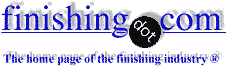
-----
Rectifiers and ripple
Q. I have installed a system in house to electroplate the Jewelry we have manufactured for 30 years. We cast rubber molds using a tin/Lead alloy and a zinc alloy to create lapel pins, key tags, medallions, belt buckles, etc.. We plate utilizing a non cyanide strike, acid copper, nickel, gold, and non cyanide brass solutions. The question has come up about the deleterious effect of ac ripple in plating this type of product. What percentage of ripple is acceptable. I have been told by one source that under 10% is a must and by another source that 46% is acceptable and will have no effect in plating my kind of product. We have rectifiers that meter out to both percentages. Our experience for the last 60 days has been positive, but if it can be better, I would like to know.
Ken Fefferman- Harwood Heights, Illinois
1995
A. Ripple is generally considered problematical for nickel plating due to the possibility of generating a passive surface (with consequent delamination and peeling). To my knowledge (and it's only my understanding) ripple isn't a big problem for the more noble metals like copper and gold. Brass, being an alloy, will deposit more copper at low voltage, and more zinc at higher voltage, so ripple could be at least a theoretical problem. A better way of looking at the question, though, might be to ask yourself whether you picked appropriate rectifiers: single phase vs. three phase; tap switch (or powerstat) vs. SCR; operating near their maximum output (good), or being way oversized (bad). If you selected well in concept, I seriously doubt that you need to add ripple chokes, even to the nickel rectifier; if you selected poorly, you selected poorly even if ripple is not a problem. Give us some more particulars about the rectifiers if you get a chance.
Q, A, or Comment on THIS thread -or- Start a NEW Thread