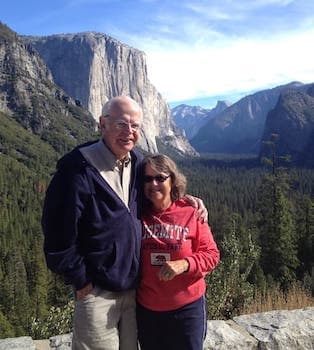
Curated with aloha by
Ted Mooney, P.E. RET
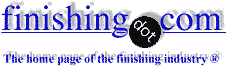
The authoritative public forum
for Metal Finishing 1989-2025
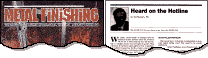
-----
Choosing aluminum casting alloy and finish to resist corrosion
1996
Q. We have an outdoor application for natural colored aluminum castings. The exposure will include all types of industrial and seaside areas. With resistance to corrosion primary, which is the best aluminum casting alloy to use?
Secondly, what, if any, surface finish should we apply to enhance the corrosion resistance?
Thank you for your suggestions in advance.
Treatment &
Finishing of
Aluminium and
Its Alloys"
by Wernick, Pinner
& Sheasby
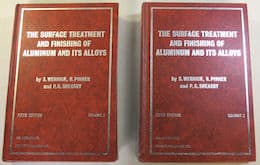
(note: this book is two volumes)
on eBay or
AbeBooks
or Amazon
(affil links)
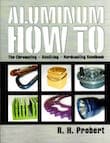
Aluminum How-To
"Chromating - Anodizing - Hardcoating"
by Robert Probert
Also available in Spanish
You'll love this book. Finishing.com has sold almost a thousand copies without a single return request :-)
A. Hi, Ken.
The best surface finish to retain the natural aluminum look and provide good corrosion resistance would probably be sulfuric acid anodizing to a thickness of 18-25 micrometers, followed by a steam or boiling water seal.
In general, the purer the aluminum, the more uniform and attractive the finish will be, and the better its corrosion resistance, so I think you can use that fact in choosing a casting alloy. Good luck.
Good luck.
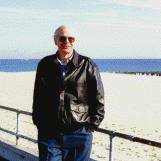
Ted Mooney, P.E.
Striving to live Aloha
finishing.com - Pine Beach, New Jersey
1996
A. We have a good deal of experience anodizing aluminum castings unfortunately we do not always know the final reason for the protective coating. For a corrosive resistance application, we have anodized many castings that are used for an aluminum step application. These steps were for a marine application either for a ladder for a boat or a swimming pool. The cast alloy of choice was Almag-35, an aluminum magnesium alloy that I surmise was chosen for it's ability to resist corrosion. It is a readilyy anodizable alloy and a film thickness of 18 to 25 microns is easily achieved.
Hope this can be of some help
anodizing shop - Philadelphia, Pennsylvania
1996
Protecting aluminum casting from corrosion at Firth of Forth
Q. An uncoated, aluminium diecasting used as the outer case for instrumentation used to monitor the potential of a cathodic protection installation at the end of an oil loading jetty in the Firth of Forth. The aluminium will experience corrosion or not?
william choi- malaysia
2000
A. I think it would depend on what aluminum alloy that the casting is made of, but even if a good one I think I would expect very early corrosion. Consider having it anodized AND painted. Good luck.
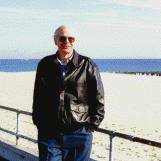
Ted Mooney, P.E.
Striving to live Aloha
finishing.com - Pine Beach, New Jersey
2000
Clear anodize sealant choice for cast aluminum A380.0
December 23, 2015Q. Hello,
My name is Zeb and I am a mechanical engineer at a motor company. I am working on specifying an anodizing process for a part that will be exposed to wear and oil. This part is made out of cast Aluminum A380.0-F, which has a relatively high copper content (3.0 - 4.0 %) and a high silicon content (7.5 - 9.5 %). I need a MIL-A-8625 / MIL-PRF-8625
[⇦ this spec on DLA] Type III, Class 1 coating with a coating thickness of ~.001". I want these parts to have clear anodize and a clear seal (I do not want any coloring from something such as a chromate sealant). This part needs to be RoHS compliant. Resistance to staining is paramount, so I need to have this part sealed, but I also want as good of abrasion and wear resistance as possible (something better than a simple hot deionized water would be preferred.
I am a little stumped on the correct sealant choice but I have narrowed it down to the following:
1. Room temperature Nickel Fluoride followed by a warm water rinse
2. Hot Nickel Acetate
3. Hot Sodium Silicate
I can't seem to find very good information on whether or not Options 1 or 3 will produce a clear product, without discoloring the part more than the anodize process itself. Do you have any suggestions?
Engineer - East Rochester
A. Hi Zeb. You may be more familiar with sealing anodized coatings than I am, but I've never heard of a silicate seal. I thought that was a clearcoat/topcoat, whereas when we speak of "sealing" aluminum we are talking about converting the aluminum oxide to boehmite (simplified explanation) to swell the aluminum and thereby seal the tops of the pores in the anodizing.
Hopefully someone more experienced will be able to answer you rather directly, but until we hear from them or find otherwise, I would be concerned about expecting a clear anodize .001" thick on a high-copper casting. Charcoal gray sounds more likely to me. Good luck.
Regards,
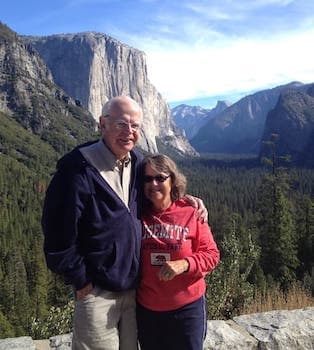
Ted Mooney, P.E. RET
Striving to live Aloha
finishing.com - Pine Beach, New Jersey
December 2015
Diecast aluminium - corrosion and conductive coating recommendation
Q. We have a die-cast ADC12 enclosure that requires to withstand up to 300 hrs SST, preferably be a clear coating and conductive, is there anything you chaps can recommend?
wayne coxon- scunthorpe - UK
October 11, 2018
A. Hi Wayne. I'm not aware of any clear conductive coatings for aluminum diecastings that can withstand 300 hours salt spray, but a class 3 chromate conversion coating per MIL-DTL-5541 [⇦ this spec on DLA] sounds closest to what you are looking for.
If you would please explain the actual application and why a clear coating is preferred/necessary and why a conductive coating is preferred/necessary you may get additional and possibly better suggestions. Good luck.
Regards,
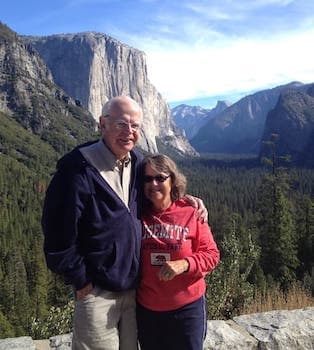
Ted Mooney, P.E. RET
Striving to live Aloha
finishing.com - Pine Beach, New Jersey
October 2018
Q, A, or Comment on THIS thread -or- Start a NEW Thread