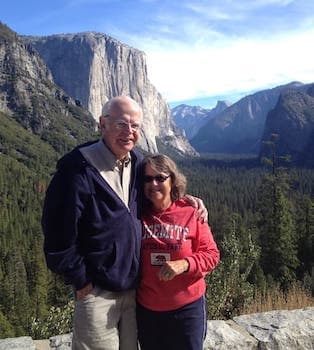
Sound technical content, curated with aloha by
Ted Mooney, P.E. RET
Pine Beach, NJ
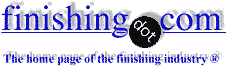
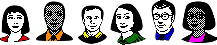
The authoritative public forum
for Metal Finishing since 1989
-----
Protecting Space Frames against internal corrosion. Lotus Super Seven
Most recent answer:
A. I realize that this is quite an old post, but having just finished braze welding some brackets on a Lotus Seven (18 gauge mild steel) using 66,712 psi silicon bronze rod, the rod should be stronger than the steel I have used it on. Most bronze welding if done properly, should be stronger than the material being joined. Bronze welding should not be performed on 4130 however, as it opens up the surface of the metal causing stress cracks. Nickel bronze rod can be as high as 80,000 psi strength.
I found some rusty looking metal filings inside my originally fully sealed space frame prior to drilling the frame and installing some necessary plain bushings. The frame had been fully sealed many years ago after construction in the U.K., has remained sealed as a spare until now, and is powder coated on the outside. The rusty filings must have remained inside sealed from outside air - only retaining the moist? English air inside the tubes after completion. I fished out most of the rusty looking filings with a magnetic end on a flexible 'fish' wire.
An aircraft welder friend of mine swore by LPS-3 frame tube treatment. He worked on tubular airframe structures, would drill a 1/8" hole in which to spray the LPS-3, then plug the hole with a monel metal closed end rivet treated with an epoxy? coating to prevent any leakage. I would suggest that LPS-3 or similar wax type treatment (Eastwood product?) would be suitable. As any older model of Lotus had alloy bodywork attached by numerous monel metal rivets (used to avoid galvanic corrosion between the dissimilar metals), use of a wax type medium sprayed in the holes would be advisable. If the chassis is already clad in alloy, carefully drill out rivets at either end, and spray the wax solution inside. Hopefully it will make its way along the tubes if you can't help it along the way by raising the front and the back of the car sufficiently to allow the solution to flow. The only way to get full coverage of course is to rotate the chassis (Lotus Seven bare chassis with ally bodywork weighs approx. 50 to 90 lbs. depending on the model and if it has added metal for strengthening). Hope this helps for future Seven owners. EW
Ed Wills- Calgary Alberta
September 26, 2020
⇩ Related postings, oldest first ⇩
2001
Q. Dear finishing.com,
Question: What (modern application) might work best for the home builder or small shop in the way of corrosion protection for the inside of a complex maze of small steel tubes all welded together?
Background:
I have been curious about corrosion problems related to the inside of tube space frames for years. These frames are typically made of one inch square mild steel (1.6 mm thickness) and are used in hand built cars like the Lotus Super Seven. If you picture a rectangle approximately 2 foot by 4 foot by 8 foot, with considerable cross bracing, you'd have a fair idea of its construction.
Persons constructing these frames are usually careful to omit any butt welds thinking that these areas will become water traps and accelerate corrosion problems internally. Another typical aspect of a space frame's construction is the attachment of aluminum panels on the sides and bottom via rivets to form a more rigid structure. Builders often apply various compounds to seal the rivets believing that this might reduce corrosion problems.
Some of these frames fail in as little as 3 years due to internal corrosion, others have performed well for more than twenty years. Some are brazed, some are MIG welded, some are treated with various waxes, fish oils, boiled linseed oil ⇦this on eBay or Amazon [affil links] and who knows what. Adding to all these variables, the environmental conditions, climates and such are still more factors which make it difficult for the laymen to figure what causes or prevents a rapid failure.
Builders would gladly insert threaded plugs top and bottom to allow agents to be poured in and sloshed About where the frame could be turned every which way to assure all areas are coated. Folks have even suggested stringing a wire through the inside of the tubes with conductive breaks to be used as the Anode? in an attempt to plate the inside of the tubes, but I have no idea if this has been done or is even Possible.
One additional factor for consideration , a number of builders suspect that the heating and cooling of this structure (created by operating the car) will bring in moisture via any crack or hole in the frame. This action could suck in moist air where it would condense during the next cycle of operation. For this reason, some profess that a frame with OPEN drain holes at the bottom would last longer. I would certainly like to hear what others think of this as well, should a builder attempt to seal the structure or leave it open?
Thanks in advance for any help or advice.
George Breckenridge- Seattle, Washington
A. Hi George!
My background is plastics, not plating, but the Lotus Super Seven, in my youth, was always a dream which could never be attained.
Due to the complexity of the rigid tubular chassis structure, I go along with what you said about pouring in a suitable 'liquid' and ensuring full penetration.
The idea of a bottom located drain hole or holes makes real sense. 1/8" dia. should be OK. Heck, if you do this to rear mufflers (earlier Volvos were very prone to premature failure of the back mufflers due to condensation) you will increase the life.
May I suggest you use a real heavy oil, SAE 80 or so BUT heat it up nice & very hot before applying. This should give you a nice thick coating versus, say, SAE 30 or 40.
You mentioned that some people braze these frames. Really! That I wouldn't like ... and doesn't the sports car Assoc. (in Canada it's the CSA) spec that brazing for roll bars is strictly verboten and that they must be welded?
Re aluminum attachments (fenders etc) via pop rivets, I'm not really qualified to give a sensible answer, maybe a small 'washer' of 1/16" thick Polyethylene between the frame and the aluminum before pop riveting to reduce the chance of corrosion ... using steel not aluminum rivets, s.v.p.
Lots of luck. Drive slowly like I always do (?).
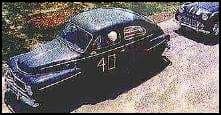
Freeman Newton [deceased]
(It is our sad duty to advise that Freeman passed away
April 21, 2012. R.I.P. old friend).
A. Hello George,
Are you sure that corrosion is the reason that the frames fail? Stress can encourage corrosion, and corrosion can encourage cracking. But if the stress were less then the corrosion may not be a problem. With all the rivet holes you speak of it is likely that damp air can get inside the frame, but then when the frames hot or warm the moisture should be driven out too. You could brush plate zinc on the outside of the frame, as a sacrificial protection, and but aluminium is sacrificial to steel also, so the riveted on aluminium plates should, already, be helping there. The little spaces between the riveted on plates and the frame will be good places for corrosion to take place, try and avoid them or seal them at least. I'm sure you can plate the inside of the frame, using some ingenuity, maybe carbon rods (with spacers) placed inside the steel tubes before joining the tubes (the rods wired together too), then when the frames made pure in electrolyte and power it up. It doesn't sound too practical though, and if your then gonna drill lots of holes in it it does make much sense either.
Really the only thing to do is design it as well as you can, build it as best as you can. Remember not all steel or mild steel is the same, there are variations within grades (from manufacturer to manufacturer). Then if you want it plated (zinc or tin/zinc) take it to a professional. They'll do a better job, and know about the safety issues and deal with some chemicals you don't want to play with (i.e. chromates - plating just aunt the same without 'em). Then paint it as you like, or get a professional to do that too. Then take it home and park it in a nice dry garage.
I hope I've been some help, in a vague and general way.
Ian Brookeuniversity - Glasgow, Scotland
2001
Hi Freeman,
Just a quick note to say that there has been a great deal of study regarding brazing and welding. Many space frames have been examined after damage. Seldom if ever does a break occur in a brazed joint. Metal seems to rip and pull apart adjacent to the brazed joint or somewhere away from the joint. Folks who know more about this than I claim that the application of brazing material forms an alloy that is much stronger than the brass based alloy applied.
It appears that welding lowers the cost of building the frame and produces higher heats in a more localized area around the weld. It is said that brazing is done with lower temperatures, but this heat travels further down the tubing creating warpage and making it more difficult to produce a truly straight frame. Others suggest that the high heat created by welding makes the metal more porous and more prone to rapid corrosion.
George Breckenridge- Kent, Washington
2001
Hi George,
I was flabbergasted to 'hear' that brazing is stronger than welding (of steel) ... I canna believe it! A brass, copper zinc (or wotever) alloy is STRONGER than steel! I strongly suggest you check with NASCAR!
Ian was right and I was wrong. Aluminum is (slightly) lower on the galvanic table than iron. And what he says about checking out the 'various' steel tubings makes sense. Some will stronger than others (undergoing perhaps more cold drawing) but that means most likely that they have more stresses which could prematurely show up after welding.
Yes, definitely go to NASCAR! Maybe they use ultra high tensile cold rolled/drawn tubing BUT (and I'm guessing) perhaps they use collars (sic. sockets) which one brazes onto. The theory being, perhaps, that the lower brazing temperature will not disturb the lattice structure of the steel as much and, because of the sockets, there is a nice 'length' of a more flexible 'weld',ie. brass (something like copper pipe fittings).
Then there's stress corrosion ... so you must get some good advice on the Quality and the thickness of the tubing you want to use. My suggestion of 1/16" Pe washers between the aluminum was to retard/prevent corrosion. The 'washer' could be made of a narrow strip of A thin plastic material taped to the frame. Then you could pop rivet to your heart's content. Use nylon if you wanted to (much, much harder and takes more heat) but HdPe is good to around 150° F continuous.
The advice of keeping the machine in a nice, dry garage makes sense ... especially if you want to keep it for many years.
I sure would like to hear what the metallurgists at NASCAR say ... or contact one of the racing teams and ask them but they'll possibly say Titanium!
Yes, I know it's all about the HP/WEIGHT ratio but I'd rather add a few pounds to play safe.
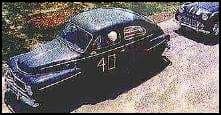
Freeman Newton [deceased]
(It is our sad duty to advise that Freeman passed away
April 21, 2012. R.I.P. old friend).
Hi Freeman,
When I look at an outfit like NASCAR, I try to evaluate their focus. Do they care whether a frame lives longer than it's short life on the track? Probably not. Furthermore, and based on my limited exposure to their cars, they seem to use thicker, heavier, materials, with far fewer elements.
I don't think there's too many people or entities that care how long a structure like a space will live. Even with no protection, they hold up long enough to sell, and then it becomes the owners problem.
I have received a number of good tips, and I appreciate them all.
Thanks,
George Breckenridge- Seattle, Washington
2001
2002
A. Hello Everyone.
Let me get this disclaimer out in front. I am not a plating guru. However I work for a company that has a large plating and wastewater operation. So I Have gotten a bit of a crash course.
As for your space frame or any other steel structure in which you want to prevent internal corrosion. My personal favorite is expanding foam. But you must use a good dense closed cell foam. The trick is to drill or find a hole in the particular tube you are filling near the end which is a snug fit for your applicator tube. There must be a way to vent the pressure at the other end. Considering your frame has already been poked full of holes and pop rivets. All you would have to do would be drill one out at each end of a tube fill from one end and then plug that hole with a pop rivet. Clean up the mess that comes out of the other end with the appropriate solvent. (do this before it hardens or you will be all day trying to clean it off) Then plug the second hole. Assuming that the metal is in decent shape and the rivets are holding on tight, the foam will expand to the full volume of the tube and force its way out any cracks or into the next tube it if wasn't a but weld.
If you have already checked and the hole space frame is constructed of open welds. Then someone could conceivably start filling from the lowest point on the frame with several rivets drilled out and have an assistant run around with a can of solvent and a rivet gun to reseal the holes as the foam climbs past them. But you would have to do it in a fairly short period of time. In other words be sure you have all the foam you will need before you start filling. My personal favorite is the stuff you find in aerosol cans at Wal-mart or hardware stores. It is more expensive by volume but you don't have to worry with mixing it properly and having it harden before you can get it where you need it.
I use it for sound deadening and rust prevention (and repair) in lower fenders of automobiles. (anyplace that will not need to drain)
Don't ever use in a enclosed area composed of thin material (i.e. sheet metal) that doesn't have enough space or vents for the pressurized foam can escape or else you will end up with a deformed panel.
I personally have a Plymouth Fury that was starting to rust in the rear quarters because of a sloppy weld. About ten years ago when a friend who worked at a body shop told me to try the foam. It worked perfectly. More recently I have filled just about any void in the body and frame that can be safely filled with it. (except the doors which of course need to drain) You can only hear the wind noise that comes through the glass. And there is no way for moisture to get in where it can cause corrosion. So far it has only added about 25 lbs (around 11.3 kg) to the total weight and has been a major improvement to the vehicle.
How does this relate to plating? I'm not sure but if you are having problems with internal corrosion in your plating shop it would be worth a try.
Bryan Denton- Lawrenceburg, Kentucky, USA
2002
Bryan,
That's not a bad idea for George to try out.
My only input is that you should check with the foam supplier about the density. I believe you may find that the foam, normally a Polyurethane, comes in different densities and perhaps a 4 lb density maybe the answer. Your local fiberglass supply house should be able to help you. (4 lb means that once foamed, it will weigh 4 lbs/cu.ft).
The only other thing is due to the very small diameter of the space tubes, may I suggest you get a 'scrap' piece and try to find out how FAR down the foam will travel after being injected through one of the 'holes'. What Bryan said about 'holes' is right on. You may need a number of these to ensure that the foam goes all the way down.
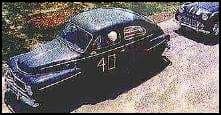
Freeman Newton [deceased]
(It is our sad duty to advise that Freeman passed away
April 21, 2012. R.I.P. old friend).
February 2, 2009
A. Years ago, Porsche built the space frames of at least some of their 917s of tubular aluminum. The state of the aluminum fabrication art was not so advanced - so cracking was a very real worry.
In order to allow for easy crack detection they would pressurize the inside of the tubular structure via a simple tire valve fitting - as long as pressure "held" all was well. Any loss of pressure indicated a crack - and finding the crack required only soap bubbles! Clever, yes?
Of course, upon initial construction of the frame, one would provide for the interconnection of all the tubes using a drilled connection at welded tube intersections as well as a high level of welding precision. Any structure that reliably holds pressure can be viewed in good confidence.
Internal corrosion of such a structure would be easily prevented by eliminating oxygen & moisture inside the tubes by simply evacuating the structure using a vacuum pump, (to 500 microns or so, holding for 30 minutes), and providing a mild positive pressure,(5 - 10 psi - no more), using DRY nitrogen.
No oxygen & no moisture equals no corrosion, EVER!
If one added a pressure gauge permanently piped into the tubular structure, you would have an clever & reliable corrosion prevention & crack detection system. One which weighs nearly nothing - costs almost nothing - with maximal reliability.
Just a thought....
Regarding attaching aluminum (or other) panels to tubular frames:
Wherever practical, one should avoid drilling rivet holes into the closed tube frame members - no matter how carefully installed, over time, the rivets will leak and allow ingress of atmosphere & moisture.
Filling the tubes with structural foam has much to recommend it, the foam can provide considerable buckling resistance - future frame repairs requiring welding could be more complicated, however.
Why not avoid the holes for rivets all together? During the fabrication phase weld on tabs and riveting strips at appropriate locations. A bit more weight,(and work), in return for "no worries".
When installing the chassis skins generally, consider using one of the good STRUCTURAL adhesives ⇨
to bond the panels to appropriate chassis tubes.
These adhesives are easily strong enough to absorb considerable structural loads over wide areas with few point loads.
This practice greatly reduces,(or eliminates), rattles & drafts - not to mention the stress risers that often lead to cracks between rivet holes in the skin panels.
Over a surprisingly short time, nearly all riveted structures "loosen up" and become much less stiff. Structural adhesives could go a long way towards eliminating this fault; a MUCH improved assembly.
Be forewarned: Aluminum adhesive bonding, (as well as welding), is much less reliable than with steel for the amateur and professional alike.
With steel panels, the constructor could forego many additional rivet tabs & etc. Structural adhesives could STILL be used with well designed spot welds REPLACING all those silly rivets.
Good rivets, after all, are EXPENSIVE and they do weigh something..more than you may think!
A full weight analysis would most likely show weight REDUCTION with this steel panel alternative! Any weight GAIN can be addressed with detailed design.
In any case, a steel panel alternative will almost certainly result in a stiffer, stronger & cheaper structure. It will likely have a much longer service life as well.
STEEL - may not be as "sexy" as aluminum - but very often it is a better choice for the "home based" craftsman.
With steel instead of aluminum skins, you will lose the ability to polish it. To get the "polished aluminum" look
-check out the various films used for vehicle wrapping.
- Charlotte, No. Carolina
Q, A, or Comment on THIS thread -or- Start a NEW Thread