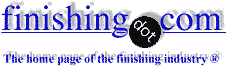
-----
Heating plating process solutions -- steam vs. hot water, internal coils vs. external heat exchangers
Q. I sell industrial water treatment for boilers and cooling systems in industrial facilities. . . What can you or someone else tell me about how solution tanks are heated other than with steam? I have treated the water for these boiler systems for the past 15 years and am very familiar with the constant contamination of the condensate return due to the leakage of the heating element in the solution baths. There is a company here in my hometown that makes a hot oil heater 450 °F similar looking to Cleaver-Brooks boiler that is used primarily in the asphalt industry. They have a few of their small units around town and are working great compared to steam. Any direction or help appreciated.
Tom Houser1996
A. Hi Tom. The four methods of heating solution tanks that I knew of are:
- electric immersion heaters (nice, but expensive to operate on large tanks);
- gas heat (sometimes awkward, and always a bit scary);
- steam (which you are already familiar with);
- hot water (a cost-effective alternative to steam except where high operating temperatures are needed).
But I don't understand why you are getting solution in the coils so frequently. Are they well maintained? Are you sure they are equipped with functioning vacuum breakers to discourage sucking in process solutions during cool down?
Regards,
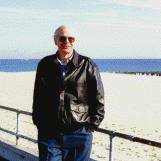
Ted Mooney, P.E.
Striving to live Aloha
finishing.com - Pine Beach, New Jersey
A. Yes most steam return systems are poorly maintained. Many times in a year plating solution enters the condensate return system and disrupts the water chemistry in the boiler{s}. Alkaline solutions are okay since the water chemistry is alkaline, acid leaks cause much problems. Hot oil systems have many advantages over direct gas, electric, and steam. As you said, direct gas can be dangerous, electric $ out of site, and steam (the most common) requires many man hours and many $. Hot water boilers usually operate up to 190° F. This will work in small tanks but would take much time to heat large tanks. Hot oil operates at normal 450° F with temps available up to 600° F.
Hot oil systems are not regulated by any agency and do not have to be insured like a boiler system. They are not required to be inspected annually like steam boilers, saving the plant an average of 2-men 1-8 hr. day to prepare the boiler for inspection by the insurance provider. There are no water treatment costs: no softeners, no chemical treatment tanks, no boiler blowdown. No feedwater/condensate tanks, no condensate return pumps, no steam traps, no vacuum breakers, no licensed operators manning the boiler{s} etc, etc. The average fire-tube boiler operates at 60% efficiency due to scale in the heat transfer surfaces, blowdown, fluctuating firing rates, and changes in steam pressures. Hot oil is controlled by temperature and is 80-85% efficient. Ted, there are many advantages to hot oil vs. steam that I am just finding out over the past 2-weeks investigating this. I am encouraged that you replied back quickly and I hope I hear back from other readers on the forum.
Tom Houser [returning]1996
Hi Tom. I certainly don't share enthusiasm about hot oil systems not being regulated, insured, inspected, or prepared for inspection -- that sounds like a recipe for a disaster :-)
To my knowledge, licensed operators are only required for high pressure boilers (I used to see a few in the plating areas of large captive shops, when captive shops were a thing in the auto industry, but I have never seen a high pressure boiler in a plating jobshop). But your other listed advantages sound promising, thanks.
Industrial hot water is usually more like 210 °F degrees than 190 °F (that's home heating temperature), but your point remains valid that it is hard to heat a really hot tank with water of this temperature. If you have any non-commercial info on these oil units, please send it along. Thanks!
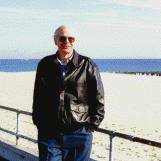
Ted Mooney, P.E.
Striving to live Aloha
finishing.com - Pine Beach, New Jersey
Q. Hello, I am working on a project and one of our clients has the exact problem. Can you provide me with any links or other data about the hot oil alternative? Thanks, Anthony.
Anthony Briganticconsultant - Norfolk, Virginia
July 20, 2010
Q. I am a heating contractor and this is my first look at a hot oil tank in a plating system. To me this looks very unsafe as compared to a hot water heating system. There is no low fluid safety, no secondary hi limit, no flow switch on oil lines? Are these regulated? What safeties are needed?
Andy Lynch- Muskegon, Michigan, USA
November 13, 2012
Multiple threads merged: please forgive chronology errors and repetition 🙂
Q. We are upgrading a metal finishing operation using nitric acid, hydrofluoric acid, sulfuric acid, etc. We are trying to find the best way to heat the tanks (that require heat) using steam. Alternatively we could produce hot water. Is there any trend toward immersion heaters or external heaters in the industry? Immersion heaters have the advantage of steam/hot water leaks go into the tank (rather than into the condensate). However, condensate drainage could be a problem for low pressure steam systems. Please let me know.
Silvan L. Larson- Schaumburg, Illinois
1999
A. Hi Silvan. There isn't a black & white answer, or nobody would ever use the other alternative, of course.
I don't see a really strong trend either towards or away from external exchangers in the last few years. But as an overall thing, taking all real world conditions into account, my own personal opinion is that internal coils are less likely to lead to a pollution incident.
I do not agree that condensate drainage is a crucial issue, unless you have some unusual situation -- tens of thousands of plating lines have successfully employed internal coils on low pressure steam systems for many decades.
As for steam vs. hot water, hot water is simpler and quieter, and the boiler is less expensive, and the coils never draw a vacuum like steam coils can. However, because there is no phase change, the coils must be significantly larger. The difference in coil size may represent only a modest cost if non-exotic materials are used for the coils and the tanks are only modestly hot, but could represent a very big cost if there are numerous coils of exotic materials trying to maintain temperatures approaching boiling.
I think I'm more comfortable with the safety aspects of a leak from a low pressure steam line than from a high pressure hot water line (contemplating it from the comfort of my swivel chair because I haven't actually experienced either). Good luck.
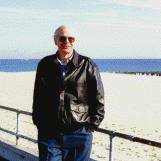
Ted Mooney, P.E.
Striving to live Aloha
finishing.com - Pine Beach, New Jersey
P.S. "No good decision was ever made from a swivel chair" -- Gen. George S. Patton :-)
Forklift operators damage tank heaters
Q. I am a manufacturing manager and we have metal finishing process line in which the tank is 745 gallons, we use a mixture of ammonium bifluoride, nitric acid, and water, this creates a hydrofluoric acid in which large parts are submerged to clean heat scale and shop oils from. Recently I have been without a crane system for placing our baskets in the tank and have used a forklift and a boom system, as careful as my guys are they seem to keep coming into contact with our heating elements when trying to guide the basket into place, this has become costly to keep replacing heaters … is there another method I can use to heat the tank up to 120 °F but no more that 140?
Scott M [last name deleted for privacy by Editor]- Chula Vista, California
July 22, 2017
A. Hi Scott. There are lots of different ways to heat a tank, including through-the-wall electric, steam or hot water heaters which you could install down near the bottom of the tank where nothing could hit them -- although I think these bring far more disadvantage than advantage (such as accidentally draining the entire tank onto the floor).
I'm guessing you know as well as anyone else that a forklift is no substitute for a crane, and that continuing with this approach could lead to a lot of trouble.
Regards,
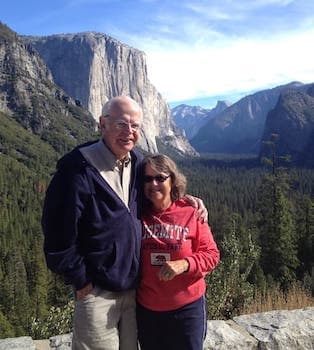
Ted Mooney, P.E. RET
Striving to live Aloha
finishing.com - Pine Beach, New Jersey
July 2017
September 1, 2017
A. I'm a facility engineer and have designed numerous Heating applications and control panels for both heating and rectifiers in the metal plating industry. Observing all the various types of installations (Natural Gas Burners-SS-316, Polypropylene coated immersion heaters-electric) I've made throughout the years I have weighed in the difference.
Gas Burner - Etch, Hot Water Seal, Aluminum Soap 1700 Gal 90 °F. to 164 °F will reach temp in 2-3 hours and requires SCAQMD permit approval and In-network agency provided by SCAQMD to perform NOX, CO2, CO, etc combustion test on all direct fired gas burners. they MUST meet min. requirements required by SCAQMD. SOCAL Gas can perform needed calibration for free and inspection from 3rd party will cost around $2500.
Price- varies on how sophisticated your control panel is and how efficient your burner will be. Compared to electric immersion heater, NG is the winner.
Cons - if safety measures are not taken you risk FIRE and the possibility of your solution evaporating leaving your internal tube burners to heat and crack or warp due to thermal couple failure or just temp control needing calibration, constant maintenance on cleaning diffuser plates, spark Electrode, flame sensors, blower, Stack and possibly control module. All of these factors will depend on the environment in which the burners are in, which in this industry it's going to be very acidic. LOL
Immersion polypropylene heaters - excellent with some harsh solutions, comes in various Voltages and KW ratings per your needs, Will not take much real estate from your tank as a NG burner would. You will need to calculate your KW demand based on some formulas and Delta Temp. Difference between set point and actual temperature.
Price - can be anywhere from $500-12K all depends on KW needed and Voltage, preferably 480 VAC. Electric bill will be expensive if operating below 480 VAC.
Cons - I had many production guys use portable immersion heaters for temporary tanks and would forget to disconnect the power to the heaters and would lead to the poly material melting and causing the burner to short leading to $500 or +$$$ of equipment to become useless. Also if safety measures are not taken such as liquid level sensors, thermocouple, controller calibration, timers, you can melt poly tanks and potentially cause a fire.
Well, hope that helps on deciding between NG or Immersion.
I'm currently designing a water boiler system for a color dye, Type 2, and hot water seal line; once completed I can input my feedback.
Pacific Allied Engineering - Gardena, California USA
September 2017
Thanks Pete. The only thing I would re-emphasize is that some dangers are common & all too real whereas others are very rare, perhaps only potential. For several years I was "the plating shop guy" for a specialty firm which assisted a bunch of insurance companies after fires. Of the many plating shop fires I surveyed around the country, almost all were caused by electric immersion heaters in flammable plastic tanks. Low level protection plus over-temperature protection should not be considered optional but absolutely essential; and electric heaters should never be temporarily used in a plastic tank without both types of safeties operational. Thanks again.
Regards,
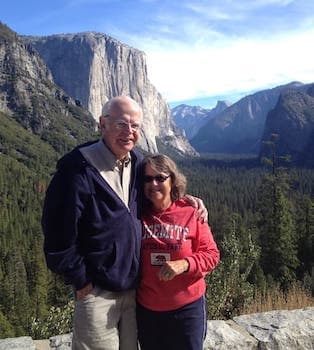
Ted Mooney, P.E. RET
Striving to live Aloha
finishing.com - Pine Beach, New Jersey
Calculate boiler size for heating plating tanks
Q. What size boiler do I need to properly heat 6 plating tanks at 1000 gallons to 140 degrees in a reasonable amount of time.
Alan Mills- Union, New Jersey
May 14, 2018
A. Hi Alan. "A reasonable amount of time" is something you may have to decide before you can go any further, but it's fairly common to size a low pressure steam boiler for a 2-3 hour heat up time. Although you didn't ask, people usually plan on 8-12 hour heat up time if they are using electric heaters.
If you are sizing for a 2-3 hour heat up time, and temperatures that are far from boiling like 140 °F, the overwhelming majority of the steam you input will go towards raising the temperature of the plating solution. So much so, that it is safe to size the boiler for 2-1/2 hour heat up time and be confident that it will achieve it in about 3 hours despite the many other heat losses like evaporation from the tank surface, convection from the tank walls, the heat expended in raising the temperature of the cold work pieces entering the tank to 140 °F, the cold drag-in water from the previous tank. The specific heat of plating solutions is very similar to the specific heat of water, so you can do the sizing based on water.
So, you want to raise 6000 gallons of water, i.e., 49980 lbs., from ambient 70 °F to 140 °F (70 degree difference) in 2 hours. It takes one BTU to raise one pound of water one degree Fahrenheit. So you'll need to add 49980 x 70 BTUs = 3,500,000 BTU in 2-1/2 hours or 1,750,000 BTUs per hour.
A boiler HP is actually 33,469 BTU/hour, but you won't go too far wrong in considering it as 33,000 BTU/hr (which is easier for engineers to remember for several reasons). So 1,400,000 / 33,000 = 42 BHP. This is, of course, quite approximate and there would be nothing wrong with getting by on 40 BHP, or getting a 50 BHP unit.
Regards,
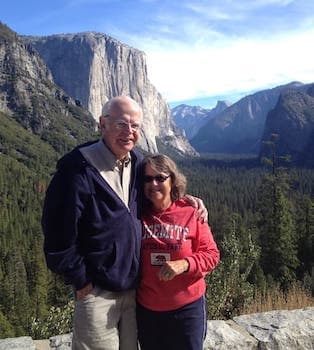
Ted Mooney, P.E. RET
Striving to live Aloha
finishing.com - Pine Beach, New Jersey
May 2018
Q. Hi I am new to the industry and am in the middle of setting up an anodizing plant in Australia. What is the best way to heat up my process tanks such as Hot Etch tank, Degreaser tank, acid etch tank and hot seal tank. I will be using a boiler for heating rather than electric immersion coils. Electricity cost are a major factor in making it a profitable operation
The tanks size are 1500 mm H x 900 mm D x 850 mm W tanks with a fluid volume of 1000 lts . Most temperatures will be 60-70 °C. I am not too familiar with heat exchangers and which ones are most efficient, plate type or shell type. Any help will be much appreciated . Also, what's the best method for cooling the anodizing tank? I have a chiller still debating whether coil or heat exchanger will be best. Any help will be much appreciated. Thank you.
Shop Owner - SMITHFIELD NSW AUSTRALIA
March 1, 2019
A. Hi Robert. After designing a thousand plating & anodizing lines in my career and studying 5X that many, I can still only tell you something that you already know: if one approach were manifestly best, the others would quickly fade out of use :-)
But surely the most common heating method, and a good one, is to use plate-style steam heating coils in the tank. Because of the phase change in steam heating, heat transfer is quite efficient so the coils can be reasonably sized and priced.
When it comes to cooling (with its lack of phase change), and anodizing (with its need for acid-resistant heat transfer surfaces) though, the case for external heat exchangers with their high velocity flows and greater efficiency is more easily made.
Regards,
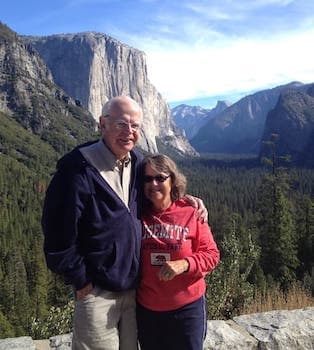
Ted Mooney, P.E. RET
Striving to live Aloha
finishing.com - Pine Beach, New Jersey
March 2019
Q, A, or Comment on THIS thread -or- Start a NEW Thread