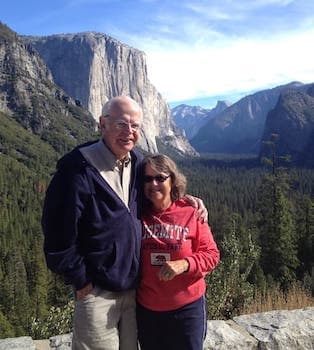
Curated with aloha by
Ted Mooney, P.E. RET
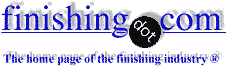
The authoritative public forum
for Metal Finishing 1989-2025
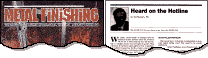
-----
Pre-Galvanized Sheet vs. Post-Galvanized Components
Q. Sir,
This is regarding Pre-coated galvanized sheet vs. Post-coated galvanized sheet (CRCA). As precoated sheet is processed after coating, rust is forming along the cut edge. Overall, which performs better with respect to corrosion, pre-coated or post coated galvanised sheet?
GopinathTVS-Electronics - Chennai, Tamilnadu, India
2002
A. Hi Gopinath. Well, yes, pre-coated sheet rusts on the edges because there is no zinc coverage there. The galvanizing on the rest of the sheet offers some degree of cathodic protection from the rusting, but it's far from perfect. There would no post-coated products if pre-coating, which is cheaper and easier, performed as well as post-coating; it doesn't.
Full name please! This is both a place of camaraderie and a forum where we can best understand your situation by reviewing your previous postings, but we have many posters by the name of Gopinath, and don't know which of them, if any, is you. Thanks!
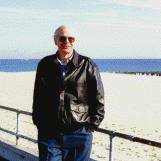
Ted Mooney, P.E.
Striving to live Aloha
finishing.com - Pine Beach, New Jersey
2002
Q. Do pre-galvanized steel sheets go through a hot dip process or is it some other galvanizing method? Apart from the edges having no corrosion protection is there any difference between pre-galvanized & post-galvanized steel
Thanks,
Engineer - Kuwait
2007
A. Hi Jason. Steel coil can be pre-coated via hot dip galvanizing or via zinc electroplating (which is usually called 'electrogalvanizing' when done in continuous style on coiled strip); or the components can be post-coated via hot dip galvanizing or via zinc electroplating. (There are other ways of applying a zinc coating as well, of course).
When doing pre-coating on continuous strip via hot dipping, it becomes practical to limit/control the zinc thickness via 'wiping' away any excess thickness from the sheet, and it is always very easy to limit the thickness of zinc electroplating/electrogalvanizing by reducing either the plating time or applied current.
When doing post-coating, again it is easy to control/limit the zinc electroplating thickness by controlling plating time or current. But with post-coating via hot dip galvanizing, whatever zinc doesn't drip off doesn't drip off.
All four approaches are viable, with post-fabrication via hot dipping usually being much thicker (and more corrosion resistant) than the other processes.
So, yes, the basic differences are whether the sheared edges have a coating, but also the thickness of the coating. There are some metallurgical differences between hot-dipped zinc and electroplated zinc but the most generally accepted idea is that the corrosion resistance of the coating is basically proportional to its thickness, summarized as "zinc is zinc" :-)
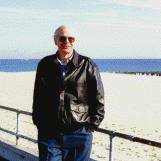
Ted Mooney, P.E.
Striving to live Aloha
finishing.com - Pine Beach, New Jersey
2007
Multiple threads merged: please forgive chronology errors and repetition 🙂
August 3, 2009
Q. Hi everybody,
I work as Research Engineer in Liège (Belgium), and I'm going to start a study comparing the performances of pre-galvanized steel vs. post-galvanized. Actually I'm mostly gathering information on this subject in order to better plan my activities; but, honestly, I'm not finding a lot of information about it.
Probably someone of you have great experience on this subject that can be useful and can allow me to save time and energies.
I just wanted to ask you if you can tell me some differences (durability in particular conditions, pro & con, price difference, etc.) or if you can address me to some specific bibliographical reference in order to speed up my gathering of information and to improve my "culture" on this topic pretty fast.
Thank you for your answer and for the time you're kindly spending for me.
Best regards,
Researcher - Liège, Belgium
August 4, 2009
A. Sir:
My publication, "Characteristics of Hot Galvanized, Metalized and Bare Edged Galvanized Sheet Products," METAL FINISHING,pages 63-68, May 1985, may be of interest to you. You can obtain a copy through interlibrary loan from any large library for the copying cost.
There was a major white rust problem when a cooling coil exchange unit changed from post galvanizing frames to galvanized sheet formed before bending. My research showed that the much higher aluminum content (e.g. 0.15% in the sheet) was the cause. Galvanizing after forming the product normally has only about 0.002% aluminum in the zinc coating.
Regards, Dr. Thomas H. Cook, Hot Springs, South Dakota, USA
Galvanizing Consultant - Hot Springs, South Dakota, USA
? What do you mean by "pre galvanized" and "post galvanized" steels?
Steel before it is galvanized and steel after it is galvanized?
Or items that are galvanized after fabrication, compared with materials made of steel galvanized before fabrication?
Clarifying your question will help obtaining answers.
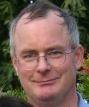
Geoff Crowley
Crithwood Ltd.
Westfield, Scotland, UK
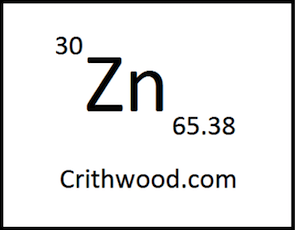
August 5, 2009
August 17, 2009
Dr Cook: Many thanks for your interest and your kind answer, I'm trying to get the article you've mentioned, and think it can be useful.
Q. Mr. Crowley: Thanks for your interest, maybe I've used the wrong words:
With "pre-galvanized" I mean steel galvanized in continuous process (so, galvanized before bending or cutting).
With "post-galvanized", on the other hand, I mean the "classical" galvanizing process, where the Zinc is laid onto the finished pieces.
I hope I've clarified the question.
Best regards,
- Liège, Belgium
A. Pre-galvanized usually is in sheet form, though sometimes pipe. It has a much thinner zinc coating than items fabricated first then hot dip galvanized.
The thickness of the zinc is very carefully controlled in pregalvanized sheet, etc., but has little control in post fabrication galvanizing. "Post galv" has a wide variability of coating thickness as well as a much higher average thickness.
The life expectancy of a galvanized finish is directly proportional to the thickness of the zinc coating, so in general, post galv will last longer, perhaps by as much as 5-10 times, but as thickness of coating is also dependent on immersion time which in turn is proportional to thickness of the steel, then the difference in life expectancy is hard to compare.
Very few items of thin sheet metal are fabricated first then galvanized as distortion becomes an issue. Pregalv is typically stretched and leveled after galv, making it very smooth, flat finish. That's not possible with post galv.
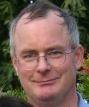
Geoff Crowley
Crithwood Ltd.
Westfield, Scotland, UK
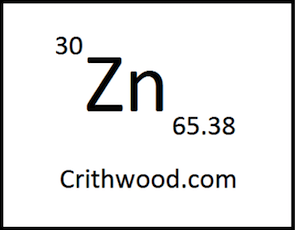
August 20, 2009
Multiple threads merged: please forgive chronology errors and repetition 🙂
Edge coating of galvanized strip
Q. We are trying to use sheared galvanized strip to replace a hot dip galvanized product used for field agricultural applications. The galvanized strip is G60 or G90 weight galvanizing but the edges are sheared from a wide coil and have no galvanizing. The strip is 16 or 14 gauge thick material. Is there a practical way to coat the edges of this strip either when it is still in coil form or after it has been cut into 2'-3' long strips? The strip width is 1".
Pike Bartlettproduct designer - Friendship, ME, US
September 14, 2009
October 1, 2009
A. Sir:
I recommend that you get my article through interlibrary loan from any good sized library:
Characteristics of Hot Galvanized, Metallized and Bare Edged Galvanized Sheet Products, Metal Finishing, 63-68, May 1985.
Regards,
Galvanizing Consultant - Hot Springs, South Dakota, USA
Multiple threads merged: please forgive chronology errors and repetition 🙂
Flat rolled galvanized steel slit edge integrity
Flat Rolled (.099" thickness), G90 coating. After the coil is slit, what protection does the slit edge have against rust? Does the Galvanize "cure" over the slit edge to protect against rust?
Joe Muellersteel supplier - Boise, Idaho
November 4, 2009
November 6, 2009
Sir:
My published article, "Characteristics of Hot Galvanized, metallized and Bare Edged Galvanized Sheet Products," in METAL FINISHING, pages 63-68, May 1985 can be obtained through a large library via interlibrary loan for the cost of copies. In the slitting process some zinc is smeared across the cut "bare" edge. Also some reaction products (zinc+2 ions) get onto the edge to help protect the "bare" edge. Also there is an electrolytic reaction in which the zinc is the anode and is preferentially corroded. The real problem about corrosion relates to the fact that galvanized sheet has much more aluminum in the coating and can cause white rust under certain conditions like cooling coils on the top of a building.
Regards,
Galvanizing Consultant - Hot Springs, South Dakota, USA
July 7, 2014
Q. Dear Sir,
Actually we are Designing the LV Drive Sheet Boxes, in which we were using the material previously as C.R.C.A sheet with Zinc finish and then powder coating.
Now we want to go for Galvanized steel (Pre-Galvanized) sheet with powder coating for Box.
What Material notes should I write in Drawing so that supplier can easily understand the Steel? Is there any ISO or ASTM Standards available for the Pre-galvanized sheet?
From your posts I want to know if Electro galvanized steel is the same as pre galvanized steel, please confirm ASAP.
Thanks in advance.
Regards
Researcher - Ahmedabad,Gujarat, India
A. Hi Asit. We appended your inquiry to a thread which previously answered that not all pre-galvanized sheet is electrogalvanized -- sheet can also be pre hot dip coated.
I think one of your issues will be how thick you want the coating to be. You might review thread 7666 "Hot Dipped Galvanized Coatings: G90 vs. G60" as a starting point for that, and for a discussion of your question about standards. Good luck.
Regards,
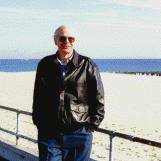
Ted Mooney, P.E.
Striving to live Aloha
finishing.com - Pine Beach, New Jersey
July 2014
Coatings for bare edges of zinc plated steel
Q. We are using cut to length sections of 35mm DIN rail in zinc plated steel materials. The cut edges on each end are left unprotected by the zinc plating. I was thinking about specifying coating with a clear acrylic sealer. Is there a better option?
Thanks,
John
- Bend, Oregon USA
February 9, 2015
A. Hi John. I would conjecture that a cold galvanizing compound (zinc-rich paint), widely used on chain link fencing installations, would be a better way to treat exposed edges than a clear acrylic because of the galvanic protection, but I can't quote a study to prove it.
Regards,
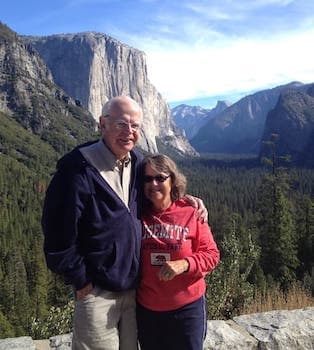
Ted Mooney, P.E. RET
Striving to live Aloha
finishing.com - Pine Beach, New Jersey
January 2016
Q. Hi All, many thanks for all the information to date. But is there any other way of treating the cut edges on pre-galvanised sheet after production of components that will give better edge corrosion performance?
Is there a brush on product that is compatible with powder coating?
We will powder coat but would feel a little more confident if we had a gauge on life expectancy
Many thanks
Adam Canty
HUXT Ltd - Hull, East Yorkshire, UK
September 4, 2016
A. Hi Adam. If you are going to powder coat the galvanized parts, you should zinc phosphatize the items after galvanizing them anyway -- and this should provide fine corrosion resistance. If you are talking only about cut edges, rather than holes in the items, you might be able to 'roll the edges'. Good luck.
Regards,
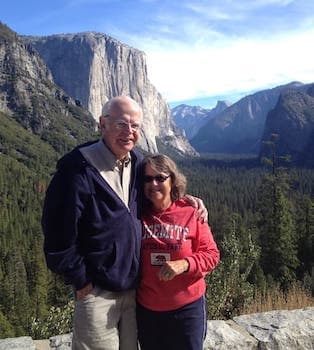
Ted Mooney, P.E. RET
Striving to live Aloha
finishing.com - Pine Beach, New Jersey
November 2016
ACRONYMS:
ERW = Electro-Resistance Welded
Q. Hi Everyone,
I am working in Fire fighting systems and need to submit for approval the pipe. Mentioned in the drawing is: ASTM A53
[affil. link] Grade-B Carbon Steel Pipe.
Now we need approval for ERW type and galvanizing after fabrication, not before due to cost impact.
As per my understanding ASTM A53
[affil. link] Grade-B Carbon Steel Pipe covers ERW, but not sure about the galvanizing after fabrication.
I need to know which standard should I mention in my approval request which will indicate ERW and galvanized after fabrication of pipe.
Yours assistance will be very helpful for me.
Thanks
- Jubail, Saudi Arabia
Corrosion Resistance of Pregalvanized Steel: Edges Laser vs. Shear/Punch
October 26, 2017Q. I am trying to find research related to a comparison of cutting processes in pre-galvanized G90 sheet steel. There is an opinion being floated, that laser cutting destroys the "self healing" properties of G90 steel. We typically process .059" up to .168" thicknesses on shears and turret punches. Can anyone point me to any studies comparing the "self healing" action between these two processes, or is this even a viable question to be asking?
Thank you, in advance for anyone who may provide some insight.
- Champaign, Illinois, USA
----
Ed. note: We appended your inquiry to a thread where Dr. Cook mentions his article which attempted to determine the value of 'smeared' zinc from shearing/punching.
A. Hello,
Once you have punched a hole via laser or press you have penetrated the coating. So both the pieces are subject to corrosion. The difference is insignificant laser vs press. Ideally, fabrication is done first and then the steel is Hot dip Galvanised or Coated as per process requirement.
INDANA STEEL PVT.LTD - Kolkata,West bengal, India
October 29, 2017
Q. Hi,
Can anyone let me know that is there any self-healing process there for Pre Galvanised sheet. We are using Pre galvanised steel for Solar structures and they are having rust on the cut edges. We want to know if there is any study reference which can give us an idea whether the rust will spread from the cutting edge or not? Also we want to know whether there any chance that the properties of the steel will stop the rust from spreading further.
- Hyderabad, Telangana, India
November 9, 2017
A. The main differences between pregalvanized sheet and post fabrication galvanized are that pregalv is very flat sheet (having been stretch leveled during the process) and with thin coating. Post galv more likely to have some distortion, not be float, and have much thicker coating.
The thicker the coating the more the so called self healing effect. Actually this is just the zinc acting as a local anode, and it's effective to about 3-4 mm away from the zinc. Cut edges should be protected by the zinc either side, but the thicker that coating the better it will be. The chemistry of the steel doesn't normal have any direct effect on speed of rusting, but could have an indirect one by way of affecting the steel reactivity with zinc, causing either thinner or thicker coating. (I'm not allowing for alloyed steels or Corten, etc.)
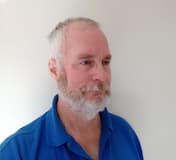
Geoff Crowley, galvanizing consultant
Crithwood Ltd.

Bathgate, Scotland, UK
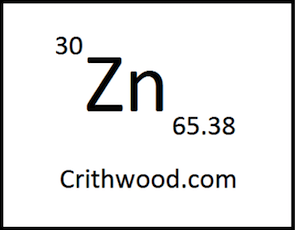
November 11, 2017
A. Hi. Although I don't have the deep experience with galvanizing of Dr. Cook and Geoff Crowley, I can add that cut edges and uncoated steel will always represent somewhat of an additional problem in that dependance on galvanic protection of bare steel inherently interferes with the ability of corrosion products on the rest of the component to slow or limit corrosion :-(
Consider, for example, that nickel plating can provide corrosion protection to steel even though it is cathodic to it. It does so as a "barrier layer coating", encapsulating the steel so it is not exposed to the environment. To a certain extent the carbonate corrosion products on galvanized steel form a barrier layer coating on the zinc which reduces its exposure to the environment and slows its corrosion; but obviously a zinc atom which is being consumed in the protection of a bare steel edge cannot simultaneously be forming a barrier layer on itself. Dr. Cook and presumably others have attempted to quantify the issue but it is a complex one, such that we can simply say that bare edges are always disadvantageous.
Luck & Regards,
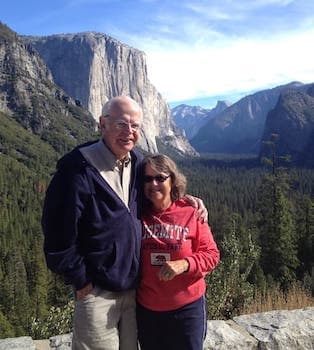
Ted Mooney, P.E. RET
Striving to live Aloha
finishing.com - Pine Beach, New Jersey
October 2020
Q. Hi All,
I am a mechanical engineer, working in telecom sector. I am facing cut edge corrosion issue on pre-galvanized steel products. As per some documents if the sheet size is 2 mm the corrosion will not affect the structural performance of the product. I could not able to find the details of sheets which have more thickness (3-5 mm). Any suggestions regarding this would be helpful.
Even though the corrosion will not create any performance issue on the 2 mm thickness products, it's creating a quality issue. Is there any way to fix that cut edge corrosion issue? I understand from the previous threads that Zinc paints can solve the issue, but for that is any surface treatment required? Whether the painting can be done after the installation in the field? if there are any other ways to fix the issue kindly let me know.
Thanks
- Bangalore, India
October 28, 2020
A. This sounds more an issue of poor specification that poor coating.
Pregalvanized sheet always suffers from cut edge lack of protection.
If its too late and someone has specified this in error and you are trying to salvage the situation, then using a zinc rich paint could solve the problem. If its fresh galvanizing and clean, then applying a painted coating to the edges will help to protect them. It's will add nothing to the aesthetics, and be a very obvious repair, but will have functionality.
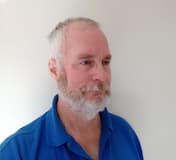
Geoff Crowley, galvanizing consultant
Crithwood Ltd.

Bathgate, Scotland, UK
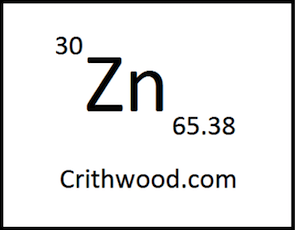
November 26, 2020
Thank you Geoff Crowley for the clarification. As of now we have requested our supplier to do some modification in the shearing process to reduce the rough edges area. I am waiting for their observation response. I will check with them regarding the surface coating quality as well.
- Bangalore, India
November 30, 2020

Q, A, or Comment on THIS thread -or- Start a NEW Thread