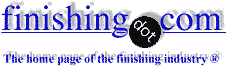
-----
Salt spray and statistics
Q. I have a bit of a scholarly question...
Does anyone have any information about applying statistics to salt spray test results? I am knowledgeable, but not an expert in statistics. I am interested in applying statistical tools to make conclusions about salt spray data.
One of the problems is that salt spray data is taken daily, not constantly. I think it may be safe to treat the data as if it was taken all day and night. Another is the unequal variance. A part does not have an equal probability of being +24 hours than -24 hours from the average.
The reason we want to do this is so that we can make conclusions about these tests instead of just eyeballing the data and going with however we want to interpret the data. If anyone has the foggiest idea on this topic, let me know!

Tim Neveau
Rochester Hills, Michigan
2000
A. Hey Timothy,
ASTM B117 (the test method for Salt Spray) has been reduced in rank (from a test method to a guide) because of the variation you have noted. The variation is present from company to company and even in the same machine, batch to batch. Statistics will not introduce a measure of certainty into a uncertain test. You will need to use the salt spray test for as long as suppliers write it into specs., but don't try to make it more than it is, a go, no-go test. The salt spray test as a tool, can be used in a general way, to control and improve your process but be careful not to read too much into the results.
Regards,
Fred Mueller, CEF- Royersford, Pennsylvania
2000
A. There are a number of ways an operator can influence the outcome of salt spray testing, both for better or for worse.
Overall trend information would be more presentable if you applied it to a data base like Excel which can be programed to do statistical number crunching for you and presenting you with the outcome in a great number of formats. Interpretation of what it means is up to you.
James Watts- Navarre, Florida
2000
A. Sir, the subject under discussion is of genuine interest to many engineers and consultants as the specifications of many manufacturers are including the salt spray hrs for their plated parts without however giving guidelines for inspection after ss tests leading to non-statistical or qualitative judgments. The ss tests have been proved to be very unreliable and it also seems to depend on the type of chromate coating, the case history, aging of the parts before ss test. There also seems to be some incongruent results between ss tests and field performance as well as atmospheric tests.
One suggestion is the ss tests on the control specimens can be carried out until white corrosion and a statistical average of the area affected can be arrived at to determine the an acceptable standard. The testing until white corrosion seems to be more reliable and reproducible for parts with different chronological events. Thanks,
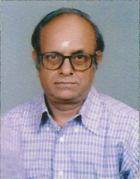
Subramanian Ramajayam
consultant - Bangalore, India
2000
A. Dear Mr Neveau,
I endorse Mr Mueller's views on SST. It is indeed a revelation to know that ASTM has taken a lead in demoting the SST to a guide rather than a standard test method. I hope that other equivalent bodies realise the futility of over-dependence on the SST as a blind judgment on plating results without endorsing process integrity first.
However without debunking the whole SST completely, I believe that the knowledge that exists today and the process improvements that have taken place over the years, would not have been possible without a yardstick like the SST in the first place, and SST statistical data linked to equally reliable process control data will lead to better understanding of the work we do and how we choose to interpret it.
You will have to build up your own data bank in the first place and use your own results to interpret your work. As you have rightly said that we interpret our results the way we want to look at them is true, but to get better objectivity it is invaluable help to be able to get outside opinions in ways like this.
Much of the work done by chaps like us lies wasted with us, and the Editors of this site deserve credit for bringing us together. As President Bill Clinton said during his visit to India last week that we should look for a higher purpose in our work, I hope we too can share from our mutual experiences in bettering the work that we all do.
Regards,
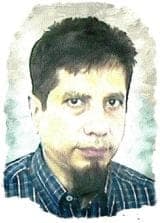
Khozem Vahaanwala
Saify Ind

Bengaluru, Karnataka, India
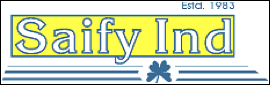
2000
Thank you for your kind regard for our mutual efforts here, Mr. Vahanwala.
I tend to agree with everyone here, most especially Mr. Ramajayam--not so much because testing to some degree of white rust is better than testing to some other degree of white rust or to red rust, but because testing multiple ways is superior to fine tuning a single test.
Salt spray testing is a somewhat useful but inaccurate, and often downright misleading, indicator of real world performance. So working to make the "passing criteria" for your neutral salt spray needle sharp offers precision with no accuracy, and will probably prove less productive than seeing what other kinds of predictive tests you can also implement. A coating which lasts 10 percent longer to some particular corrosion point in neutral salt spray testing is not necessarily a better coating at all; but a coating which performs better in three disparate tests probably really is better. I would suggest investigating the CAMRI test as a very simple supplement to ASTM B117 salt spray testing. Good luck.
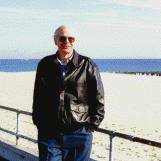
Ted Mooney, P.E.
Striving to live Aloha
finishing.com - Pine Beach, New Jersey
2000
Q. Can Fred Mueller or anyone possibly advise the reference(s) for his statement that ASTM B117 has been "demoted"? Thanks in advance.
Peter Weber- Creil, France
2000
Extrapolating salt spray results?
Q. I am wondering if there is any formula or general rule of thumb for extrapolating salt spray test results.
I have data showing a 1.6mm creep at 500 hours and wondering if there is anything to approximate what it will be at 1000 hrs?
Quality Engineer - Osceola, Wisconsin, USA
May 13, 2015
A. Doug,
You only have one data point, so any such approximation would be making an enormous assumption on the linearity of the effect you are measuring. Experience tells us that we should generally expect such things to behave linearly, but it's always nice to have enough data to know for certain.
As for the 15 year old question from Peter above (I got curious), it seems that the 1997 revision of B117 changed it from "Standard Test Method of Salt Spray (Fog) Testing" to "Standard Practice for Operating Salt Spray (Fog) Apparatus" though it probably counts as a lateral move more than a "demotion".
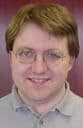
Ray Kremer
Stellar Solutions, Inc.

McHenry, Illinois
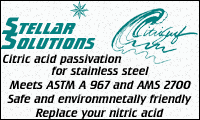
June 12, 2015
Thank you Ray.
I guess that was the question, if anyone had found any correlation to results at X hrs of SS to results at Y hrs. Didn't know if this would be linear even, just curious. Always fun to wait for a 1000 hr SST, especially if you question the results of the test vs. the real world expectations of the product.
Too often we seem to call out requirements without truly understanding the real world correlation, simply calling it out because "we always have" (boiled frog syndrome).
- Osceola, Wisconsin, USA
June 16, 2015
A. Hi Doug. Accelerated corrosion testing is misleading in the first place, as you apparently know. One of the reasons it gives misleading results is that it does not allow for the real mechanisms of corrosion and resistance to corrosion, such as the buildup of adherent corrosion-resisting reaction products on the parts. The best example is probably hot dip galvanizing, which easily outlasts any other finish for steel (75 years without maintenance is not unheard of) because a tight, adherent, relatively impermeable skin of zinc carbonate reaction products forms over the years under good conditions and dramatically slows the zinc dissolution -- but it doesn't happen in accelerated testing.
If we now look at accelerated-accelerated testing and assumed linearity, and we were right, all we would prove is that accelerated testing is even less indicative and reliable than we thought.
But I suppose if we're only talking about adhering to a spec rather than real world performance, corrosion rate might well be linear in a salt spray test, certainly more linear than real-world corrosion where fluffy corrosion products hold moisture to accelerate corrosion and impermeable corrosion products slow it :-)
Luck and Regards,
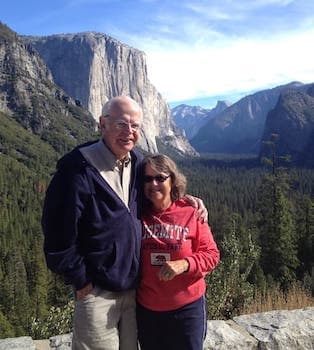
Ted Mooney, P.E. RET
Striving to live Aloha
finishing.com - Pine Beach, New Jersey
June 2015
Q, A, or Comment on THIS thread -or- Start a NEW Thread