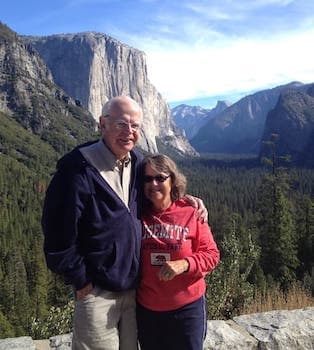
Curated with aloha by
Ted Mooney, P.E. RET
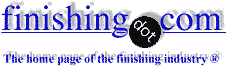
The authoritative public forum
for Metal Finishing 1989-2025
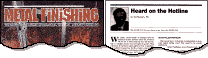
-----
Gold plating of wave guides
Current question and answers:
Q. Need a Means to Coat Interior of a 28 mm x 14 mm Rectangle MW Wave guide with Gold coating of 1 Micron. Can I get A Response ASAP?
Suryanarayanan SubramanaiamBuyer - Hyderabad TS INDIA
July 3, 2018
A. Hi. You'll need internal anodes (probably platinum coated titanium wire or other DSA anodes), and some sort of pumping for solution exchange in those recesses, but I see no fundamental reason it can't be electroplated with gold to a micron thickness. What is it made of, copper? Good luck!
Luck & Regards,
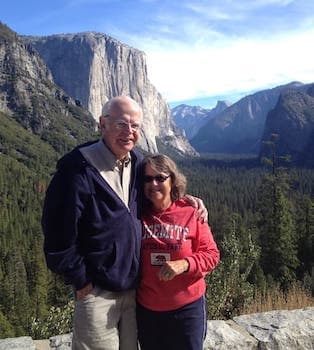
Ted Mooney, P.E. RET
Striving to live Aloha
finishing.com - Pine Beach, New Jersey
February 2021
⇩ Related postings, oldest first ⇩
Q. I am working for West Virginia University. We have a microwave cavity that needs to be plated with gold (1-2 µm).
Maybe it sounds simple for professionals but not for us. We have tried phosphate gold solution (1.3 g KAu(CN)2, 120 g K2HPO4, 30 g KH2PO4 per/L) and current density 1 mA/cm2. The gold layer looks matte and brownish. Is there any way to get a shiny finish without polishing?
We would be glad if you could help us with advice. Thank you.
Alex K [last name deleted for privacy by Editor]- West Virginia, USA
1995
A. First, what type of waveguide/cavity material? I'll assume Copper although Aluminum is also possible as well as ferrous based (you did say you were in an edu).
The next issue is that of the matte brown finish. Sounds like you're burning the plate. I suggest a Hull cell analysis. Essentially, you plate up on a brass shim that is placed at an angle to the anode. This allows you to compare varying current density to plated appearance.
I am also assuming that you are using an appropriate anode w/ appropriate surface area. A platinum coated anode works best although stainless steel can be used for short periods of time without damaging the bath. The surface area of the anode to cathode should be about 1:1 although 2:1 will be ok.
Good luck, Jeff
- El Granada, California
A. I would recommend you look at Plasma Enriched Deposition (aka Sputter coating) your university will have this facility I am sure. The film will have better adhesion, better structure and better uniformity.
Vijay Simha- Bangalore, India
2003
by Jay H. Newman
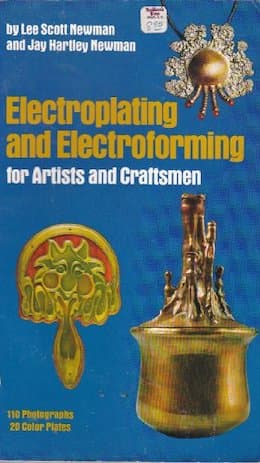
on AbeBooks
or eBay or
Amazon
(affil links)
A. Hi Alex,
Most professionals buy proprietary gold plating solutions rather than trying to make them from scratch according to old formulas. That way you get the most modern approaches, and you get the supplier's expertise and lab working for you. That's perhaps what you might want to try. Gold Touch [a finishing.com supporting advertiser] and Technic specialize in this.
Jeff,
As you probably know, many wave guides are electroformed because it's such a great way to build complicated hollow shapes. Suppose Alex were to polish an aluminum or wax mandrel, then electroplate it with gold, then back it up and give it integrity by electroforming with copper or nickel, then dissolve away the aluminum or wax. He'd have a copper or nickel waveguide with a highly polished gold surface. From your experience do you see any reason this wouldn't be feasible? Thanks.
Vijay,
Thanks for the feedback. But wave guides often are electroformed, and it's a good application for gold electroplating. The third advantage you listed for sputtering is true, i.e., that it's easier to get coatings of uniform thickness with sputtering than plating, but the other two purported advantages may not be. In many cases electroplating yields 'perfect adhesion', which means that it is impossible to separate the materials at the boundary -- either the coating or the substrate will rip instead. Plus, this application doesn't sound line-of-sight where sputtering would work; it sounds like Alex wants to plate the cavity (interior) of a waveguide, not the outside of it.
Readers, learn more on similar issues--
Topic 22456 proposes a cleaning sequence for copper wave guides that might be applicable. Topics 1799 & 39679 address electroforming of wave guides. Topic 49813 is about a cracking problem in plating of copper electroforms. Thread 085 addresses the general issue of making robust copper electroforms. Patient application of the search engine will uncover other related topics.
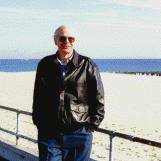
Ted Mooney, P.E.
Striving to live Aloha
finishing.com - Pine Beach, New Jersey
Q, A, or Comment on THIS thread -or- Start a NEW Thread