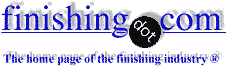
-----
ASTM B117 24 hour salt spray test = 10-15 years in environment?
Q. Is there documented transference rate in regards to: 24 hours salt spray test ASTM B117 is equivalent to 10-15 years for 304 Stainless Steel? Where do I find this information?
Teresa Burnine- Shelbyville, Indiana
2001
A. Unfortunately, there is no correlation because the corrosion mechanism is fundamentally different. Salt spray testing is merely a "screening" test to help indicate that a process has not gone south. It's best used as an ongoing QA test.
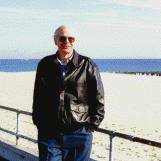
Ted Mooney, P.E.
Striving to live Aloha
finishing.com - Pine Beach, New Jersey
A. I concur with Ted. Should you want a published reference, check out almost any volume of NACE's journal "Corrosion", which often has articles lamenting the lack of good correlation between test data and reality. Yet another is ASTM Cyclic Corrosion Cabinet Testing ⇦[this on Amazon affil links], ASTM STP 1238, 1995. Good luck!

Lee Gearhart
metallurgist - E. Aurora, New York
A. Teresa - If you refer back to ASTM B117, there are several paragraphs which indicate that there is no direct correlation between salt spray and real world performance. New tests are being developed within the automotive industry that provide some correlation to outdoor exposure but they are relatively new and the correlation is still limited.
Cynthia L. Meade- Sylvania, Ohio, USA
A. As everyone else said, that correlation does not exist. Many have tried to come up with better tests, but not a one correlates. GM, Chrysler, and Ford use long 6-month vehicle durability tests and claim that they correlate to real life, but I am still skeptical.
However, you should try and pick a salt spray standard that is in the ballpark. 24 hours to red rust seems a bit weak if you want your part to last 10-15 years. I'd at least expect 150-500 hours if you seriously expect that type of part life. The environment around the part also matters. If the part will see physical damage, heat, water, and/or salt, you may want to beef up your finish and your salt spray requirements.

Tim Neveau
Rochester Hills, Michigan
Multiple threads merged: please forgive chronology errors and repetition 🙂
Q. About your experience: there is same data about resistance to salt spray test hours in real life for example PVD on brass handle is more or less 1500-2000 h .How many years in real life? and zamak, or Iron?
Thank you very much.
locks - Brescia, Italy
2003
A. Hi Stefano,
There is no correlation between salt spray exposure time and real-world corrosion. The purpose of the salt spray test (ASTM B117) is to obtain information about relative corrosion protection.
- Naperville, Illinois
A. To further clarify George's good answer, salt spray testing is primarily for ongoing QA -- to make sure that the process has not gone south, but is continuing to function the way it was designed. The theory being that if a process has been developed that offers acceptable real-world life, while offering X hours of salt spray life, if it stops offering X hours of salt spray life something is probably wrong that will also affect the real-world life.
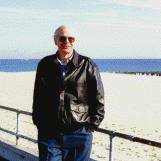
Ted Mooney, P.E.
Striving to live Aloha
finishing.com - Pine Beach, New Jersey
Multiple threads merged: please forgive chronology errors and repetition 🙂
Q. Good Morning !
Please inform me how many actual years reflect a 48, 96 or 192 hours of Salt Spray Test according to ASTM ASTM B117.
Thank you in advance.
Bremer CheziDirector Mechanical R&D - Tel-Aviv, Israel
2004
A. There's no harm in asking, Bremer, but actually this question has been answered here many times before. Salt spray testing is solely a QA measure, used to make sure nothing has gone south in your process, it is not a prediction of real-world life. The only thing that can be said is that if the quality control on a particular finish is improved such that it gets better salt spray life, it will get as good or better life in the real world.
by Gustavo Cragnolino (ASTM)
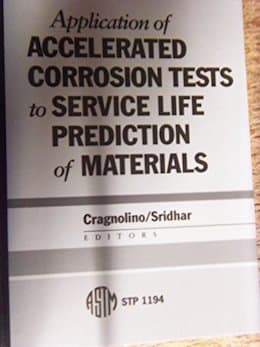
on Amazon or AbeBooks
(affil link)
Corrosion mechanisms are different in an accelerated test cabinet than in real life. For example, finishes that build protective carbonate corrosion products in real life, build none in a salt fog cabinet. So if you were to compare, say, an anodized aluminum finish to an electroless nickel finish to a powder coated finish, to a nickel-chrome finish, to a zinc with chromate finish, it is entirely possible that one of these finishes that lasted only 48 hours in a salt spray cabinet might in the real world easily outlast a different finish that survived 192 hours of salt spray.
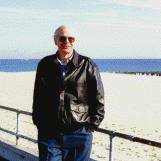
Ted Mooney, P.E.
Striving to live Aloha
finishing.com - Pine Beach, New Jersey
A. There are a few instances where "B117" type test methods result in an inverse correlation with real world exposures. This could lead to a false 'pass' and result in poor selection of materials.
There may be some useful information at
http://autotestreport.com/2000_Articles/0500_engineers.htm ⇩ in the May article by the editor, in which a steel company engineer (Ph.D., PE) relates many problems with salt fog (spray) tests when attempting to predict service life.
To 'prove' a lab test has correlation with real world exposures, there must be the same corrosion mechanisms and the same corrosion products from each, which means that real world exposures must be performed. It is a daunting task, but there are statistical-based Design of Experiment means to reduce the permutations of all variables.
Harold D. Hiltonmaterial testing - Chicago, Illinois
Ed. note: Sorry, that URL is now UTL :-)
[editor appended this entry to this thread which already addresses it in lieu of spawning a duplicative thread]
Q. Performed Salt fog testing on mild steel parts which have been single nickel/chrome plated. They have performed very well in Salt fog setup to ASTM B117 standards but customer needs to understand how these salt fog hours [in this case 200] translate to his products life in the field in years of service. Is there any information I can reference or website with some good information on this?
Customer - Wheeling, Illinois
June 2, 2009
Q, A, or Comment on THIS thread -or- Start a NEW Thread