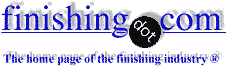
-----
Nickel Chrome Plate temperature thresholds
2006
We are a manufacturer of UV Curing Systems that use extruded aluminum (6063-T5)reflectors with high polish to reflect Ultraviolet Light toward the material to cure Inks and coatings. Recently, we began using a nickel chrome as a highly reflective covering which gave us outstanding results of reflectivity.
The problem we encountered was a bubbling of the chrome surface and ultimately a peeling off of the chrome due to exposure to the high heat of 550 °F. The surface under the chrome was polished to remove impurities and then etched to provide good bond.
Any recommendations for a coating that will either simply a clear coat to protect the polished aluminum from the high heat and Ozone environment or a highly reflective coating that will withstand the harsh environment for years?
Such reflectors are usually bright dipped (or electropolished) and anodized. Often they are dyed gold if they will be used for infrared, but I don't know enough optics to understand the value of the dyeing. I am surprised that you found nickel chrome satisfactory because it far "darker" than people tend to think and absorbs a great deal of the heat rather than reflecting it. Rhodium is a far better reflector.
I don't think it's the temperature that is the problem so much as the substrate. Aluminum requires an immersion zincating process that is always more troublesome adhesion-wise than plating on brass or steel. By the time it gets to 550 degrees these problems are amplified. It may be possible to improve the preplate cycle but that doesn't sound like the easiest way out.
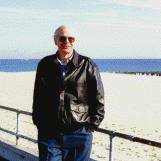
Ted Mooney, P.E.
Striving to live Aloha
finishing.com - Pine Beach, New Jersey
2006
Q, A, or Comment on THIS thread -or- Start a NEW Thread