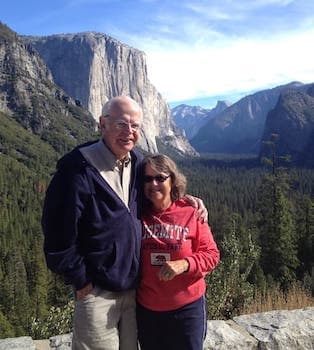
Curated with aloha by
Ted Mooney, P.E. RET
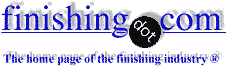
The authoritative public forum
for Metal Finishing 1989-2025
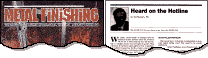
-----
Surface finish and Roller Burnishing
Q. I am a manufacturing engineer who would like to learn more about roller burnishing. I am currently developing a new product which will be manufactured from stainless steel. This new product will require a surface finish of 2-10 micron finish. I am attempting to turn a 16 micron finish on a lathe, and then try to burnish the surface to the final 2-10 micron finish. I have considered grinding and electropolishing.
I would be grateful for any input.
Thanks
Mfg. Engineer
1996
A. A 2-10 micron isn't that unusual; I've recently been looking at some mirror-polished stainless sheet that is 1.17 microinch.
As for electropolishing, whether it is advisable doesn't primarily depend on what surface finish is desired, but on how important cleanliness, elimination of microscopic slivers, and passivation is. An electropolished finish will be very smooth at a microscopic level, but it will be wavy if the substrate has not been well polished.
I'm not truly familiar with roller burnishing, and will leave that to the next reader :-)
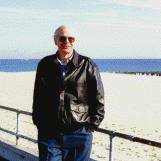
Ted Mooney, P.E.
Striving to live Aloha
finishing.com - Pine Beach, New Jersey
1996
2005
A. Roller Burnishing is a Super-finishing process. It is a Cold Working process which produces a fine surface finish by the planetary rotation of hardened rollers over a bored or turned metal surface. Since all machined surfaces consist of a series of peaks and valleys of irregular height and spacing, the plastic deformation created by roller burnishing is a displacement of the material in the peaks which cold flows under pressure into the valleys. The result is a mirror-like finish with a tough, work hardened, wear and corrosion resistant surface. Lapping and Honing is eliminated.
ADVANTAGES OF ROLLER BURNISHING:
Mirror Finish in One Pass, Accurate Sizing, Close Tolerances, Eliminates Lapping & Honing
Improved Metallurgical Properties - Work Hardened Surface, Increase in fatigue strength,
No Additional Machine Investment - attachable to any Standard Machine Tool Already Present in the Shop
Long Tool Life No Operator Skill Required Low Torque & Power Requirements Maximum Parts Interchangeability
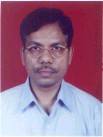
Yashwant Pawar
manufacturer of burnishing tools - Mumbai, Maharashtra, India
A. This method is for to making the workpiece -- which has passed through the pre-machining -- smooth and hard. It is possible to process any kind of metallic material by using this method. The roller burnishing is done by contacting of the rollers on the surface of the workpiece by the help of a precision mechanism. When such a contact is obtained, the workpiece or the tool turns at a specified speed, then the rollers go forward on the workpiece's surface by rotation. In addition, a stress is applied on the surface of the workpiece with a certain force thus the process of roller burnishing is achieved.
Nalan CIFTCI- Turkey
May 26, 2008
Thank you Yashwant; thank you Nalan.
This forum is intended as a technical information source, so we like it best when the thread reads more like a masters' thesis with pros & cons than like a sales shpiel designed to induce people to buy. Every technology has disadvantages & limitations offsetting each of its advantages, so we'd like to ask:
What are those limitations and disadvantages?
What kind of parts will not profit from roller burnishing?
We don't want to rain on anyone's parade, but we don't want a reader to decide to try to roller burnish the wrong item for the wrong application, only to have them later say "Why didn't anyone warn me about that ?!" :-)
Regards,
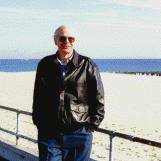
Ted Mooney, P.E.
Striving to live Aloha
finishing.com - Pine Beach, New Jersey
A. Material exceeding 40 rockwell C is too hard for burnishing
Dave Schwister- Milwaukee, Wisconsin USA
July 24, 2009
Ed. note:
This thread was originally laced with recommendations of, and testimonials to, various suppliers of burnishing supplies, equipment, and services. We recognize that readers may wish to contact suppliers for further info, and appreciate the effort of the posters to help the readers that way, but please remember the law of unintended consequences ...
- Most readers are reluctant, for fear of turning the thread sour or even legal action, to challenge another poster; so a thread with company names becomes glowing and one-sided, and loses the technical balance we strive for.
- A sales person who sees his competitor recommended feels compelled to explain at length why his company is better, or even to post with a fictitious name, posing as a satisfied customer :-)
- We already fight off thousands of spams every day and can't open these forum pages to spam.
- The site can't exist without advertisers; and no advertiser will support a forum where parties with possible vested interests pay no part of the costs, then praise his competitors and try to steer the customers to them.
So, we apologize for our limitations, and list without comment the names of suppliers who were suggested if readers are looking for further information:
- Cogsdill [England]
- Metaltec [Korea]
- MechIndia [India]
Q. Hi, I am Shankaremarose here. I wish to do project in burnishing. I would be grateful if somebody answers this. Sir, how to measure the burnishing force? I am using roller type burnishing tool which I have to fabricate. I am mounting the tool in a lathe for cylindrical jobs.. moreover I am using hard material as my work piece. could you suggest to me some tool material? thanks
Shankarstudent - Chennai, Tamil Nadu, India
2006
A. Basically you have to mount a pneumatic cylinder on the saddle in the place of the tool post on your lathe at right angles to the work piece. You need also a pressure regulator a flow control valve, a pressure gauge and a lever operated three way poppet valve.This set up will ensure a constant regulated supply of air at your pneumatic cylinder. The cylinder will actuate the roller holding shaft which is sliding in linear bearings so that there are no friction losses. Just behind the burnishing roller you will place on the shaft your force measuring strain gauges. The signal from the strain gauges is passed to an amplifier and then to a UV recorder. Deflection on the UV recorder show the measuring load at the tool.(You have to calibrate.)
Material for the roller is good at stainless steel . The roller could be radiused or flat. Loads from 400 N - 2.5 kN.
- Athens, Greece
2007
A. You can measure the burnishing force with help of spring of known stiffness and dial gauge. keep the spring inside the tool. and place the dial gauge at the end of the tool shank. the deflection of dial gauge multiplied by stiffness of the spring gives the value of burnishing force.
You can use tungsten carbide or diamond as the tool.
Student - Chennai, Tamil Nadu and India
2007
Burnish rollers with built in force meters are available. Come in pretty handy.
Verl Hayes
- Eupora Mississippi
September 24, 2008
RFQ: From where do we buy these burnishing rollers with built-in force meters as we are doing a project on burnishing? Please reply.
Vikram of Mangalore- mangalore, Karnataka, India
February 28, 2014
Roller burnishing before heat treatment
Q. If you roller burnish a part before heat treatment (tool steels A2 or D2 ) you are in fact compressing the grains together to add some surface hardness -- correct?
Will that improve the grain structure if you heat treat the part after it was burnished?
- wheeling illinois
August 2, 2014
How to choose burnishing roller diameter and speed?
Q. I wish to setup burnishing operation for ID of electric motor stator ID.
What is the correct method of setting of burnishing tool dia?
What is the appropriate speed for burnishing a dia of 107 mm?
- Goa, India
September 3, 2014
Q, A, or Comment on THIS thread -or- Start a NEW Thread