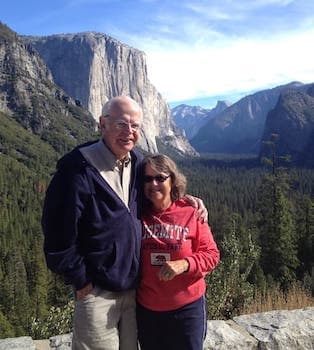
Curated with aloha by
Ted Mooney, P.E. RET
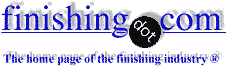
The authoritative public forum
for Metal Finishing 1989-2025
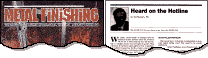
-----
Unplated area inside blind holes is rusting
Quickstart (no readers left behind):
Plating thickness is essentially proportional to the applied current and time (per Faraday's Law). But electricity wants to take the path of least resistance, so edges, corners, and protrusions get thicker plating, while recesses and inside diameters get lesser, sometimes none.
Some plating solutions (usually the more chelated or complexed ones) exhibit better "covering power" or "throwing power" than others. Addition agents (brighteners) can also help with covering and throwing power by being attracted to the high current density areas and somewhat covering/blocking/insulating them to steer the current away so it flows towards other areas.
Holes, especially blind holes not only have coverage issues, they can also be a problem by causing air locks which prevent the process solutions from getting into the hole, or by dragging solutions cupped in the holes to the next tank.
Q. I have a plating problem that concerns a 5/16 cold rolled steel and I have spec'd a finish of zinc plating on. There are a number of blind, tapped holes (8-32) end-on into the 5/16 thickness. The problem is that after the part gets plated, rust appears days later inside the tapped holes. I have talked to my plater about the problem, and he assures me he is following this procedure: 1. ultrasonic cleaning. 2. water rinse. 3. electro cleaning. 4. water rinse. 5. descaler. 6. water rinse. 7. cyanide pretreatment. 8. water rinse. 9. zinc plating. 10. water rinse. 11. chromate 12. four water rinses 13. hot water rinse.
If this is the proper plating procedure, and every thing here looks like the right set of steps, why else might I be getting the rust inside the holes after a few days? Any help would be appreciated.
1995
A. This problem may be more about the plating shop managing your expectations than their technique, Ronny.
In typical commercial zinc plating, rust inside tapped holes like this is a commonplace because there is no plating inside the holes. The plating will deposit in proportion to the current flowing to that area, and essentially no current will flow into the hole. Some platers (with their customer's permission) stopper the holes during processing to minimize dragover and contamination rather than pretend there will be plating there. If the parts were treated with a rust inhibitor at some point prior to plating, plugging the holes would retain the rust inhibitor in them, and might help.
If the inside of the holes MUST be plated, they can be. But this involves detailed handwork like putting a piece of wire (auxiliary anode) into the hole, and inverting the part in every tank so that neither air pockets nor cupped solution interfere with the process. But this is certainly not the usual commercial practice, and would be very expensive. Sorry to be the messenger.
The only cost-effective encouragement I can offer besides plugging the holes is that: 1. alkaline zinc and cyanide zinc plating solutions have greater covering power than acid zinc, and you may see at least some improvement if the plating shop uses one of those processes instead of acid zinc. 2. barrel plating may help a bit if the parts are amenable to barrel processing. Good Luck.
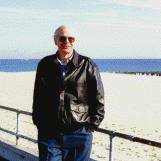
Ted Mooney, P.E.
Striving to live Aloha
finishing.com - Pine Beach, New Jersey
Rust on bend area of zinc plated pipes
Q. We are facing Rust Formation on the Bend Area of Zinc Plated Pipes. We are following both Acid and Non-cyanide Alkaline Zinc Plating process, but facing same problem. Kindly confirm the exact reason and corrective actions.
2nd problem is that when we rub the surface with soft paper board, the Green Passivation Layer (hexavalent) is coming out. What is the reason and corrective actions.
- Jamshedpur, Jharkhand, India
February 9, 2014
by Larry Durney
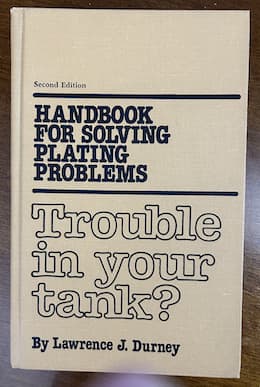
on eBay
(sometimes) or
AbeBooks
(rarely)
or Amazon
(sometimes)
(affil links)
A. Hi cousin Arijit. You probably realize that there are entire books about troubleshooting plating problems, like Durney's "Trouble in Your Tank", and entire books just about zinc plating like Geduld's "Zinc Plating". I mention this so you can have some reasonable expectations about people's ability to help you through this forum, and how much work it is going to necessitate on your end. If you need speedy and closely focused help, you need to call in the suppliers of your plating processes and have experienced eyes look it over, or retain a plating consultant.
But to get started here, please tell us more about these bent pipes, whether the problem is at the inside or outside bend, how you rack them, and what the plating thickness is in the rusty area. Photos of the parts and the racking would help. If the problem occurs after packaging, the packaging material may be an issue too.
Regarding the green chromate rubbing off, please tell us the maximum temperature the parts see at any point after chromating, and whether you are able to prevent any abrasion for a 24-hour curing time. Thanks!
Regards,
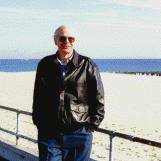
Ted Mooney, P.E.
Striving to live Aloha
finishing.com - Pine Beach, New Jersey
Q. I have attached photographs about the Rust formation on Bend Area (outside).
Plating Thickness is 19-23 micron. It is processed in Rack horizontally. This is Acid Zinc with Olive Green passivation (Cr-6).
- Jamshedpur, Jharkhand, India
February 11, 2014
A. Hi. That is extremely heavy zinc plating -- 7-1/2 to 9 ten thousandths of an inch -- and you should not be encountering problems. How do you know the zinc plating thickness? Are the pipes bent before or after plating (a bender could damage them)? When does the rust develop -- immediately after plating or months later? I find it hard to believe you could encounter such heavy red rust within a reasonable time.
Are the parts stored in a plating shop laden with acid fumes?
Rub-off of the chromate can occur for a number of reasons, but foremost is exceeding a drying temperature of 140 °F. It's hard to trust the color tone of photographs without well-known things like trees, sky, and human skin in them, but the chromate looks black, not olive green. Good luck.
Regards,
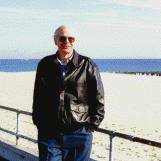
Ted Mooney, P.E.
Striving to live Aloha
finishing.com - Pine Beach, New Jersey
Q. Hi, We have a cylindrical part with a blind hole of 17 mm and we observe heavy rust within the hole even after zinc plating. I know that the plating is not happening within the hole.
Can anyone kindly suggest what can be followed to plate the holes in an economical manner, or to prevent rust?
- Hyderabad, India
October 31, 2014
A. Economical is a matter of need or perception.
Cleaning is mandatory and nearly impossible. This by and large makes tank plating impossible.
A grease like cosmoline is probably the best answer.
If You have to plate it, then a motorized and flow thru brush plating is about the only way that I can think off. The chemicals will mess up the existing plating requiring a difficult masking job. If you brush plate the holes first, then you are going to need an excellent plug for the holes when you clean and activate the rest of the part.
You might be able to sell your customer on using a good anti-seize
⇦ this on
eBay
or
Amazon [affil links] material after plating and after excellent flushing of the hole.
- Navarre, Florida
Limited success zinc plating from vinegar and epsom salt
Q. Hi, I have a similar issue. I am zinc plating some motorcycle pieces and have run into a very interesting dilemma. First and foremost, I am not in the least an expert at electroplating, nor am I a chemist or electrical engineer so I'm at a loss as to why this is happening.
I am using a very basic, household setup consisting of vinegar
⇦in bulk on
eBay
or
Amazon [affil links] , epsom salt, a chunk of zinc (marine outboard anode) and a benchtop power supply set from 1.5 - 5 Volts (experimentation range) at 1 - 4 Amps (also experimentation range) and am getting a good plate for the most part but in a concave area of a footpeg mount or concave head bolt, the plating (zinc) is not sticking.
On the footpeg mounts there is a definite line where the plating stops, and I'll provide an image.
It seems there's some type of electrical field going on because when I submerged the pieces in the vinegar solution a second time using an alligator clip vs a bent hook on a piece of solid core copper wire, the portion of the alligator clip nearest the unplated area didn't even have any plating stuck to it when it otherwise does when plating other parts. Pics to come soon.
for Shops, Specifiers & Engineers
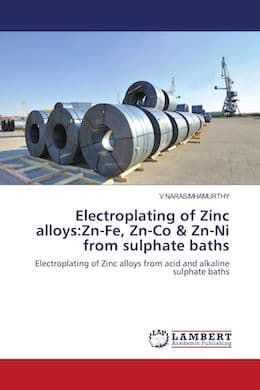
from eBay, AbeBooks, or Amazon
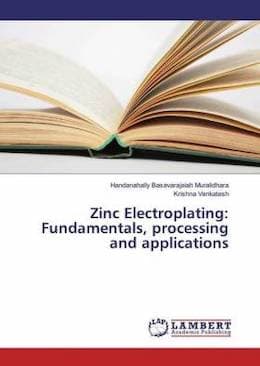
from eBay, AbeBooks, or Amazon
"Alkaline non-cyanide zinc plating with reuse of recovered chemicals" by Jacqueline M. Peden (1994)
from (U.S. EPA)
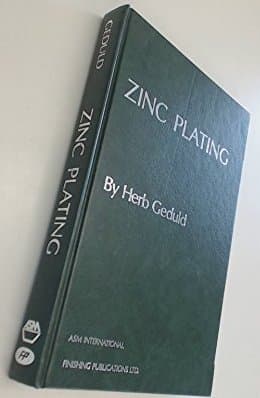
from eBay, AbeBooks, or Amazon
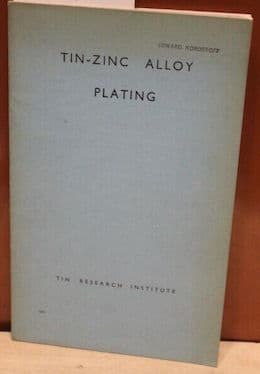
from eBay, or AbeBooks
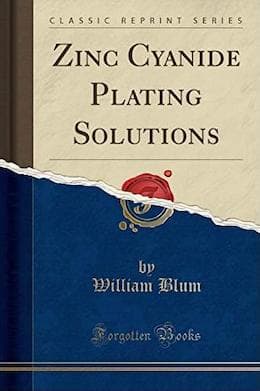
from eBay, AbeBooks, or Amazon
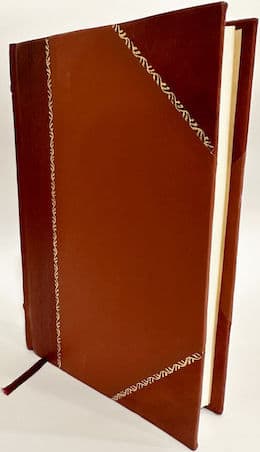
from eBay, AbeBooks, or Amazon
(as an Amazon Associate & eBay Partner, we earn from qualifying purchases)
- Gainesville, Florida, United States
February 13, 2016
A. Hi Stuart. I'm glad you are enjoying at least some small measure of success in plating from the vinegar & epsom salt. My great friend and former partner Tom Pullizzi invented this solution 20 years ago as a safer way for elementary school children to actually see a little something happen as they learned the principles of electroplating. It was never intended to be stable, robust, or usable for actual parts :-)
A concave area will get very little current (most of the current will take the shortest path), and thus little plating unless you can fashion an anode to follow that contour. Still, when plating doesn't stick, it's usually best to assume that the area was not properly cleaned and activated. Good luck!
Regards,
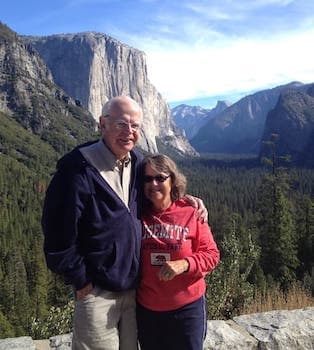
Ted Mooney, P.E. RET
Striving to live Aloha
finishing.com - Pine Beach, New Jersey
Q. Hi Ted, I've actually had great success with this vinegar / epsom salt solution which is actually the standard among other zinc plating recommendations and it works well on the areas that ARE plated (the plating is well adhered) but I'm just having trouble with this particular situation.
I have also tried submerging this part in the solution using various orientations to the anode and have attempted many runs with cleaning in between still to no avail and was wondering if there is an electrical or magnetic field being created in the middle of this part which is preventing the zinc from depositing on this area?
I was wondering if you received the image and additional input I sent you? I'm certain the part is clean and I have connected the cathode lead directly to the non plated area yet the plating doesn't stick in this center area and I'd like others to see the picture and be able to comment. Thanks
- Gainesville, Florida, United States
A. Hi Stuart. No pics received. Please attach them in email to
Yes, I can see from googling that a large number of auto enthusiasts are now using Tom Pullizzi's vinegar & epsom salt solution for plating. It's gratifying, but I wish they'd occasionally attribute it to him 🙂
Regards,
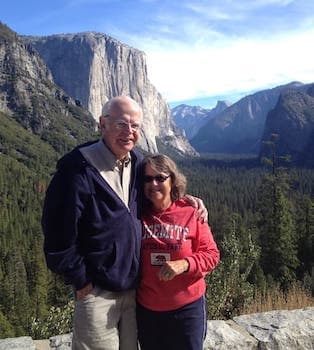
Ted Mooney, P.E. RET
Striving to live Aloha
finishing.com - Pine Beach, New Jersey
A Better Coating for Spring Loaded Auto Clips?
Q. Good Morning:
Just an auto hobbyist looking for a better widget in the resto of a thirty year old car …
Some of you may recall the spring loaded clips of yesteryear used by car manufacturers to attach the top of air cleaner to the bottom of the air box that held the air filer. Both top and bottom used to be metal but then at some point the lower metal bowl gave way to hi-heat plastic. Yet the silly "galvanized" clips (7) remained.
Over time these clips rusted, corroded or generally became less than serviceable.
After sourcing an OEM supplier for the clips I was wondering what kind of coating (process) could be applied to the same in a cost efficient manner that might render the same a metal look but a more dutiable life span?
Any help or suggestions are greatly appreciated.
Hobbyist - Naples, Florida
February 23, 2016
A. Hi Jim. As the owner, over time, of many 10-12 year old cars I wish they'd still use metal:-)
The underhood plastic seems to be fine for about 8 years but finally loses the last of its plasticizers, becoming weak & brittle and unrepairable.
I'm perhaps misunderstanding you, but you want a D-I-Y plating that is more robust than OEM plating? Sorry, that's not going to happen. You can send the clips to a plating shop for zinc alloy plating, or you can try to do the very easy vinegar-based zinc plating described on this letter and in our FAQ. As noted, this process was intended for grade schoolers to play with plating relatively safely, but auto enthusiasts have reported some success with it on actual parts.
Spring clips are hardened steel which is very subject to hydrogen embrittlement, but on the other hand they don't seem to be life-critical parts, so it seems you could try the D-I-Y plating if you wished. Just wear safety glasses when flexing them because without a hydrogen de-embrittlement baking they might be prone to shattering. Good luck.
Regards,
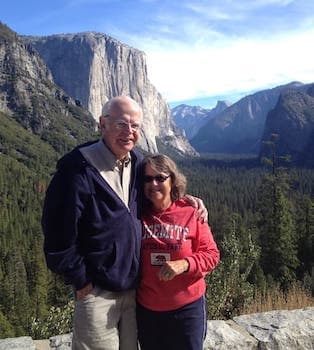
Ted Mooney, P.E. RET
Striving to live Aloha
finishing.com - Pine Beach, New Jersey
Q. Hi,
I have a plating problem in blind hole parts which we are using in the cables (Crimping process) in Door Latch mechanism in cars.
Specification is zinc plating with 8 microns minimum coating thickness.
Plating done in Automated Barrel process (Acid Based)
The problem is that after the part gets plated, rust appears days later inside the blind holes. I have talked to my plater about the problem, and he told plating will not pass in the blind hole and moreover they are followed by water rinse 2 times, Drying temp. 80~ 100 deg.
To avoid Rust and chemical inside the blind hole, Plugging the end cap parts and send for plating . After plating removed the plugs and checking the parts 100% in the plug gauge , and rework done 100% pre drilling done and removed the dust inside the end caps
If this is the proper plating procedure, and everything here looks like the right set of steps, why else might I be getting the rust inside the holes after a few days? Any help would be appreciated.
I need solutions for the below issues
1. To avoid Rust / Dust inside the blind Hole
2. Plating process solutions
Supplier Development Engineer - India , Tamilnadu , Chennai
June 8, 2016
A. Hi Ramnarayanan.
a. Although it can depend on the diameter and depth of the blind holes, it is generally true that you can't expect plating inside them.
b. An alkaline zinc plating process would exhibit somewhat better coverage and leave behind somewhat less corrosive contaminants.
c. Surely the process doesn't end with plating, rinsing, and drying but rather with plating, rinsing, chromating, rinsing, and drying?
d. 80-100 °C drying is too hot, as chromates should only be exposed to about 60 °C.
But it seems that you are now doing nothing at all to the bare steel inside the blind holes and expecting bare unprotected steel not to rust? That doesn't sound to me like a reasonable expectation. I don't fully understand your fabrication sequence, but I think at some point you need to clean those blind holes and apply some sort of preservative. Maybe run them through the electrocleaner, squirt a dap of rust preservative in as you plug the holes, then run them through the whole process beginning with cleaning again?
Regards,
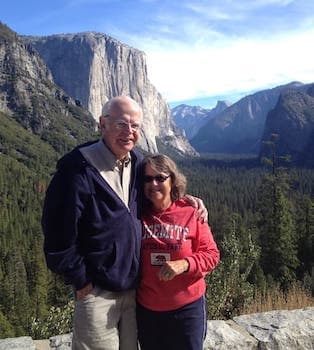
Ted Mooney, P.E. RET
Striving to live Aloha
finishing.com - Pine Beach, New Jersey
A. Perhaps some kind of conforming anode?
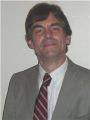
Dave Wichern
Consultant - The Bronx, New York
Q. Hi, I am an Intern working at a company that makes wheel locks and lug nuts. I am working on a project to reduce rust in the blind holes of our parts. The parts are plated with copper nickel and chrome on a rack and have an air pocket when submerged in the plating bath. I have noticed that the rust seems to form along the bath/air pocket barrier. I assume this is due to the acidic nature of the bath and the oxygen at the barrier. However, I notice a large rust formation after sending the parts through an oven for hydrogen de-embrittlement. I am looking into ways of incorporating rust-preventative measures on our plating line. Would it be possible to have a high-pH rinse tank at the end of the plating line without leaving a residue or stains on the parts once baked in the oven?
Thanks,
Kaleb
Process Engineering Intern - Buffalo, New York
July 19, 2021
A. Hi Kaleb. I know of shops who did nickel-chrome plating on tubing and finished the cycle by phosphatizing the I.D. of the tubing. The advantage of that approach was that the phosphate reacts with the bare steel but does not affect the nickel-chrome plated area, so after rinsing there is no residue to cause staining. But they did not have to bake like you do.
Exactly what would happen to the phosphatized area during baking I don't know. Phosphatizing and oiling after the baking sounds more straight forward, but may involve more than your shop wants to deal with. A high-pH rinse may not do as much as you'd like, and sounds like, by definition, it would have to leave an alkali residue on the parts.
An important thing about plating for you to learn as an intern, which you may already know but which your bosses may not have learned, is that you try these chemistry ideas in the lab first. I'm pretty serious! -- you can't imagine how many people write to us saying that they added a thousand pounds of 'x' to their plating tank and it didn't work, or they tried to treat 6,000 gallons of waste by adding 750 gallons of sulfuric acid or sodium hydroxide, so what now :-)
Luck & Regards,
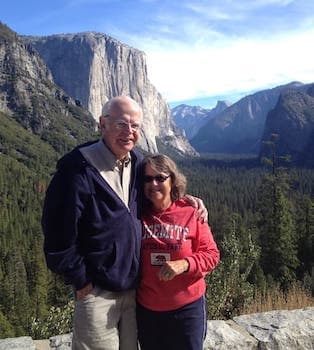
Ted Mooney, P.E. RET
Striving to live Aloha
finishing.com - Pine Beach, New Jersey
A. Kaleb,
Unplated area of parts is rusty because of this area oxidized; if you want to prevent rust, you can do wax of this area or dip this part into rust inhibitor liquid.
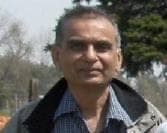
Popatbhai B. Patel
electroplating consultant - Roseville, Michigan
Q, A, or Comment on THIS thread -or- Start a NEW Thread