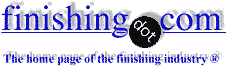
-----
Polishing Stainless Steel
1996Q. Can anyone tell me what chemicals are used in the cloth wadding that is used to polish various metals, especially stainless steel?
At present to get a mirror finish I am using felt wheels and a polishing compound for stainless steel called Hyfin it gives a mirror finish but fills internal holes in the parts with black sludge from the compound and stainless being worn away through the polishing, this is removed in an ultrasonic cleaner using degreasing agent. After cleaning in ultrasonic the surface is a grey color without the mirror shine.
This shine is brought back using wadding (Duraglit) impregnated with some chemical to polish stainless and chrome plating, the whole process takes too long. I can get a good finish using ceramic media in vibratory finishing machine, and get a reasonable polish after, with corn cob, but not as good as using compound and polishing wheel. If I could add the chemical used in the wadding to the corn cob I am sure I could get almost mirror finish.
Leaving the components (batches of around 100 parts) overnight in a vibratory finishing machine is a better proposition that taking all day polishing by hand, about 10 parts per hour.
If anyone has any idea what the chemical used in this wadding is, I would be pleased to hear.
Thanks,
Tattoo Club of Great Britain, U.K.
A. The material used in the felt wheels is not a single material, but a series of grits & compounds, applied in sequential order, to remove scratch lines through ever-finer polishing. Mirror polishing is achieved by starting with a course polishing media, then using a finer one to remove the polishing lines, with the process continuing for 4 or more steps, ending with a very fine buffing compound. The wheels are changed too; fine media isn't put on a wheel formerly carrying course media. Can you barrel/vibratory finish to do most of the work, and then hand buff with the fine polishing compound?
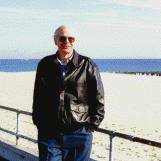
Ted Mooney, P.E.
Striving to live Aloha
finishing.com - Pine Beach, New Jersey
1996
Q. Hand polishing is not a problem, but it is taking too long. The components are small 8 mm diameter tubes ending in a cone shape at the end with small holes in the cone end from 1.5 mm to 2.5 mm. It traps dust from the felt wheels and polishing compound that has to be removed.
The ceramic media is giving a good finish, but not a mirror finish, so the possibility of using chemicals as used in the polishing wadding might be worth trying.
Tattoo Club of Great Britain
1996
A. Hi there, based on my experience, my company used two types of polishing compound to polish our product (stainless steel cookware). one is wadding polishing compound, another one is liquid. And the liquid is more expensive than the others; of course its quality is better than others. best regards
Kenneth Tay- KL, Malaysia
2000
Remove blemishes from stainless steel elevator
Q. We have 12 elevator cabs that have a stainless steel interior finish that is marked and blemished. Does anyone know of a product that would take out these blemishes?
Ted Lowden- Longboat Key, Florida
2001
A. Hi Ted. If the blemishes are superficial, citric acid may remove them.
adv.
You might talk to Stellar Solutions [a finishing.com supporting advertiser] about Citrisurf.
Regards,
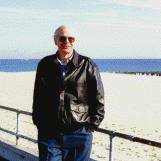
Ted Mooney, P.E.
Striving to live Aloha
finishing.com - Pine Beach, New Jersey
A. I cleaned the external stainless steel shell of commercial toll booths which had been totally neglected for almost two years and which were in filthy condition on commencing cleaning work. I tried a great variety of products and followed lots of varying advice.
The conclusion I reached was that the best cleaning procedure involved
1. De-greasing with a standard de-greaser sprayed on, wiped off and allowed to dry
2. Wadding (e.g Domestic Duraglit etc.) applied in small areas at a time with lots of elbow grease and remove tarnish as you go
3. Final wipe down with a baby oil (e.g. Johnsons Baby Oil). This step was given to me by a house-proud housewife and it really was a useful tip for getting a nice clean tarnish free finish combined with protection going forward
- Dublin, Ireland
June 12, 2009
Alternate methods of stainless steel mirror polishing
Q. At present we are finishing our SS materials with buffing method, that is very labor orientated and time consuming too. For a small batch it requires long time to finish. Now my question is, is there any easy and cheaper process other than buffing which can help us to produce our SS materials with better mirror finishing and will take less time to produce?
We will highly appreciate a quick response.
With Best regards,
bathroom fittings - Dhaka, Bangladesh
2003
A. Nothing can top a hand buff finish in appearance. However, you can drastically reduce your processing time by using mass finishing equipment. Then again, a lot has to do with the surface finish of your parts prior to processing. A rough surface of over 35 RMS may still require a belt or wheel to reduce the surface profile. The next step would be a mass finishing system. The machine size and system depends on the volume of parts needed to be produced in a given period of time. Next, the media depends on the metal being processed. You may need to do more than a one step operation to get a mirror finish, but it still may not match a hand buffed finish. If that is still needed, a very short hand cycle maybe required.
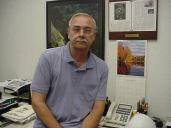
AF Kenton
retired business owner - Hatboro, Pennsylvania
2003
December 27, 2008
A. It sounds like you are buffing before the surface has been brought to the proper finish.
Remember that each step to a finer grit should only happen after the current grit has removed all scratches left by the proceeding process. Moving prematurely will result in both taking a long time to polish, and reducing the quality of the finish.
Any time a step takes too long, it is probably because you didn't take long enough on the previous step(s.)
Check your surface under a 10-20x magnifier and choose the grit which is sized one size smaller than the largest scratches you see.
Any time it seems to take too long, try stepping back one or two levels of grit.
There really is no way to get a better surface finish I know of, chemical polishing methods depend upon the mechanical surface to be smooth first.
- Menomonie, Wisconsin
A. My advice would to polish the surface to as near a finish to mirror as you can then have the part electropolished which is the opposite of electroplating but instead of putting a coating on the surface as in plating it is carried out on a reverse polarity which removes the top surface of the metal.
The only problem is it will not remove scratches, it will take out the surface inside the scratch so the scratch remains.
Hope this helps
Colin
- Milton Keynes, U.K.
July 2, 2010
Polishing stainless steel mirrors
2004Dear Sir,
I am trying to develop SS mirrors for research application. The SS we are trying is 304 grade. Does the grade make sense in achieving Pure Accurate Flat mirrors?
Today I tested the SS Mirror (which I am working with!), in Fizeau tester, and it gives widened fringes similar in the case of glass optics., but still we cannot get pure reflectance., i.e., some blurriness is occurring, maybe because of the polishing agent (cerium oxide) we used. Is there alternate we can try in obtaining a scratch-proof flat SS mirror?
Also the tool we are using is same for the Optics, i.e., a Pitch lap., Does it make sense?
Please reply,
Thanks in advance,
Regards,
Research Based Industry - Kochi, Kerala, India
Mirror polishing small stainless steel bars
Q. I want to mirror polish a standard stainless steel bar of 1" diameter and 3.5" in length. Would a vibratory tumbler be the best way, or a buffing pad, or what? Any help will be appreciated.
Steve Loarhobbyist - Westerville, Ohio
2004
Q. I'm looking for a liquid polishing compound/solution to use on the metal edges of my racing skis. I want to polish them to a mirror finish after I sharpen and de-burr them.
The liquid needs to be non-oil or petroleum based.
I would be grateful for suggestions.
- Winnipeg, Manitoba, Canada
January 4, 2010
A. Reading between the lines of several entries here, there might be a misunderstanding about what those polishing compounds are and do.
They're not acids that melt the metal and let it flow to smoothness. Rather, they are like exceptionally fine-grained sandpaper.
As an aside, although people use power shovels to dig out the earth for the foundations of buildings, if you had eternity you could do it with a teaspoon. Similarly, you can remove deep scratches with a very fine mirror polishing compound . . . but it would take virtually forever.
Practically, the only way to mirror polish metal is in a series of steps. First you use a compound that is course enough to remove every scratch in a practical amount of time, but fine enough that the scratches it creates in the process are smaller than the scratches you started with. Then you use a finer compound, but one that is still course enough to remove the scratches from the first compound in a practical amount of time. Then you use a finer compound ... In other words, mirror polishing is simply a great deal of work :-(
Good luck.
Regards,
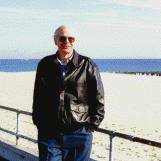
Ted Mooney, P.E.
Striving to live Aloha
finishing.com - Pine Beach, New Jersey
January 4, 2010
Q. I use products of Metabo and 3M. I don't know how to polish metal #2 to #8 (pipe, tube, flat surface). Please help me (step by step). Thanks.
Viet Nguyensales engineer - Ho chi minh, Viet nam
August 10, 2011
Hi Viet. We have many other threads about polishing stainless steel on this site. Just put "polish stainless steel" into the search engine.
However, since you are dealing with different kinds of shapes and metals, you might benefit from the more tutorial approach of a general book about polishing. Thrashing from one thread to another can be a very hard way to learn the basics :-)
Luck and Regards,
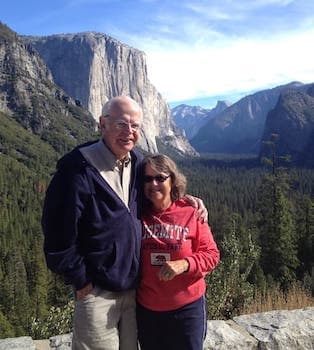
Ted Mooney, P.E. RET
Striving to live Aloha
finishing.com - Pine Beach, New Jersey
January 2015
Can we mirror polish type 430 stainless with same machine and compounds as type 304?
January 18, 2015Q. We are polishing stainless steel BA 304 sheets with woolen buff rotating on the sheet.
Dimensions of sheets are 100 x 200 cm or 122 x 244 cm.
our machine has 8 polishing heads and a liquid which is a mixture of below items is applied during polishing process:
a- 500 liters water
b- 20 liters nitric Acid (HNO3)
c- 25 KG titanium dioxide
⇦ on
eBay or
Amazon [affil links]
powder
The result of polishing 304 is very good. But I am looking to mirror polish SS BA 430. Can I use the same process or do I have to change process and polishing mixture?
worker - UAE
A. Unless someone is working with the same process, it is difficult to say yes to your question. Suggest you try it and then if it doesn't work, re-post your question explaining the new problem. You are basically working with the same materials and process and that normally should achieve the results you are looking for.
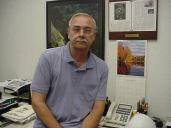
AF Kenton
retired business owner - Hatboro, Pennsylvania
February 5, 2015
Q. Hi,
I would like to know whether we can use Thinners while polishing SS 304 & 316 Grades. I came to know from one Steel expert that using thinner will lead to chemical reaction which may cause rust/staining in future.
Please advise what will be the result if thinner is used to remove stains which persists even after polishing.
Thanking You in Advance,
QA/QC Engineer - Abu Dhabi, UAE
May 26, 2015
A. I assume when you are talking thinners, you are talking about a solvent based product. If that is true, it is not a good choice. There are way too many problems with that. You might want to try a paraffin based product, but I'm not sure that would work any better.
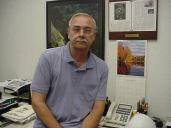
AF Kenton
retired business owner - Hatboro, Pennsylvania
June 3, 2015
A. It would be better if you could share more on the end application of the product. It may be harmful if you [use] thinner/solvent as lubrication media while buffing. I would suggest electropolishing as this would be easier and faster. Good luck.
Mahendra gargatti- Belgaum Karnataka India
June 29, 2015
Polishing Stainless steel fittings & tubes
Q. Best Polishing method for Stainless steel fittings & tubes for Sanitary application of food and pharma industries from 3mm ID till 100 mm (6 mtr length for tubes and various size for fitting)?
We are manufacture of sanitary tubes in India for FOOD and Pharma Industry, under a Brand name. We are successful in making high standard quality tubes with required Ra finish less then 0.38 ra inside the tubes, with use of mechanical polish followed by In house Electro polishing from 25.4 till 101.6 OD tubes, but our automatic mechanical polishing setup doesn't work below 25.4 mm size.
We want to know from you industrial expert what is the best method for polishing tube below 25.4 till 3 mm ID tube in 6 mtr length and also for the fitting we don't want to use conventional polishing with mob wheel as it is very time consuming and labors process. We have done our primary research where we found 2 method which are like a) chemical dipping, b) polishing with ss balls and chemical in vibrating machine.
We are currently doing nearly about 200 tubes in single shift in 6 mtr length, and we for smaller size we want similar capacity and for fitting we need 1000 pcs per day capacity with minimal manpower.
Jignesh shah- Mumbai, India
November 14, 2015
A. You could try extrude honing .
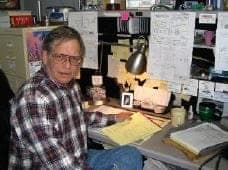
Jeffrey Holmes, CEF
Spartanburg, South Carolina
November 15, 2015
adv.
Jignesh,
Contact me directly about the method of electropolishing internal diameter of long tubes for pharmaceutical and food industries. We have developed a device and method that works together with Universal Electrolyte for various types of stainless steel ID and OD electropolishing. This method was successfully implemented at BAMA facilities in Italy.
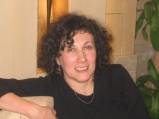
Anna Berkovich
Russamer Lab

Pittsburgh, Pennsylvania
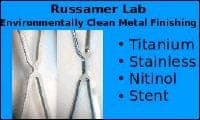
November 16, 2015
Polishing a Scratched Heirloom Cake Server
February 18, 2016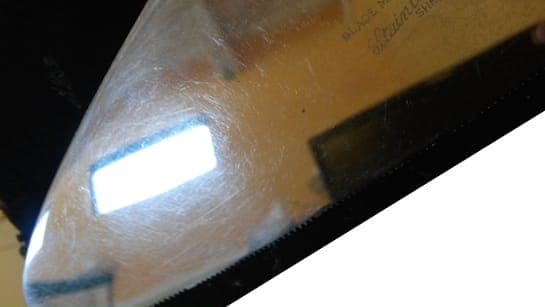
Q. Hi there, I am a bride getting married in 30 days and my mother gave me her cake server from when her and my father (who passed away last year) were married in 1960.
I plan on using it to cut my own cake, engraving the blade with my parents and our names on it to continue to pass down to my own daughter when she gets married.
However, although it gleams so bright, it shows my reflection- it is covered with scratches. I have tried to include a picture, but it is hard to capture the scratches.
Can these scratches be removed affordably and, if so, can I do it myself or would I have to take it somewhere. Also would I remove them before engraving or after?
BRIDE - PUNTA GORDA, Florida USA
A. Best wishes Bridget. Your picture is cut off so we can't fully read the label, but it looks like the cake server is made of stainless steel. This means it is the same material through and through, not just plated, so you should be able to mechanically polish/buff it before you engrave it.
It is something you theoretically could do, but experience is the best teacher, so you would want to practice on scrap, and you're getting married in 30 days and will surely be very busy. Unfortunately I don't know who in your area can do such work but if you have a motorcycle enthusiast in your extended family, they may know. If not, a local antique shop may have contacts.
Regards,
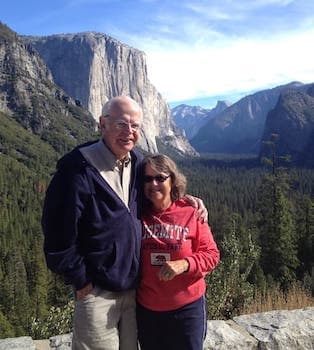
Ted Mooney, P.E. RET
Striving to live Aloha
finishing.com - Pine Beach, New Jersey
February 2016
A. I am an expert on hand polishing stainless still, so let me give you some guidance.
Polishing metal is a lot like polishing automotive clear coats, depending on the damage you start with different size wet sanding paper. In your case I would start with 1000 grit wet sanding paper with soapy water do it for about 5 minutes, then move to 1500, then 2000, after that fine polishing compound and you will have a very nice almost mirror like surface.
- Managua, Nicaragua.
February 18, 2016
A. First, she obviously doesn't have the time to do this by hand herself. Second, from the photo she supplied, the surface is already obviously well beyond 2000 or even 3000 grit wet sanding and polishing.
Wouldn't she be better off, if she REALLY feels the need to do this, to take it to a professional refinisher. What you're telling her to do will result in a finish far below what she obviously has now.
- Pittsburgh, Pennsylvania USA
June 15, 2016
Q. 430 ss 16GA
Had material show up that has a brown tint.
Solvents and cleaners are not helping.
Does anyone have polishing ideas?
This is new material from coil.
- Winterset Iowa USA
October 3, 2019
A. Hi Randy. You tried solvents and cleaners, but did you try citric acid passivating solutions?
Regards,
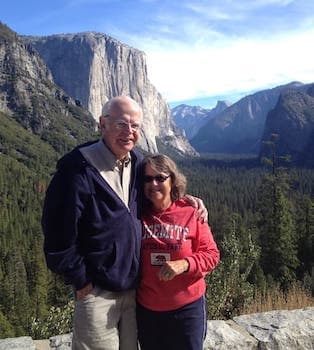
Ted Mooney, P.E. RET
Striving to live Aloha
finishing.com - Pine Beach, New Jersey
October 2019
A. Randy,
A "brown tint" could be a lot of things, though two main possibilities come to mind.
Discoloration from the heat treatment or welding? It needs descaling, either mechanical (grinding/polishing) or acid (pickling).
Iron oxide corrosion? Rust removal and passivation, plenty of available products for that.
Solvent cleaners, detergent cleaners, and alkaline cleaners aren't likely to do anything for either issue.
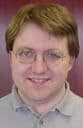
Ray Kremer
Stellar Solutions, Inc.

McHenry, Illinois
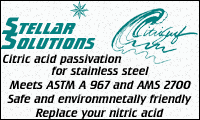
October 15, 2019
Q, A, or Comment on THIS thread -or- Start a NEW Thread