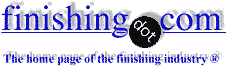
-----
Cyanide Copper plating vs. Acid Copper Plating

Q. Can someone tell me the practical differences between Cyanide Copper plating and Acid Copper Plating. I have a line of Cast Bronze designs about the size of a lady's brooch pin (that has open-work throughout), and I am trying to Bright copper plate over nickel.
My plater tells me that he is getting spotting from areas of my original bronze castings which suck in his plating solution, and when the piece is dry, the areas which have the porosity slowly release the cyanide copper solution causing discoloring (spotting) in those areas. He thinks that the porosity is the problem, and that I should try someone who does Acid Copper plating. All I know is that acid copper usually plates thicker and maybe less bright, but is there something about the cyanide that would cause this to happen? Will Acid copper be an improvement ?
Also what I am doing is bright copper over nickel over the bronze castings. I am also trying to get a clear enamel coating baked over this to prevent oxidization. Is my plater right about the spotting?, and are there finishers who do this kind of three step process? I have used lacquer baked coatings, but they are not durable enough. First I need to stop the spotting … any clues?
1995
A. Cyanide solutions are difficult to rinse and are more prone to "spot out" than acid solutions. They deposit a more even plating thickness. And acid copper can't be used on materials that come substantially ahead of it in the EMF activity series because it will immersion deposit, leaving a powdery non-adherent plate. That covers the principal differences, and I agree with your plater (and applaud his honesty) in suggesting that acid copper may be the way to go if you can't reduce the porosity of the castings.
Be prepared to answer whether your parts are barrel plateable or must be racked, then contact the plating shops listed in this directory. Your problem is not a special or unusual one and many jobshops can solve it for you.
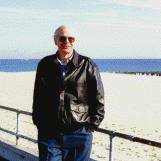
Ted Mooney, P.E.
Striving to live Aloha
finishing.com - Pine Beach, New Jersey
Q. Wondering if you can provide detailed information on, cyanide copper plating of lead. Web sites, text books, articles, etc. I've been searching for some time and am only finding info. from Dupont, etc.
Daren McCann 2000- Lewiston Idaho
A. Hello, Daren.
If you search this site for "cyanide copper plating onto lead", you will find some detailed info. In terms of literature references though, a solution to the problem may be that you divide your question about cyanide copper plating onto lead into two parts: cyanide copper plating, and plating onto lead. Once you do that you'll find many articles, or you can start with any of the "must have" plating books. Best of luck.
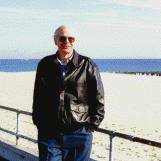
Ted Mooney, P.E.
Striving to live Aloha
finishing.com - Pine Beach, New Jersey
Q. I want to know if the acid copper overcome the problem of pores in the zinc die-cast.
Mohamed Basiony- EGYPT
2002
A. Your strike plate before acid copper is more important in getting a good initial deposit in the pores that will eventually fill with electroplated metal, such as are present. Some porosity will not be filled in by the plating process.
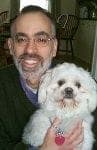

Tom Pullizzi
Falls Township, Pennsylvania
A. Hi. Poor quality die castings are not plateable. They must be inspected for porosity and cold shuts, and bad ones discarded. If it is impossible to improve the quality of the castings, it may be possible to vacuum impregnate them before plating.
Regards,
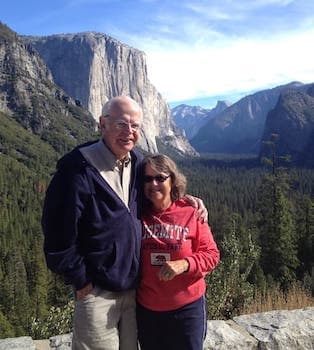
Ted Mooney, P.E. RET
Striving to live Aloha
finishing.com - Pine Beach, New Jersey
Porosity in acid copper in plating on plastics
Q. Hi everybody, my name is Nestor and I'm from Mexico; I'm process supervisor in a POP industry. We have a process with electroless nickel and copper immersion; the problem is when the material comes out from the acid copper it shows porosity. We control all the concentration in baths, we also control temperatures, what could cause the porosity? The pH is okay in every bath, above 9 in electroless and in the pre-activator (before copper immersion). 4 gr/l of sulfuric acid; we also control the pH of rinses after electroless (between 5 and 6).
Nestor JimenezProcess supervisor - Mexico
April 12, 2016
![]() |
A. Hello Nestor, you don't mention the size of parts you are plating, so I don't know if a water break test is possible. The pre clean process is the first place to look. Good tank filtration is also important.I would run a controlled test sample lot. Remove the sample at each process, dry and examine the surface under magnification, a minimum of 10X. Look for pin holes or irregularities on the surface. This problem could go as far back as the etching of the plastic. If all examinations look good, measure the thickness of each coating to ensure you are getting adequate coverage. So, close examination at each process is the key here, and starting with a clean surface. Mark BakerProcess Engineering - Phoenix, Arizona USA Good day Nestor. Aerotek Mfg. Ltd. - Whitby, Ontario, Canada |
Q. Hi, thanks for your advice, I'm going to try it. Did I mention that we have 3 rinses after every bath -- except electroless Nickel, we have only 2 rinses after electroless and then the pre activator (sulfuric acid at 4 gr/l) and then the copper immersion. The design of the racks could cause porosity (sometimes only appears in the pieces on the rack in the middle). And what do you mean with "water break"? Can I go directly from electroless to pre-activator without rinses?
Nestor Jimenez [returning]- Puebla, Mexico
A. Hello Nestor, water break testing is a step taken to determine the cleanliness of the part after the pre - clean cycle. When coming out of a rinse the water should flow evenly (sheeting) from the part's surface. If not, there are areas on the part that need attention. I would not recommend going without rinsing after the immersion process.
Mark BakerProcess Engineering - Phoenix, Arizona USA
Q, A, or Comment on THIS thread -or- Start a NEW Thread