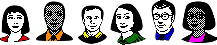
Metal finishing Q&As since 1989
-----
Is bronze galvanically compatible with Cr-Mo-V steel?
Q. We recently started using impeller rotor(Cr-Mo-V steel) supported on bronze rollers as a temporary storage. Later we found that the rotor got corroded/pits at the contact point. Is it because of galvanic corrosion ?
Is there any solution to prevent this (still keeping rotor on bronze rollers)
- Baroda India
February 13, 2021
A. Hi Kumar. My understanding, and I could be wrong, is that the Cr-Mo-V steel you are speaking of is a low alloy steel, not anything approaching stainless steel. I couldn't quickly find its potentials or place in the seawater series, and we'd probably need to know the exact composition, but I think it's basically the same as plain carbon steel, such that most bronzes are significantly more noble. So I think galvanic corrosion is a real possibility.
If you can send a sketch or picture so we understand what you are speaking of, suggestions may be possible regarding improving the rollers or the contact arrangement -- but I have no real mental picture of what you are talking about :-(
So the best I can suggest for now is make sure everything is bone dry, and control the humidity in the storage area. Galvanic corrosion won't happen without moisture.
Luck & Regards,
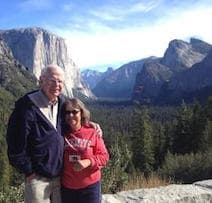
Ted Mooney, P.E. RET
Striving to live Aloha
finishing.com - Pine Beach, New Jersey
February 2021
Q. Thank you Ted for the quick Reply. Further info on my query.
1. Key elements of the steel are C:0.3%, Ni:2.25%, Cr 1.25%, V:0.15, Mo:0.7%
2.A rotor is made out of the above composition and is simply placed on temporary stand (on either end of the rotor, just like a cantilever beam) having bronze rollers. There is a direct contact between rollers and rotor.
3. Temporary rust preventive is used to protect the rotor from moisture, but still I saw pitting on rotor at the contact point between rollers and rotor.
Any advice on understanding the pitting phenomenon would be helpful in choosing the roller material
- Baroda, India
February 15, 2021
A. Hi again. My first thought was that it is indeed galvanic corrosion, and that removing all moisture from the rotor, the roller, and the environment would be the best defense if practical. That alloy is not corrosion-resisting steel.
I was hoping for a better mental picture of the situation to avoid 101 "ifs, ands, & buts". Is the rotor thimble-sized or many tons? If it's very heavy it could well be extruding any rust-preventative away from the contact area so you have no protection at the critical point. Perhaps the rollers could be nylon, teflon, or plastisol coated but I have no concept of clearances and scale of the installation. And I don't know whether storage is outside, or in a climate-controlled environment, or otherwise. Maybe just lay a sheet of PVC between the thimble and roller, or does this defeat the purpose of the rollers?
Luck & Regards,
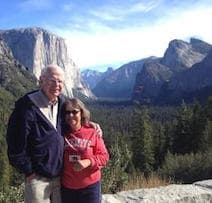
Ted Mooney, P.E. RET
Striving to live Aloha
finishing.com - Pine Beach, New Jersey
February 2021
A. If you want to determine the galvanic potential between your steel alloy and brass, a quick and easy test is described in Topic 38853 on this great website. (You don't need Epsom Salts [Magnesium sulphate]; any electrolyte will work in this test.) Common salt (Sodium Chloride) would be a great choice. If you want to reduce the galvanic potential, you could always have the steel plated with bronze.
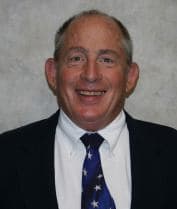
Tom Rochester
CTO - Jackson, Michigan, USA
Plating Systems & Technologies, Inc.

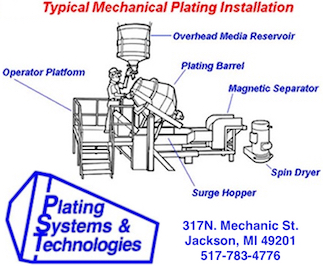
February 15, 2021
February 17, 2021
Q. Thanks Ted and Tom for giving some insight on the problem approach. sorry for not giving the full info.
1. The rotor is approx. 5 tons ... and is kept in open atmosphere.
2. Sample pic (rotor at one end) is attached for quick view.
Any suggestions
Kumar Nivas [returning]- India Baroda
A. Aluminum sounds like a good idea, along with a rust preventive grease.
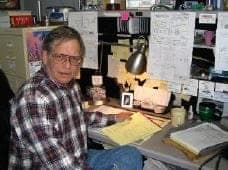
Jeffrey Holmes, CEF
Spartanburg, South Carolina
May 2, 2021
Q, A, or Comment on THIS thread -or- Start a NEW Thread