a SS wheel. They are 410 SS and something happens in the process that no amount of passivation will remove its propensity to rust. I personally had any problem with abrasives on 304, but they were dedicated to 304.
It costs a lot more, but 316L is the way to go. Also look into the amount of heat the welders are using. Are they welding or burning it. Some weld a LOT colder than others with excellent results.
- Navarre, Florida
1997
A. I have to disagree with Mr. Collins assessment of the decrease in corrosion resistance of the weld heat affected zone. Most of the loss in corrosion resistance for weld HAZ is a near surface phenomenon. The heat from welding does cause surface oxidation and results in a very thin layer of chromium depleted material at the surface. This thin layer has lower corrosion resistance. This layer, however, is seldom more than a few hundred Angstroms thick and can easily be removed by chemical passivation. Welding supply companies sell chemical treatments specifically for restoring corrosion resistance around stainless steel welds.
The chromium carbide precipitation phenomenon is limited to the grain boundaries of the material - this phenomenon is called sensitization. The loss of corrosion resistance is specific to the material grain boundaries, and is generally not a problem in atmospheric corrosion. Sensitization is usually a problem in specific corrosive environments and is manifested as grain boundary cracking in the HAZ.
Switching stainless steel alloys will probably not help either if you don't passivate the weld HAZ. Be careful with your abrasive cleaning that you don't don't create crevices by local metal smearing or embed abrasive particles. Crevices can be deadly to corrosion resistance of stainless steel.
I apologize for the long winded response, when I could easily have said that I think a good passivation treatment will solve your problems at the welds and in abrasively cleaned areas. Electropolishing would be nice, but may be overkill. I think that nickel plating is also overkill.
Good Luck.
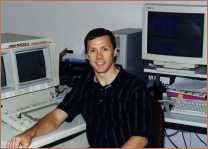
Larry Hanke
Minneapolis, Minnesota
1997
A. I feel Mr. Hanke has his facts correct. Sensitization usually occurs because of an in-service environment and rarely is due to the rapid heating and cooling cycles of the welding operation. I also think passivation is the answer.
Tim
BSWE
- Versailles, Ohio USA
2001
Rust spots after torching stainless steel for cosmetic effect
Q. Hello, and thanks in advance to anyone who has the expertise, time, and occasion to offer guidance. My name is Tim, and my company makes golf putters. The putters are milled from 303SS and one of the finishes we offer is a deep gold color achieved from torching the head with a MAP torch.
Today I was contacted by a customer who told me his putter was beginning to rust in spots. The putter was produced in June, but we have sold a bunch over the last year with this same torched finish.
The following is copied from an answer to a previous question regarding rust due to welding)
"Most of the loss in corrosion resistance for weld HAZ is a near surface phenomenon. The heat from welding does cause surface oxidation and results in a very thin layer of chromium depleted material at the surface. This thin layer has lower corrosion resistance. This layer, however, is seldom more than a few hundred Angstroms thick and can easily be removed by chemical passivation. Welding supply companies sell chemical treatments specifically for restoring corrosion resistance around stainless steel welds."
Is the rusting that my customer is reporting the result of what is being described above, and if so is there something I can add to my process to remove that thin layer while maintaining the color? Also is there a fix that can be recommended and performed on the customer end that will not result in damage of the customer or the product if not executed correctly?
Again, thanks to all who take the time out to reply.
Product Designer - Clifton Park, New York USA
July 31, 2015
A. Tim,
It's usually a good idea to passivate stainless steel after any kind of welding, laser marking, heat treating, or other high temperature events that visibly affect the surface. citric acid passivation generally will not remove the heat discoloration (to the disappointment of most, but fortunate for you). citric acid based passivation/rust removal products are available.
Also, since this is 303, the rust your customers are seeing may be iron oxide, but it alternatively may in fact be sulfur. These free-machining grades should be pretreated in a high pH alkaline cleaner prior to passivation to take care of any sulfur near the surface. That also is not likely to affect the heat discoloration.
adv.
Let us know if we can help.
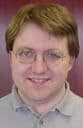
Ray Kremer
Stellar Solutions, Inc.

McHenry, Illinois
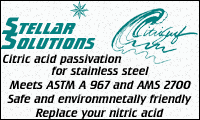
July 31, 2015
Q. Stainless steel SS430 weld area rust. What should I do to prevent this?
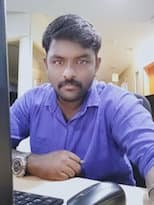
Manikandaprabu janarthanam
Metallurgy - Tamilnadu, India
March 19, 2019
A. Hi Manikandaprabu. Per this thread, the first thing that should be done is passivation. Whether that will be sufficient for your situation isn't known though.
Regards,
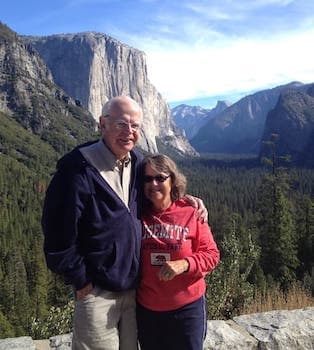
Ted Mooney, P.E. RET
Striving to live Aloha
finishing.com - Pine Beach, New Jersey
March 2019
Q. Actually we are using ferritic stainless steel SS430 for washing machine basket cabinet, we will procure that as Sheet with 2B finish and do spot welding, No post treatments done, but on one lot we have experienced a weld area rust, reports say that the area is chromium depleted, do anyone know why this lot failed and Cr depletion ocurred suddenly not before
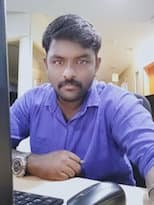
Manikandaprabu janarthanam
- Pondicherry, India
September 3, 2019

this text gets replaced with bannerText
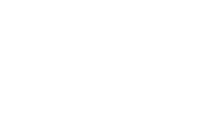
Q, A, or Comment on THIS thread -or- Start a NEW Thread