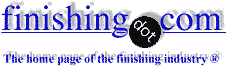
-----
Maintaining low contact resistance on zinc coated chassis
Q. GalXC vs. G90 or Galvannealed long term electrical conductivity for EMI?
We have found over years of radiated emissions (RF) testing that Galvannealed plating oxidizes and develops a non-electrically conductive layer over time. We switched to GalXC, and the propriety plating and have not had the conductivity problems since. Now, we can't get GalXC. Wondering if there is something else similar we could use. Also wondering about pure Zinc, like G90 and how it would oxidize. Does it develop the grey powdery finish similar to Galvannealed?
BRENT GALAS- DENVER Colorado
June 11, 2021
Different coating weights - i.e., G30, G60, G90, etc, won't make any difference because the surfaces will be the same. The difference between ordinary galvanizing and GalXC is that the GalXC has a passivation applied to the surface to prevent premature oxidation of the zinc. I would guess that it is a trivalent passivate or a zinc phosphate; a little digging would tell you which. From there, you could find a local metal finisher that could apply the same passivation.
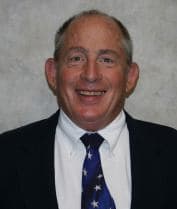
Tom Rochester
CTO - Jackson, Michigan, USA
Plating Systems & Technologies, Inc.

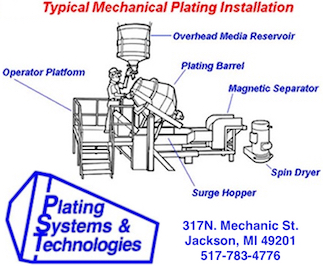
June 15, 2021
⇩ Related postings, oldest first ⇩
Q. I have a question about the use of Zinc plating on a steel chassis. How do you address oxidation of the Zinc plating when low skin resistance is a requirement? I would like to use a tin plated EMI gasket between two pieces of Zinc plated steel panels. What would you suggest to prevent a resistive buildup on the surface of the Zinc plating? Thanks for your time.
Michael KinneyA. I don't know enough about EMI shielding to give a to-the-point answer, but chromates will do a good job of holding down the contact resistance (although they may not be affordable). You should pick a clear/blue one because thicker chromates do cause resistance. Tin is worse than zinc in the short term, but is better at low resistance in the long term. You might need a very specific computerized literature search to find quantitative data unless a reader here can offer you more than I can.
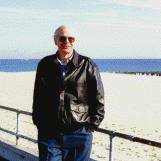
Ted Mooney, P.E.
Striving to live Aloha
finishing.com - Pine Beach, New Jersey
1996
1996
A. My experience is with chassis for electronic equipment. If the equipment is in an office environment the best finish on the zinc would be a clear chromate conversion coating. The thicker coatings, such as the yellow or black coatings are definitely more corrosion resistant, but unless your EMI gasket has points to dig through the coating they may not make a good ground contact even initially. If your gasket does dig through the oxide or you have lots of force and wiping, then they might work. My experience has all been in designs where we didn't have those features.
Janet RiceQ. Would you please recommend the best and cheapest plating for a steel chassis that must be electrically conductive so that it passes ESD testing? The current design that I'm working on is too complicated for powder coating, which is what I normally use.
I've been told that bright tin, annealed plating is not good enough for passivation. Nickel is banned in some countries due to allergens. And clear zinc may reduce electrical conductivity too much.
Nickel-tin alloy plating has been suggested. But I can't find a local supplier that can do it.
If zinc plating is the answer, what specifications can I put on my drawings to ensure that electrical conductivity remains adequate?
Thank you.
Mechanical Designer - Ajax, Ontario, Canada
September 9, 2013
Q, A, or Comment on THIS thread -or- Start a NEW Thread