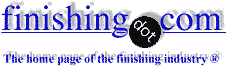
-----
Anodized aluminum refuses to dye

Q. I am trying to establish a facility for color anodizing. My issue is why color is not adhering to the Aluminium pieces after anodization process. White thin layer of Aluminium is clearly evident after sulfuric acid anodization bath. please advise why dyeing process is not getting result? What can be done?
Steps followed
1. Mechanical & cleaning with detergent
2. water rinsing
3. Caustic soda 5% for 25-30 min
4. water rinse
5. Nitric Acid (50%) dipping - 2-3 min
6. Water rinsing
7. sulfuric Acid (20%) dipping - 40 min with Aluminium on both sides as anode and working piece Aluminium at the center connected to rectifier. (voltage of 4-5 volt and up to 12 volt given. Current was varying).
8. water rinse
9. dying - 20-30 min
10 rinsing
11. hot water sealing - 10 min
12. Drying
- UAE dubai
June 19, 2023
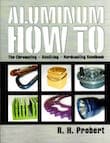
Aluminum How-To
"Chromating - Anodizing - Hardcoating"
by Robert Probert
Also available in Spanish
You'll love this book. Finishing.com has sold almost a thousand copies without a single return request :-)
A. Hi Imthiyas. There are a few questionable things in your process spec, like:
• very long etching time,
• high acid concentration, likely too low voltage, and no mention of temperature in anodizing
• no mention of temperature in dye tank,
• rather low sealing time ...
But I think the obvious first step is to measure the thickness of the anodizing, rather than just trust that the anodizing is okay and the problem is in the dyeing step.
Luck & Regards,
Ted Mooney, P.E. RET
Striving to live Aloha
finishing.com - Pine Beach, New Jersey
Q. Thank you Ted Mooney for your reply. Please find below answers:
• very long etching time: Is 5-10 min adequate in caustic tank instead of 25 min?
• high acid concentration, low voltage, and no mention of temperature in anodizing. Is 20% sulfuric acid conc is more will reduce to 15%. Temperature is room temperature as no cooling system provided. Temp may be around 20-25 °C. If we apply high voltage such as 12V current drops near to Zero very fast. So voltage gradually increased from 3V to 10 Volt.
• no mention of temperature in dye tank,- Temp of approx. 50 °C
• rather low sealing time ... Sealing time will be increased to 30 min.
• what is the min coating thickness required for dye to hold after anodizing, Highly appreciated if you can support with valuable advice in this dilemma. Thank you.
- UAE Dubai
June 20, 2023
by Larry Durney
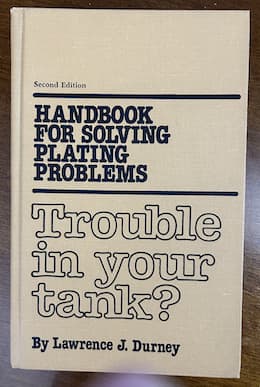
on eBay or Amazon
or AbeBooks
(affil link)
A. Hello again Imthiyas,
There is a difference between designing an anodizing line and troubleshooting a problem. You can't efficiently troubleshoot the problem by simultaneously changing the etching time, the anodizing concentration, the sealing time, the anodizing thickness, etc. :-)
Does someone there have actual anodizing experience, or is it book knowledge? Nothing wrong with book knowledge! -- I only ask because it might be something quite obvious to an anodizer but misunderstood. For example, when you say there is a "white layer ... clearly evident" I'm not confident that what you are seeing is a proper anodized layer.
Please measure the anodizing thickness that you are actually getting. Thanks!
Luck & Regards,
Ted Mooney, P.E. RET
Striving to live Aloha
finishing.com - Pine Beach, New Jersey
A. Hello cousin Chanath,
A caustic etch bath should be considered 4 distinct parts:
Contamination
Temperature
Agitation
Contamination means how much sloughed-off aluminum (and other materials) remains in the tank. This slows the etch. Which is good -- to a point. A stable, low to moderate, level of aluminum in an etch bath is a gift to your line technician :)
Increases in temp, time, and/or agitation speed it up.
Once you've confirmed by titration that your etch has a good level of both hydroxide and free aluminum, try some shorter etches. By "good", iI mean... once your etch is truly broken in, the tech data sheets for a couple common "proprietary" blends will actually be useful to you in terms of aluminum management and concentration calculations, temp, and immersion time. There's a window to stay within for all; it's a bit 3 dimensional.
I can think of a couple products offhand whose published/posted test protocols are so basic as to be near-universal. Poke around and cross reference TDS and SDS ;)
With etch... sometimes less is more!
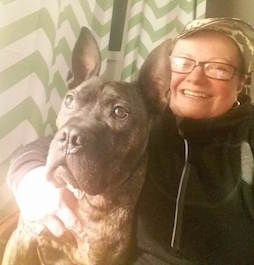
Rachel Mackintosh
lab rat - Greenfield, Vermont
getting rained on so much as to question whether I'm actually a wharf rat or a swamp rat. Happy New England summer, y'all.
June 25, 2023
⇩ Related postings, oldest first ⇩
Q. Hi. I've been trying my hand at anodizing and dyeing aluminum, and have encountered a problem. The technique is essentially that found in an associated Web page: Degrease in sodium hydroxide, rinse, anodize in 20% sulfuric acid with current density 0.4 amps per square inch, rinse, soak in dye (Nigrosin Bio Stain, black).
The problem is, no color is absorbed; none, absolutely none.
It appears that an oxide layer has formed, but it is hard to tell how thick it is. It seems to be uniform over the entire surface of the parts. The materials treated were 5056 and 2024 aluminum alloys; all wires were pure aluminum. Time in the anodizing bath was 1 hour. I started with the dye bath at room temperature, then after about 20 minutes slowly raised its temperature to boiling (took about 30 more minutes). Any suggestions as to what is (or is not) happening here would be greatly appreciated.
JPL, Pasadena, California
1995
Treatment &
Finishing of
Aluminium and
Its Alloys"
by Wernick, Pinner
& Sheasby
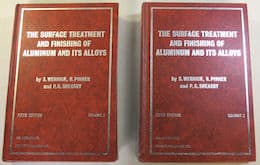
on eBay or Amazon
or AbeBooks
(affil link)
A. I'm not a practicing anodizer but I think the sequence should be: 1) clean/etch, 2) deoxidize, 3) desmut, 4) anodize, 5) dye, 6) seal. Step 1 is surface clean and finish, while step 2 should remove the existing oxide layer. Step 3 removes the inclusions such as copper. I may be wrong in one or more details, but I'm pretty sure that you have to remove the existing oxide layer before you can form a new one.
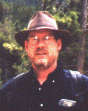
Bill Vins
microwave & cable assemblies - Mesa (what a place-a), Arizona
A. Suggest you try cleaning the item in a mild detergent ( up to 150 °F. ) to remove any organic contamination prior to "degreasing" in sodium hydroxide. The sodium hydroxide attacks uncontaminated areas while removing any organic films that may be present causing a selective attack that will create an etched pattern. We obtain black coatings on 2,000 series in 30 minutes and in 50 minutes for the 5,000 series. Our parameters are typical of most anodizing baths for aluminum: 15% sulfuric acid, 68-72 deg. F., and 12 amps/sq ft.. Solution agitation is important to dissipate the substantial heat generated.
If either the temperature, time, and or concentration of solution is exceeded, or there is insufficient agitation to dissipate the heat, the solvent action of the solution will attack the coating as it is being created. This could partially or totally re-dissolve the coating. These conditions will provide a "Standard" anodize coating as opposed to a "Hard anodize" coating. The conditions you are using are more toward the "hard anodize" type coating, but they still do not sound correct for a proper film to form. .4 amps/ sq. in. ( 57 amps/ sq. ft. ) exceeds our "hard anodize" method of 36 amps/sq. ft.. The 20 % concentration is o.k. but the temperature should be at 32-40 °F. These conditions will create a periodic drop in voltage as the coating builds - then an increase in voltage is necessary to maintain the 36 amps/ sq. ft. It is common to start at 20 volts d.c. and end at 40-50 volts over a period of 30-50 minutes.
Even if you acquire a proper "hard" anodize coating, the density is much greater than "Standard" anodize coatings. The porosity of "Standard anodize" coatings is what makes them easier to dye. We have difficulty dyeing "Hard anodize" coatings for this reason. Last, if you have a created a coating at all, I believe it is being attacked by the extreme temperatures. A properly formed coating will be non-conductive and have a color ranging form satin-aluminum below .0004 tk. to dark bronze and black ( depending on alloy ) at .003 tk.. One more thing, you might want to check the terminal connections
- are you sure the item to be coated is "positive"? - and a proper cathode material is used ( aluminum or lead is recommended).
Q, A, or Comment on THIS thread -or- Start a NEW Thread