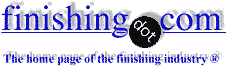
-----
Cure or treatment for tin disease
2003
Hello,
Can anyone tell me please whether there is a cure or treatment for tin disease? We have a number of antique tin vessels which are showing signs of increasing deterioration from this crystalline form of tin. Crystallization always occurs around the edges of existing affected areas, so some form of seeding appears to be involved in the process. We would at least like to know how to inhibit further crystallization. Even better would be to know how to revert affected areas to their original state (e.g. spot-heating?), but that may be wishful thinking. B.t.w., to our knowledge, these items have never been at low temperatures. Certainly for the last 60 years they have been kept at circa 20 °C, and the crystallization is still progressing.
Thanks for your help,
Jules Backer Dirks- Lymington, United Kingdom.
2003
Hi Jules,
You have a difficult problem. It is the subject of an FAQ on this site (see letter 740), but no remedy for 'diseased' tin is offered, only its prevention in new products by alloying.
Pure tin undergoes an allotropic transformation (change of crystal structure) at temperatures below 13.2 C, from white tin (silvery, ductile) to the undesirable gray tin (extremely brittle). An accompanying 27% increase in volume often results in decomposition into powder, hence the name 'tin pesting'ö ('tin plague'ö in medieval times). White tin persists for long periods down to about 0 C, but decomposes almost spontaneously at about -35 C. With continued decrease in temperature, the reaction slows and then stops due to kinetic reasons. The reason you observe the transformation occurring along the edges of existing gray areas is not from seeding, but rather a mechanical effect: it is easier for the volumetric increase to occur at a free surface than in a solid matrix. Unfortunately, the only method reported to return gray powder to white tin requires melting. Your idea of spot heating, e.g., pressing down with a soldering gun, would work except for the fact that the tin oxidized upon powdering and will not rebond. There is also the problem that tin becomes brittle upon heating above ~160 °C (up to the melting point at 232 C).
This transformation is prevented in modern tin casting and plating by alloying with small amounts of antimony or bismuth. Silver or lead also reportedly help. Indium should work since it stabilizes the white tin phase, but I didnöt find evidence in my brief search. Your observation that the 'disease'ö is progressing at 20 °C may indicate the presence of an alloying element or impurity which thermodynamically shifts the phase equilibrium to a higher temperature.
A related phenomenon, the growth of tin whiskers from relatively pure tin plating and lead-free tin solders, is less understood despite extensive government and private research. It has cost billions of dollars in damage to satellites, computers, and other electronic circuitry. NASA Goddard Space Flight Center has collected much of the available information and photos and has experiments in progress (http://nepp.nasa.gov/whisker). Prevention seems to require alloying. For articles already plated with pure tin, a conformal 0.002Ç coating of polyurethane seems to slow the whiskers. A University of Maryland site (http://www.calce.umd.edu) offers Mitigation Strategies for Tin Whiskers which may be useful to circuit designers and platers. Both NASA and TinTechnology.com (formerly the International Tin Research Institute) are collecting data and may be interested in your information.
None of the literature remedies that I found is applicable to repairing historic artifacts. To prevent further progress, short of surgery, I suggest storing at a warmer temperature, say 30 C, and photograph periodically to determine whether that halts the progression. (It would also help to store under a high pressure, but that may not be practical.)
I suggest that you contact museums and historical societies for possible remedies before following my 'surgical'ö suggestions. Surgery for Tin Disease
1) Remove powder phase.
2) Apply a resin-type soldering flux.
3) Fill cavity with a 95% solder.
4) Do any feasible touch-up work.
The following is recommended to improve the stability of the white tin phase via alloying for storage at present temperature.
5) Have items electroplated with 0.0005-0.0010 inch of antimony or silver.
6) Prior to heating in the next step, I suggest that you make a plaster cast of each item in 2 pieces, top and bottom. This is to provide support for the tin during the long heating period, and to be able to make a replica if things go wrong. Let the plaster thoroughly cure, and slowly heat to 100-150 °C to drive out moisture.
7) *Heat part within plaster cast to 100-150 °C. Observe periodically, the objective is to allow the electroplate to diffuse into the tin. A longer time will be necessary at lower temperatures (however, it may lessen tarnishing).
8) Once the electroplated coating is no longer visible (except possibly for a surface oxide).
[start with your least valuable pieces while developing technique, and keep records. You may come up with improvements. It may be a good idea to spray the item with a cooking oil prior to heating in order to prevent tarnishing*.]
Good luck,
Ken Vlach [deceased]- Goleta, California

Rest in peace, Ken. Thank you for your hard work which the finishing world, and we at finishing.com, continue to benefit from.
More Info on Tin Disease An article on the Metallurgy of Organ Pipes by David Smit, State University of New York at Albany, sheds additional light on the causes of Tin Leprosy (Lèpre d'etain). He attributes the breakdown of the metal to "casting on sand, impure alloys (perhaps containing iron or silicon)" and "This condition seems to resemble that where pustules of corrosion form on the surface of the [French organ] pipes and eventually corrode all the way through the material." Elsewhere: "A little aluminum will cause it [he may mean lead/tin alloy] to have severe and continuing grain growth." (www.albany.edu/piporg-l/pipemet.html#analysis)
This supports the idea that certain alloying elements or impurities shift the white/gray tin equilibrium to lower temperature, thereby explaining the observation of tin disease at 20 °C (whereas white tin is stable above 13.2 C if pure). Also, silicon has the same (diamond cubic) crystal structure as gray tin, supporting seeding as a contributing factor (in addition to the mechanical effect of a free surface allowing the volumetric expansion).
- Goleta, California

Rest in peace, Ken. Thank you for your hard work which the finishing world, and we at finishing.com, continue to benefit from.
2003
Ken,
I enjoyed your reply. A good book of info in a short space.
Jon Quirt- Fridley, Minnesota
2003
2003
Thanks Jon,
The first sentence in my last paragraph isn't quite right -- my lame excuse is that my back was hurting so I hit submit when I should have proofread. To clarify:
Badö ingredients (Al, Fe, Si, moisture, sand) increase the relative stability of bad gray tin vs. white tin, causing white tin decomposition even at normally stable temperatures (above 13.2 C). Good ingredients (Ag, Bi, In, Pb, Sb) extend the stability range of white tin to lower temperatures.
It also seems certain that corrosion, especially intergranular, can accelerate the decomposition (by weakening the mechanically-constraining solid metal). Leonardo Perretti, a pipe organ restorer in Italy, states that corrosion (oxidation) of tin due to air pollutants and moisture is often mis-diagnosed as "tin pest" and recommends waxing or storing at < 50% humidity. He considers the corrosion irreversible and mentions the practice of removing the oxide layers and filling with tin or soldering alloy [as suggested above, use a 95% tin solder rather than pure tin]. (http://sul2.stanford.edu/byform/mailing-lists/cdl/2001/0391.html)
Ken Vlach [deceased]- Goleta, California

Rest in peace, Ken. Thank you for your hard work which the finishing world, and we at finishing.com, continue to benefit from.
Dear Ken,
Thanks very much for your most interesting reply to my query regarding tin disease problem. I can see that this problem has taxed many people in the past and that there is no simple cure. The suggestions you make are excellent. Thank you very much. My father's great hobby and love is antiques and also restoring them. I know that he has turned his hand to metal works in the past, and I am sure that he will have the necessary equipment and products to put some of your suggestions into practice. It is such a shame that so many beautiful items from as 'recently' as 200 or 300 years ago have now decided to disintegrate at an alarming rate. I wonder whether, perversely, central heating or some other aspect of modern home environments might not have a role to play in all this. Anyway, thanks very much again for your kind help.
Jan Dam Julus Backer Dirks- Lymington, UK
2003
Re: Tin disease.
Hi Jules,
I stumbled over your mail while surfing Fluoride matters by our uncle Prof. Otto Backer Dirks. You are one strange brother that I am blessed with, strange problems. I Love it. Hope your large collection of antique copper pots are OK. :-) Your bro Charles
Charles Backer Dirks- Barcelona, Spain
2004
Oh my, I have such a strange family.
Tobias Backer Dirks- London, England
2006
August 10, 2008
In 1964 I worked with Northern Electric, Montreal Canada,where in 1965 I started to work on the causes and cures of whisker growth.There was an international patent assigned to Northern Electric. Northern Electric Tin plating process included a post treatment .This post treatment included baking parts in an oven at 375 degrees in a Nitrogen atmosphere for three hours.
This process became a norm at NE for many years with no problem (as far as I know) in soldering component leads or whisker growth. If you can get the patent you will see the logic behind baking.
I thought the readers may be interested in this background, although it may not solve your antique pieces problem. Ash Jafri in my 8th year.
- Richmond Hill, Ontario, Canada
Q, A, or Comment on THIS thread -or- Start a NEW Thread