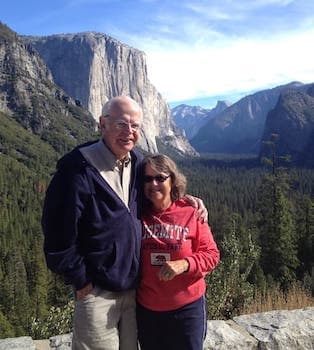
Curated with aloha by
Ted Mooney, P.E. RET
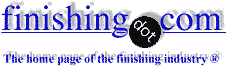
The authoritative public forum
for Metal Finishing 1989-2025
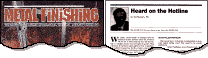
-----
Waste treatment of chromic acid
I was recently involved in the treatment of a batch of Chromium. I work in the Waste Treatment Department of a shop which does electroless plating on plastics.
We had some Chromic Acid, which we use to "rough up" the parts that are plated with Copper and Nickel. We put about 500 gal or so of this Chromic acid in our 3000 gal batch tank. We had around 47,000 ppm Cr in this batch. We ended up having to treat this batch with about 2500 lbs of Sodium Metabisulfite. We worked around the clock for about four days and filled over 50 filter press loads. (Most normal batches that we treat only fill 1- 2 filter presses. ) Is there an easier way of going about this treatment?
Also, in the event of leaks which spill significant amounts of Cr
(5000 ppm) into tanks containing Cu and Ni, is there a good method of Cr removal? We have to add Sodium Metabisulfite, sodium hydrosulfite
⇦ this on
eBay or
Amazon zincaffil links] , and DTC and sometimes still have to run out very slow in order to stay in spec. High levels of Cr get us way behind in the treatment of our other wastes. Do other shops experience these problems?
Thanks in advance to any replies.
1996
I don't know of an easy way to treat chrome. The bisulphite method is probably the least sludge intensive. The problem is that these etches hold a very high concentration of chrome; further, the sludge that they do generate is really gooey glop that is very hard to filter.
The only good side is that it is becoming understood that leaks and unnecessary dumps are not affordable, so that whatever it costs to prevent the leaks and unnecessary dumps looks more attractive every day.
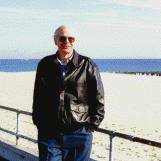
Ted Mooney, P.E.
Striving to live Aloha
finishing.com - Pine Beach, New Jersey
1996
By keeping the pH at 2.3 or below during the reduction process (Cr+6 to Cr+3) will reduce the amount of "sludge".
Chris Willcox- Dayton, Ohio
2005
That's an interesting assertion, Chris. Thanks! Is there a chemical principle that would explain it? I had always believed in keeping the pH in the chrome treatment as high as practical while still getting complete reduction within the available retention time because it minimizes the release of those smelly and toxic sulfides to the air.
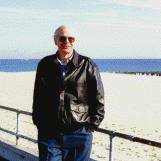
Ted Mooney, P.E.
Striving to live Aloha
finishing.com - Pine Beach, New Jersey
2005
I have worked in both a chrome plating shop and at different WWTP treating CR+6. If the pH value is not below 3.0 during the reduction process it will take a huge amount of sodium bisulfite, therefore creating excess solids. After the pH is lowered and bisulfite is added run a check for CR+6. Add just enough bisulfite until you see the pH start to climb. If CR+6 is still present lower the pH back to 3.0 and add more bisulfite. Repeat process until you have completed the CR+6 to CR+3 reduction. After the reduction you will need to adjust your pH value to meet your permit. Even though the addition of acid will create some solids it will be far less than the bisulfite.
Chris Willcox- Union Grove, Alabama
November 20, 2009
Q, A, or Comment on THIS thread -or- Start a NEW Thread