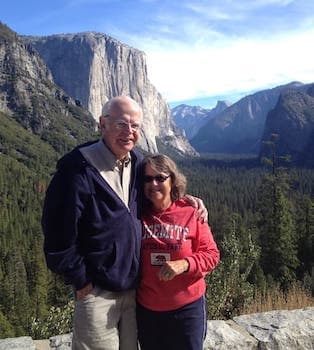
Curated with aloha by
Ted Mooney, P.E. RET
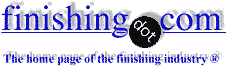
The authoritative public forum
for Metal Finishing 1989-2025
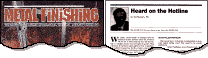
-----
Hot black oxide (blackodize) vs. cold blackening
Q. I work in a tool room as an apprentice and would like a comparison of durability between black oxide done with the cold method and the hot method. Thank you very much.
Thomas M. Herpel1997
A. Room temperature blackening with proprietary solutions is more expensive and less durable, Thomas, and doesn't look as good. Whether it will prove "durable enough" would depend on the application, but the cold blackening processes that I know of deposit selenium compounds on the surface, which do tend to rub off as a smut. Hot black oxiding is a nasty, dangerous, process though. So, if the durability of room temperature blackening is sufficient for you, and the cost is affordable, it may be worthwhile :-)
You may be interested in our FAQ on Black Oxide & Cold Blackening, and further info can be found in The Metal Finishing Guidebook. Best of luck!
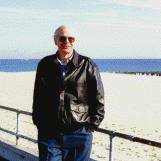
Ted Mooney, P.E.
Striving to live Aloha
finishing.com - Pine Beach, New Jersey
1997
A. Tom,
Ditto on what Ted said. A well done hot process looks a lot better and my gut feeling is that it is ten times as durable as a well done cold process. The cold process is adequate for most of the tool room uses. Have done both and unless you absolutely need the better protection of hot, use the cold. Hot is going to cause you some problem with EPA more so than the cold. Personal feelings.
James Watts- Navarre, Florida
1997
Q. I'm very interested in the cold process for auto parts for personal use and want to find a local dealer for the chemicals. However I have the background to set up a small garage based unit for local hot rodders. Any help will be appreciated.
John g. [last name deleted for privacy by Editor]1998
----
Ed. note: You can try EPI / Electrochemical Products Inc. [a finishing.com supporting advertiser] for cold blackening processes; they are well known for them.
A. If you do, that will make you a Hazardous waste generator. Suggest that you check with your region of the state EPA and with your local sewer folks before you go any further. You probably will change your mind. Minimum fine is substantial if you are caught. If an angry customer turns you in, they will visit you to clear the complaint.
James Watts- Navarre, Florida
1998
Response to John G. If you really have the proper background to install a mini plating shop in your garage, then you should know you will be exposing children, pets and neighbors to dangerous chemicals. You should also be aware that you will have chemicals and waste water to dispose of, and that you need a city permit, a state permit and EPA clearance to do all of this.
Are you prepared to put in a separate sewer line, pay the business fees and license fees to all the proper agencies, or take the livelihood from an honest, reputable plating shop that does all these things.
Lee Garcia- Reno, Nevada
2003
Multiple threads merged: please forgive chronology errors and repetition 🙂
Q. I would like to know about:
1. Room Temperature Blacking Method of Iron and Steel.
2. What are the Advantages and Dis advantages compared to Hot Blackening/Oxidization process.
3. Which web sites I can visit to know more about the process and the various manufacturers.
- Calcutta, India
1999
sometimes on
AbeBooks or Amazon
(affil links)
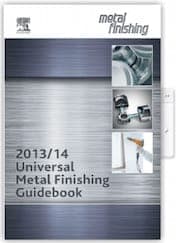
free pdf is currently available from academia.edu
A. The principal advantage of cold blackening is that it is far safer to operate than the hot process, which involves a boiling hot highly concentrated aqueous solution of caustic soda ⇦liquid caustic soda in bulk on Amazon [affil link] which, if not handled properly, can erupt and burn or kill people. The operating temperature of hot black oxide tanks is much higher than the boiling point of water, such that when water is added to make good the evaporation losses, it has the potential of instantly flashing to steam and blowing the contents of the tank all over the place.
Cold blacking chemicals are more expensive, do not have equivalent corrosion resistance or the shiny uniform appearance of hot black oxide, and can rub off as an abrasive grit which can be a problem in certain manufacturing processes.
We have a FAQ on Black Oxide & Cold Blackening which may be helpful, and if you can find a copy of the Metal Finishing Guidebook, it will have a chapter on the subject. Good luck.
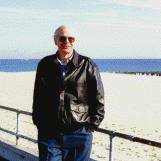
Ted Mooney, P.E.
Striving to live Aloha
finishing.com - Pine Beach, New Jersey
1999
Q. James,
Which process would make me more of a hazardous waste generator, the hot method or the cold? Do you know of any documentation comparing the waste concerns of both methods?
Bob P.- Toronto, Ontario, Canada
2001
![]() |
- Atlanta, Georgia 2003
It is one thing to use chemicals as a hobby and collect the waste rather than sending it to the sewer. But if you sell metal finishing services as John G proposes, you are operating a plating business, so please glance through EPA40CFR, especially the subheadings on waste water, sludge accumulation records, nitrate documentation, and air emissions estimating; or attend a hazmat course offered by AESF, or Lion Technologies, or your local community college. Go to the library and read a couple of issues of Plating and Surface Finishing, Metal Finishing, or "Products Finishing", or attend the annual plating industry/EPA meeting in Washington DC. Then try to explain to yourself on what grounds you could possibly think that a metal finishing business could possibly become exempt from those regulations. You ask what good is this forum if it doesn't encourage amateurs to go into the plating business? Well, what good is a police force if they don't serve me breakfast in bed? What good is an air conditioner if I can't barbecue a steak on it? This forum is directed both towards professionals & their shop problems, and amateurs & their metal finishing questions -- but it is not directed at tempting people to injure themselves, to violate laws, or to jeopardize the public safety. ![]() Ted Mooney, P.E. Striving to live Aloha finishing.com - Pine Beach, New Jersey 2003 2004 Curiosity has me in it's grip today. I do gunsmithing once in a while. So far, sending parts out hasn't been too tough, but I'd like to add to my in-shop abilities. Some things MIGHT be better if I had some control over them myself. Getting parts back plated too thick, or not masked properly... I found, well, Ted's response a bit presumptuous, and rather inflammatory. Ya, it was a flame...but a semi-informative one. Listed a few areas for me to look into... Being interested in the plating/finishing processes, I'd like to know more about the laws involved, and what needs to be done to actually DO some plating/finishing on my own once in a while. Truth be told, it's MY judgment call as to what will be "too expensive" to justify it. Likewise with the legal research. It's MY responsibility to ensure I conform with law, specifically those that would apply to ME: MY application, quantities, location, whether to hire a lawyer to find all of this out, etc... Case in point: Some businesses ARE EXEMPT from OSHA. Law is not always the same, it's up to the individual to make sure they comply to whatever laws applicable. Real Estate businesses are exempt from OSHA, BTW...Supposedly not enough injuries per year to justify inspecting them...Hmph... Anyhow, rather than blow someone off with a flame, next time do it with some finesse. Information shared responsibly, AND IN A MANNER THAT IS USEFUL, is worth a lot more than some cheap shot at the auto parts plating guy. Enough to think about. Take Care, - Berthold, North Dakota
2004
James Watts and Lee Garcia warned the initial writers that there are EPA problems involved in operating a shop with this kind of chemical processing. To that, Mr. Horan responded by saying they 'make way too big a deal' of it and were 'throwing a bunch of legal mumbo jumbo' at people. He implied that our website is worthless because it doesn't serve the purpose he wishes. He closed by saying that our motive for the long years we've put into this site was to keep things "secret" so we could "make more money" by discouraging people from the business. You did not see those repeated, provocative, personal insults as a flame! I gave the volume number of the code of federal regulations that people should look at, and which subheadings to look under. I gave three places where people could get training on the actual laws. I named the principal journals serving the industry if anyone wanted to learn more. I named the location of the annual conference where EPA keeps metal finishers advised of those regulations. And you considered this as 'blowing him off', not sharing information in a 'manner that is useful', and flaming :-) Amateurs often react petulantly when they find that plating isn't as easy and unregulated as they hoped. Oh well :-) EPA 40CFR413 and 40CFR433 make no exception for the size of a business. However, if someone is processing parts only for personal use and they neither sell a finished part nor their processing services, so that they can honestly say they are not in business, it is very probably true that these federal regulations do not apply to them. However, there may still be state & local laws, sewer regulations, and community "right to know" laws that may be violated by that chemical processing. That, as you say, depends on the situation. ![]() Ted Mooney, P.E. Striving to live Aloha finishing.com - Pine Beach, New Jersey |
Multiple threads merged: please forgive chronology errors and repetition 🙂
Q. Does anyone know if you can successfully chemi black EN31 Carbon Steel?
Louise BoyleProduction engineer - Glos, UK
2007
2007
A. EN 31 = DIN 100Cr6 = SAE 52100. A high carbon, high chrome steel with high hardness and wear resistance. Commonly quenched & tempered to HRC 62. Composition is
C 0.98-1.1, Cr 1.30-1.60, Mn 0.25-0.45, P 0.025 max, S 0.025 max, Si 0.15-0.30, bal Fe.
It likely can be blackened by either the conventional hot black oxide or room temperature chemical processes. I haven't any experience treating this alloy. Due to the levels of C & Cr, it is perhaps treated as a 400-series stainless steel. Anyone with more info?
Chemical suppliers may be able to refer you to local jobshops having the appropriate treatment solutions.
- Goleta, California

Rest in peace, Ken. Thank you for your hard work which the finishing world, and we at finishing.com, continue to benefit from.
The EN31 (400) series material can be treated with low temperature chemi-black systems that operates at ambient temperature.
Barry Clements- Coventry Warks, UK
2007
2007
Q. For your info -
I run a small 3-man engineering shop and use a proprietary supplier to supply me with cold blackening chemicals.
For a shop as small as mine, the process is probably a little expensive, but the benefit is being in control of your product from start to finish, controlling your own lead time on job completion, etc.
In my experience it is correct to say, though, that hot black oxide processes are much better quality.
As my company expands I am now looking into the hot process.
What process is used for cleaning the part before hot blackening?
When I cold blacken I first have to sandblast the part if it has any mill scale left, unless it has been machined, then it can go directly through the cleaning agents provided by the supplier.
What is the process with hot blackening?
- Goulburn, NSW, Australia
A. Those steps will be the same, Ben. Scale must be removed, then the parts thoroughly alkaline cleaned before putting them in the hot black oxide tank. Usually there will be a post-dip involving a wax or oil.
The biggest difference is that hot black oxide is quite dangerous. The problem is that the process operates at about 290 °F so there are evaporation losses, and water must be constantly added. But water flashes to steam at 212 °F. So, if a good slug of make-up water finds itself surrounded by this 290 ° solution, it can flash to steam, propelling this hot concentrated caustic onto an operator. Some people have been killed and many severely burned from these eruptions, so extreme care must be used to prevent it from happening, and protective gear worn in case it happens anyway. Good luck!
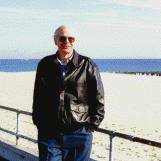
Ted Mooney, P.E.
Striving to live Aloha
finishing.com - Pine Beach, New Jersey
2007
Multiple threads merged: please forgive chronology errors and repetition 🙂
Q. If properly rinsed after the black oxide bath, should a hot-process black oxide leave smut residue when handled?
Parts I am receiving from a supplier leave a black, greasy substance, and since the parts will be handled by a customer, I'd like to minimize this. It seems to be after finished in oil. Rinsing in isopropyl alcohol removes most of the smut but also some of the finish.
Thanks,
Jimmy
- Austin, Texas
February 4, 2008
February 23, 2009
A. Hi, Jimmy. You can have a different oil applied that is less smutty, or a wax instead. But a black oxide finish derives almost all of its limited corrosion resistance from the oil or wax. If you remove it, it will flash rust.
Regards,
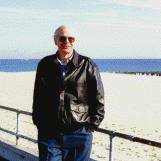
Ted Mooney, P.E.
Striving to live Aloha
finishing.com - Pine Beach, New Jersey
![]() |
Q. I'm working for someone who is interested in possibly starting a hot black oxide business and I noticed that someone said that a permit was required for plating, but I wasn't sure if that applied for a black oxide finishing company. From what I've read, finishing and plating are different so I was wondering if the law requirements were the same. Kirsten Haney- Acton California United States May 19, 2008 A. Hi, Kirsten. I do not see black oxide mentioned in EPA 40 CFR 433 (see www.access.gpo.gov/nara/cfr/waisidx_98/40cfr433_98.html), so I would say it's possible that an EPA permit may not be required. But you should check with a local field office of the EPA, or with your POTW. Good luck. Regards, ![]() Ted Mooney, P.E. Striving to live Aloha finishing.com - Pine Beach, New Jersey May , 2008
- Bangalore,Karnataka, India October 22, 2008 ---- September 3, 2012 OK, Robert and Ted, - Louisville, Kentucky |
A. Hi Tom.
My understanding is that all cold blackening processes rely on a deposit of a selenium sulfide compound on the steel, not an actual black oxide. My limited personal experience is that even the best of these are "smutty" (rub off fairly easily, leaving hands or cloth dark). Hot black oxide is, in my opinion, a nicer looking and superior finish. But the high temperature does present the safety issue I mentioned.
In one case that I know of, someone tossed an unopened can of soda to a co-worker, but it missed and landed in a black oxide tank where it flashed to steam then exploded that hot caustic onto the operator, killing him. Everyone treats a pot of boiling water with respect, and these tanks are much bigger, much hotter, and filled with concentrated caustic rather than water. So face shield ⇦ this on eBay or Amazon [affil links] , apron ⇦ this on eBay or Amazon [affil links] , gloves, and boots is not at all excessive in my opinion ... and they would be a requirement if I were the supervisor. Good luck.
Regards,
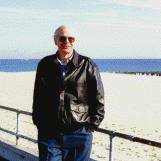
Ted Mooney, P.E.
Striving to live Aloha
finishing.com - Pine Beach, New Jersey
September 3, 2012
Q. What is the modern cold bluing now?
Today what is the better way to do the modern cold bluing or the traditional bluing?
Someone help me to answer my question please.
- dubai, uae
May 4, 2015
A. Hi Kabz. Both are widely done because there is no such thing as "better way" ... it all depends on which parameters are most important to you. However, there is little question that hot black oxiding produces a nicer looking and more corrosion resistant finish. As you see, we appended your question to a thread which already addresses it. Good luck!
Regards,
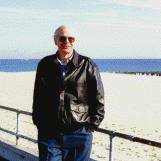
Ted Mooney, P.E.
Striving to live Aloha
finishing.com - Pine Beach, New Jersey
May 2015
Q. Hi Ted,
Thanks for giving me an idea.
Can I ask more questions: I'm working now in a government company and I don't have any idea what's the better process. I will do the hot bluing or the spray-on, bake-on finish process? and I don't have also the idea of the man-hours of both processes because this is my first time I will do this kind of work. And we're planning a small arm and a big arm that will undergo bluing or coating. Can you give some advice what's good to do, where the man-hours also are short and can produce more finished products.
Thank you so much.
Regards, ave
- dubai,uae
May 8, 2015
A. Hi again Kabz. The reason so many different finishes are available is because none of them is all-around superior to the others. Manufacturers with decades of experience have difficulty choosing, but Step 1 is to have sample parts finished and tested before you consider building a factory to mass produce a possible mistake.
Still, here's one thing for you to consider: bluing, even hot bluing, doesn't offer much corrosion resistance. It's a beautiful finish for those who will lovingly maintain their favorite hunting weapon, cleaning and oiling it after each outing. But as a robust finish for mass produced and mass distributed arms? ... I don't think so. The spray-on and bake coating sounds more applicable. But there are many other choices including electroless nickel plating and salt bath nitriding.
As for man-hours, I think you would need to hire a consultant to work through all of the issues with you. Estimating the man-hours involved in a whole manufacturing and inspection sequence is a very big job. I am personally not interested in cheapening stuff anyway. I'm for sustainability, whereas perpetually re-manufacturing stuff that doesn't last due to cheap, poor finishes represents wastefulness that the planet can't afford :-)
Regards and good luck,
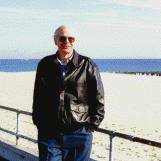
Ted Mooney, P.E.
Striving to live Aloha
finishing.com - Pine Beach, New Jersey
May 2015
August 16, 2015
Q. Dear sir,
I am planning to start BLACKENING process in our company only. Can you suggest what and all need and how to start new process sir?
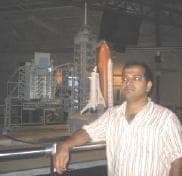
Hemant Kumar
- Florida, USA
Q. Dear All,
Could you please help to make a continuous cold blacking or cold bluing for uncoated steel strip to get high corrosion resistance with blackening? Please help to apply a thin coating (1 micron max) on steel strip with an acceptable opacity and good coverage.
Line speed around 60 m/mint.
Regards,
steel - Cairo, Egypt
November 19, 2015
Hi Hemanth; Hi Salah.
People are very welcome to try to help you, but it looks like they're not doing so this time :-)
This forum is good for directing people to sources of information, which I did in my first response on this page, and the forum is also good for specific answers to highly specific queries. But it's probably unrealistic to hope that a reader will design a process line for you for free via this forum. Good luck, but after reviewing the recommended resources, please try to ask highly specific questions. Thanks.
Regards,
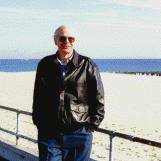
Ted Mooney, P.E.
Striving to live Aloha
finishing.com - Pine Beach, New Jersey
Want cold blackening with shades of gray
Q. I haven't found anyone in Brazil who has experience with black oxide for architectural purposes so I have been researching your site and working with a small metal shop in order to try to create cold blackened steel panels to cover a large kitchen wall. We are getting close using the selenium copper compound however our results still don't have that beautiful dark grey finish with lighter and darker variations. We are using 20% copper to 80% selenium on 1/8" steel sheets and leave it approximately 20 seconds. The result is either totally black, if left too long, or it has a reddish-orange tint. Any suggestions how we can achieve the desired coloring?
Mitchell TremskyArchitect - Rio de Janeiro, Brazil
January 24, 2016
A. Hi Mitchell. That sounds like an interesting finish! Unfortunately I'm not personally familiar with it, and the only cold blackening that I know is actually black. You can try contacting EPI / Electrochemical Products Inc. [a finishing.com supporting advertiser], who specialize in cold blackening, or hopefully a reader will be familiar with your need.
Regards,
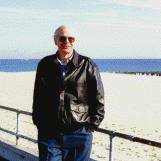
Ted Mooney, P.E.
Striving to live Aloha
finishing.com - Pine Beach, New Jersey
January 2016
Multiple threads merged: please forgive chronology errors and repetition 🙂
Black oxide counter top
Q. I am investigating blackened steel kitchen bench top. Concerns from reading above would be reliance on a seal for corrosion prevention. Given only kitchen bench would a non sealed work. I got the impression blackening was done in first instance to stop corrosion.
Thanks in advance.
- Christchurch, New Zealand
February 22, 2016
February 2016
A. Hi Darin. Try a small and simple one first and let us know how it works out because I have no experience with it. A "dry" hot black oxide would probably be highly subject to rusting, but if you keep it waxed with butcher's wax or oiled with mineral oil, my guess is that it will be okay. Remember that petroleum oils (which would be the most commonly applied oils) are poisonous!
Regards,
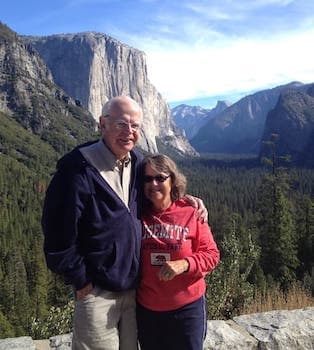
Ted Mooney, P.E. RET
Striving to live Aloha
finishing.com - Pine Beach, New Jersey
Cold blackening toxicity?
January 28, 2017Q. I'm looking at black oxide treatments for shop-made tooling--clamps, step blocks, boring bar adapters, that sort of thing. Typical materials are 1018 and 12L14 cold rolled steel, maybe some O-1, D-2, or S-7 tool steels on occasion.
The actual black oxide processes, even the ones at lower temperatures (220 vs 290) are wickedly dangerous due to the caustic sodium hydroxide, flash-over, etc.
Hence I'm looking at the cold black options. If I understand it correctly, these put a copper/selenium coating on the steel My concern with them is the selenium content. Selenium and its compounds are very toxic, with an LD50 on the order of 1-3 mg/kg body weight.
How safe is it to handle parts with a cold black treatment on a regular basis?
hobbyist - Renton, Washington, US
Ed. note: This RFQ is outdated, but technical replies are welcome, and readers are encouraged to post their own RFQs. But no public commercial suggestions please ( huh? why?).
January 2017
A. Hi Paul. These are proprietary processes, so I think the suppliers' material safety data sheet may offer good info.
Regards,
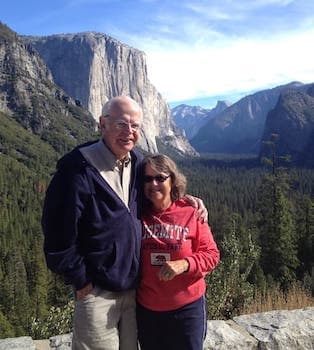
Ted Mooney, P.E. RET
Striving to live Aloha
finishing.com - Pine Beach, New Jersey
Q. "Hi Paul. These are proprietary processes, so I think the suppliers' material safety data sheet may offer good info."
Unfortunately, they discuss the toxicity of the ingredients (selenious acid in particular--"may be fatal in small amounts"), but not the safety of the finished item.
- Renton, Washington USA
February 7, 2017
Q, A, or Comment on THIS thread -or- Start a NEW Thread